Calibração de Instrumentos de Pressão: Guia Completo
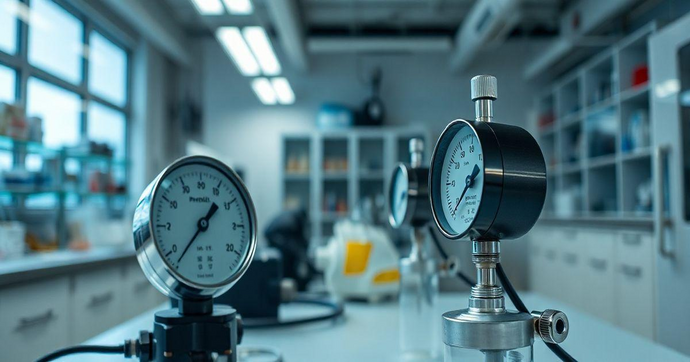
Por: Anderson - 24 de Dezembro de 2024
Calibração de instrumentos de pressão é um processo crucial para garantir a precisão nas medições e a segurança de diversos sistemas industriais. Neste artigo, vamos explorar a importância da calibração, os métodos mais utilizados, equipamentos necessários e as etapas essenciais para realizar essa tarefa de forma eficaz. Você também aprenderá sobre os erros comuns que podem ocorrer e como evitá-los, além de descobrir normas e regulamentações pertinentes. Continue lendo e aprofunde seu conhecimento sobre esse tema fundamental para a indústria.
Importância da Calibração de Instrumentos de Pressão
A calibração de instrumentos de pressão é um aspecto vital para garantir a precisão e a segurança em ambientes industriais. Esses instrumentos são utilizados em uma variedade de aplicações, desde processos químicos até manuseio de fluidos, e uma medição incorreta pode levar a consequências graves, incluindo falhas de equipamentos, desperdício de recursos e até mesmo riscos à segurança dos trabalhadores. Por essa razão, a calibração adequada é indispensável para manter a integridade do sistema.
Quando falamos da importância da calibração, é fundamental considerar diversos fatores que impactam tanto a eficiência operacional quanto a qualidade dos produtos. Primeiramente, instrumentos de pressão não calibrados correm o risco de apresentar leituras errôneas. Isso significa que a pressão elevada ou reduzida pode não ser detectada, levando a uma série de problemas, incluindo danos aos equipamentos e interrupções na produção. A calibragem regular ajuda a manter as medições dentro dos padrões estabelecidos, assegurando a operação contínua.
Além disso, a calibração é uma prática que ajuda a conformidade com normas e regulamentações do setor. Dependendo do tipo de indústria, pode haver exigências específicas para a calibração de instrumentos. Por exemplo, no setor farmacêutico, a precisão é crítica, pois pequenas variações podem afetar a eficácia de medicamentos. Portanto, garantir que os instrumentos estejam devidamente calibrados não é apenas uma boa prática, mas uma obrigação legal em alguns casos.
Outro ponto relevante é a questão econômica. A calibração adequada de instrumentos de pressão evita reparos dispendiosos e a substituição de equipamentos que podem ser causados por medidas imprecisas. Por exemplo, um equipamento que opera com pressão em níveis errados pode consumir mais energia e, consequentemente, aumentar os custos operacionais. Portanto, realizar calibrações regulares é uma forma eficaz de economizar dinheiro a longo prazo e aumentar a eficiência dos processos industriais.
Adicionalmente, a calibração também desempenha um papel importante na segurança dos trabalhadores. Instrumentos que medem pressão são frequentemente utilizados em ambientes que lidam com substâncias perigosas. Uma falha na medição pode resultar em acidentes, como explosões ou vazamentos, que podem ter consequências fatais. Garantir que esses instrumentos estejam sempre calibrados é uma responsabilidade crucial para a proteção dos profissionais que operam nesses locais.
É fundamental também destacar que a calibração não é uma atividade única, mas um processo contínuo. A calibração deve ser realizada em intervalos regulares, dependendo das recomendações do fabricante e das condições de operação. Fatores como variações de temperatura, umidade e vibração podem afetar a precisão dos instrumentos, tornando essencial a manutenção regular. Portanto, as empresas devem estabelecer um calendário de calibração que atenda aos requisitos específicos de cada instrumento usado em suas operações.
Além disso, a tecnologia tem avançado em muitos aspectos, oferecendo métodos inovadores e mais precisos para realizar a calibração de instrumentos. Hoje, o uso de dispositivos digitais e softwares avançados contribui para automatizar o processo, resultando em medições muito mais confiáveis e precisas. O investimento em tecnologia de calibração não apenas melhora a eficiência, mas também a confiança nos dados coletados.
Outra vantagem da calibração regular é a sua relação com a manutenção preventiva de equipamentos. Ao calibrar instrumentos de pressão, as empresas também podem identificar problemas potenciais antes que se tornem falhas graves. Por exemplo, a calibração de um sensor de pressão pode revelar um desgaste ou falha iminente, permitindo que a equipe realize uma manutenção de redutor antes que cause um tempo de inatividade significativo.
Por último, a calibração contribui para a melhoria contínua dos processos internos. Com medições precisas, as indústrias podem coletar dados mais confiáveis, permitindo a análise de desempenho e a implementação de melhorias. As informações extraídas de instrumentos bem calibrados podem fornecer insights sobre a eficiência operacional e identificar áreas que necessitam de ajustes, conduzindo a um ambiente de trabalho mais eficiente e seguro.
Em resumo, a calibração de instrumentos de pressão é um elemento essencial não apenas para a precisão das medições, mas também para a segurança, conformidade e eficiência econômica nas operações industriais. Por conta de sua importância, é fundamental que as organizações reconheçam a necessidade de práticas de calibração regulares e invistam nelas para obter benefícios a longo prazo em todos os aspectos de suas operações.
Métodos Comuns de Calibração
A calibração de instrumentos de pressão é uma prática fundamental para garantir a precisão em processos industriais. Existem diversos métodos de calibração, cada um com suas especificidades e métodos de execução. A escolha do método adequado pode impactar diretamente a confiabilidade das medições, a segurança dos processos e a eficiência operacional. Neste artigo, vamos explorar os métodos comuns de calibração de instrumentos de pressão e suas aplicações.
Um dos métodos mais utilizados é a calibração por comparação. Esse processo envolve a utilização de um instrumento de referência calibrado e certificado. O instrumento que precisa ser calibrado é colocado em paralelo ao instrumento de referência, e as leituras de ambos são comparadas em diferentes pontos de pressão. Se houver discrepâncias, o instrumento não calibrado pode ser ajustado até que suas leituras coincidam com as do instrumento de referência. Essa abordagem é eficaz e amplamente utilizada porque permite a identificação de erros com precisão e ajuda a manter os instrumentos funcionando em conformidade com as especificações.
Outro método é a calibração por ponto de ajuste. Este procedimento envolve o ajuste do instrumento durante sua operação normal para atingir um ponto específico de pressão previamente definido. Isso é ideal em situações onde o processo operacional exige que o instrumento esteja funcionando em uma determinada faixa. Durante esse tipo de calibração, a comparação é feita em um único ponto, e o ajuste é realizado apenas se os valores medidos estiverem fora da faixa tolerável. Além de ser um método simples, ele pode ser rápido e prático quando bem aplicado.
A calibração por simulação é outro método que merece destaque. Nesse caso, um simulador de pressão é utilizado para gerar pressões conhecidas. O instrumento a ser calibrado é conectado ao simulador, que estabelece várias pressões predeterminadas. Os dados são coletados e comparados com os valores padrão. Esse método é particularmente útil quando é necessário simular diversas condições rapidamente, e é ideal para instrumentos que não podem ser removidos de seus locais de operação, como em sistemas de processo integrados.
Além desses, a calibração digital está se tornando cada vez mais comum devido à evolução da tecnologia. Dispositivos digitais que oferecem funções avançadas, como armazenamento de dados, podem simplificar o processo de calibração. Esses instrumentos podem executar calibração automática, onde são programados para comparar as medições com padrões conhecidos e alertar os usuários sobre a necessidade de ajustes. Embora o investimento inicial em equipamentos digitais possa ser maior, a facilidade de uso e a precisão geralmente compensam esse custo ao longo do tempo.
Outro método importante é a calibração em condições controladas de temperatura e umidade. Para garantir medições precisas, é fundamental que as condições ambientais durante a calibração sejam controladas. Instrumentos que medem pressão podem apresentar variações em sua leitura devido a alterações nas condições ambientais. Ao calibrar em um ambiente controlado, os operadores podem evitar erros e obter resultados muito mais confiáveis.
As práticas de manutenção também são vitais para o desempenho de instrumentos de pressão. A Manutenção em redutores e outros componentes é necessária para garantir que todos os elementos estejam funcionando de forma ideal. Muitos métodos de calibração precisam ocorrer após a manutenção, pois mudanças nos equipamentos podem levar a variações nas medições. Portanto, a manutenção e a calibração andam lado a lado em qualquer operação industrial que utiliza instrumentos de pressão.
Não podemos esquecer da calibração por comparação cruzada, que utiliza dois instrumentos que medem o mesmo parâmetro, um conhecido e calibrado, enquanto o outro é o que precisa de calibração. Essa técnica é especialmente útil em situações onde a indústria apresenta um grande número de instrumentos similares, permitindo uma avaliação rápida e eficaz em campo, sem a necessidade de se interromper processos operacionais por longos períodos.
Cada um desses métodos de calibração traz suas vantagens e desvantagens, e a escolha do método ideal varia com base nas condições específicas de operação, no tipo de instrumento e na aplicação desejada. O conhecimento e a compreensão sobre esses métodos são essenciais para garantir a precisão e a confiabilidade das medições em ambientes industriais.
Além disso, as empresas devem considerar o treinamento de sua equipe para a realização adequada de calibrações. A calibração não deve ser realizada por pessoal não treinado, pois erros podem levar a leituras imprecisas e, consequentemente, a sérios problemas operacionais. Treinamentos regulares e a conscientização sobre os métodos de calibração são investimentos que trazem retornos significativos em precisão e segurança.
Em conclusão, a calibração de instrumentos de pressão é um passo crítico na manutenção da qualidade operacional e da segurança em processos industriais. Com a variedade de métodos de calibração disponíveis, escolher o mais adequado para as circunstâncias pode fazer toda a diferença na eficácia e na precisão das operações.
Equipamentos Necessários para Calibração
A calibração de instrumentos de pressão é uma prática fundamental em várias indústrias, sendo essencial para garantir a precisão e a segurança dos processos. No entanto, a calibração não pode ser realizada de forma eficaz sem o uso de equipamentos apropriados. Neste artigo, discutiremos os principais equipamentos necessários para a calibração de instrumentos de pressão e como cada um deles contribui para uma medição precisa e confiável.
Um dos equipamentos mais cruciais na calibração é o manômetro de referência, que é um instrumento de alta precisão utilizado como padrão para comparação. Esses manômetros, que podem ser digitais ou analógicos, devem ser calibrados e certificados regularmente para assegurar sua precisão. Visionar e comparar as leituras do manômetro de referência com os instrumentos em teste é uma prática comum que ajuda a identificar discrepâncias. A precisão do manômetro de referência é vital, pois qualquer erro nesse instrumento afetará a calibração dos demais instrumentos.
Outro equipamento importante é o calibrador de pressão. Esses dispositivos são projetados para gerar pressões conhecidas que podem ser usadas para testar e ajustar instrumentos de pressão. Existem diferentes tipos de calibradores, incluindo os manuais e os eletrônicos. Os calibradores eletrônicos geralmente oferecem funções avançadas, como a capacidade de armazenar leituras, realizar ajustes automáticos e operar com maior precisão. Ao escolher um calibrador, é essencial considerar a faixa de pressão que ele pode gerar, bem como a precisão requerida para a calibração dos instrumentos específicos.
Além do manômetro de referência e do calibrador de pressão, é necessário um sistema de conexão adequado, que pode incluir mangueiras e adaptadores. Esses acessórios são fundamentais para realizar as conexões entre os instrumentos a serem calibrados e os dispositivos de referência. Uma vedação adequada também é muito importante para evitar vazamentos durante o teste, pois vazamentos podem resultar em medições imprecisas e até danos aos equipamentos. Certifique-se de que os conectores e mangueiras utilizados são compatíveis e estão em boas condições.
É igualmente importante ter uma fonte de pressão, que pode ser uma bomba manual ou um sistema pneumático. As bombas manuais são frequentemente utilizadas em calibrações de baixa pressão e são uma opção prática e econômica. No entanto, para calibrações que requerem pressões mais altas ou em grandes volumes, um sistema pneumático pode ser mais adequado. Este último pode ser equipado com monitoramento digital da pressão, permitindo leituras mais precisas e controle automatizado do processo.
Além desses equipamentos principais, a Calibração de equipamentos laboratoriais é uma área que também exige várias ferramentas especializadas. Laboratórios frequentemente utilizam instrumentos como bússolas de pressão ou termômetros de referência para garantir que todos os parâmetros sejam monitorados com precisão.
Um sistema de registro e documentação é indispensável na calibração. Todos os dados coletados durante a calibração, incluindo medições iniciais, ajustes realizados e medições finais, devem ser documentados para futuras referências. Isso não apenas ajuda a manter um histórico claro de calibrações, mas também é um requisito em muitos ambientes regulados. O uso de software de calibração para gerenciar e registrar esses dados pode agilizar esse processo e garantir que as informações estejam sempre acessíveis.
Outro fator a ser considerado são as condições ambientais onde a calibração será realizada. Para garantir medições precisas, a temperatura e a umidade do ambiente devem ser monitoradas. A instalação de termômetros e higrômetros pode ajudar a controlar essas condições, garantindo que não haja variações ambientais que possam afetar os resultados da calibração.
Além da calibração de pressão, outros instrumentos de apoio podem ser necessários para fornecer um ambiente de trabalho seguro. É recomendável ter equipamentos de proteção individual (EPIs) disponíveis, como luvas, óculos de segurança e protetores auriculares, conforme necessário, principalmente em áreas industriais. Garantir a segurança dos operadores deve sempre ser uma prioridade.
Por último, mas não menos importante, o conhecimento e a experiência da equipe responsável pela calibração também são essenciais. Os operadores devem ser treinados na utilização de todos os equipamentos mencionados, além de entender os princípios envolvidos nas técnicas de calibração. O investimento em treinamento não apenas aumenta a segurança no processo, mas também garante que as calibrações sejam realizadas de forma eficaz e precisa.
Em resumo, a calibração de instrumentos de pressão requer uma variedade de equipamentos e ferramentas. A utilização de manômetros de referência, calibradores de pressão e fontes de pressão adequadas são fundamentais para que o processo de calibração seja realizado de modo eficaz. Além disso, a documentação precisa de todos os procedimentos e dados é imprescindível para a manutenção de um alto padrão de qualidade, segurança e eficiência nas operações industriais.
Passo a Passo da Calibração de Instrumentos de Pressão
A calibração de instrumentos de pressão é uma etapa fundamental para garantir a precisão e a segurança nos processos industriais. O procedimento de calibração pode parecer complexo, mas segue uma série de etapas lógicas que, quando seguidas corretamente, resultam em medições exatas. Neste artigo, apresentaremos um passo a passo detalhado sobre a calibração de instrumentos de pressão, orientando cada etapa do processo.
O primeiro passo para a calibração é a **preparação do local de trabalho**. É essencial garantir que a área onde a calibração ocorrerá esteja limpa e organizada. Isso minimiza o risco de contaminação dos instrumentos e interfereções indesejadas. Além disso, verifique se todas as ferramentas e equipamentos necessários estão disponíveis e em boas condições. Preparar um ambiente controlado em termos de temperatura e umidade também pode ser vantajoso, pois estes fatores podem influenciar as medições.
Após a preparação do espaço, o **próximo passo** é desconectar o instrumento de pressão que será calibrado. É importante seguir as recomendações do fabricante ao remover o dispositivo para evitar qualquer danos. Certifique-se de documentar a condição do instrumento antes da remoção e guarde todas as informações necessárias, como modelo, número de série e data de última calibração. Essa documentação pode ser útil mais tarde, quando você precisar realizar a manutenção ou obter informações sobre a calibração anterior.
Uma vez desconectado, o **próximo passo** é conectar o instrumento de referência, também conhecido como manômetro de referência, ao sistema. O manômetro de referência deve ser calibrado e certificado, pois será usado como padrão comparativo durante o processo. Conecte o instrumento de referência na mesma linha que o instrumento a ser calibrado, garantindo que houve uma vedação adequada para evitar vazamentos. Enquanto faz isso, verifique se as conexões não apresentam desgastes ou danos.
Agora que os instrumentos estão conectados, o **quarto passo** é gerar a pressão necessária. Se o seu sistema tiver um calibrador de pressão, ele será utilizado neste momento. Gradualmente, aumente a pressão até atingir os níveis especificados pelo fabricante do instrumento a ser calibrado. Normalmente, essa pressão é ajustada em incrementos e deve passar pela faixa total de operação do instrumento. Aumente e registre a pressão em intervalos. Isso garantirá que você não apenas realize a calibração adequadamente, mas também capture a resposta do instrumento em toda a sua faixa operativa.
O **próximo passo** envolve a coleta de dados. Com a pressão ajustada, observe as leituras do instrumento que está sendo calibrado e do manômetro de referência. É importante registrar as medições em um formato claro e organizado. Para cada incremento de pressão, anote a leitura do instrumento que está sendo testado e a do manômetro de referência. Esta comparação permitirá que você identifique qualquer discrepância entre as medições.
Após coletar os dados em todos os pontos de pressão, o próximo passo é **analisar os resultados**. Compare as leituras do instrumento em teste com as do manômetro de referência. Verifique se há desvios entre as duas leituras e considere o limite aceitável para cada instrumento. Se as discrepâncias forem excessivas, será necessário ajustar o instrumento calibrado. A calibração deve ser realizada conforme a especificação do fabricante, garantindo que o instrumento atenda à precisão desejada.
Se ajustes forem necessários, você deverá realizar as correções no instrumento. O processo de ajuste pode variar dependendo do tipo de instrumento e das instruções do fabricante. Durante a calibração de instrumentos de pressão, os ajustes frequentemente envolvem o uso de botões, chaves ou parafusos de ajuste localizados em algum lugar no corpo do instrumento. Após os ajustes, repita o procedimento de medição para confirmar que o instrumento agora está lendo dentro das tolerâncias especificadas.
Após a calibração bem-sucedida, é hora de **documentar os resultados**. Registre todos os dados, incluindo as medições coletadas, qualquer ajuste feito e as condições sob as quais a calibração foi realizada. Essa documentação é importante não só para manter um histórico do instrumento, mas também para conformidade com regulamentos e normas industriais. Algumas empresas também utilizam software de calibração para facilitar esse registro, garantindo uma gestão eficiente das informações coletadas.
Uma prática altamente recomendada durante o processo de calibração é acompanhar a **calibração de outros instrumentos relacionados**, como os Termômetros industriais que podem ser utilizados junto com os instrumentos de pressão. Manter a calibração sincronizada entre equipamentos correlatos assegura maior precisão nas medições e promove a eficiência operacional.
Por último, ao finalizar o processo, faça uma **verificação final** em todo o sistema. Isso envolve garantir que todas as conexões estejam seguras, que não haja vazamentos e que os instrumentos estejam no estado desejado para retornar à operação. Ao reconectar o instrumento ao sistema, faça uma checagem final para garantir que todas as funções estejam operando corretamente antes de colocá-lo em serviço novamente.
Em resumo, a calibração de instrumentos de pressão é um processo metódico que requer atenção a cada passo para assegurar a precisão e a segurança. Seguir essas etapas não só garante medições confiáveis, mas também otimiza o desempenho do sistema como um todo, contribuindo para a eficiência e a segurança nas operações industriais.
Erros Comuns na Calibração e Como Evitá-los
A calibração de instrumentos de pressão é um passo essencial para garantir a precisão e a confiabilidade nas medições em ambientes industriais. No entanto, várias armadilhas podem comprometer o processo de calibração, levando a erros que podem afetar o desempenho do sistema. Neste artigo, discutiremos os erros comuns que ocorrem durante a calibração e forneceremos orientações sobre como evitá-los.
Um dos erros mais frequentes na calibração é a **falta de preparação do ambiente de trabalho**. A calibração deve ser realizada em um local limpo e organizado, livre de interferências externas que possam afetar as medições. Uma área desorganizada pode levar à contaminação dos instrumentos ou ao uso ineficiente de ferramentas. Para evitar esse erro, é crucial dedicar um tempo para preparar o local antes de iniciar o processo de calibração. Certifique-se de que todos os instrumentos estão em boas condições e que todas as ferramentas necessárias estão à disposição.
Outro erro comum é **não verificar as especificações do fabricante** antes de iniciar a calibração. Cada instrumento pode ter requisitos específicos que devem ser observados, incluindo condições de temperatura, umidade e limites de pressão. Ignorar essas especificações pode resultar em medições imprecisas. Sempre consulte o manual do fabricante e siga suas recomendações para garantir que o processo de calibração ocorra dentro das diretrizes corretas. Isso pode fazer uma grande diferença nos resultados finais.
Durante a calibração, um erro comum é **não utilizar um manômetro de referência devidamente calibrado**. O manômetro de referência deve ser um instrumento de alta precisão, constantemente verificado e calibrado. Utilizar um instrumento de referência que não esteja em conformidade pode levar a resultados errôneos nas medições do instrumento em teste. Para evitar esse problema, mantenha um registro de calibração do manômetro de referência e certifique-se de que ele é verificado com frequência para garantir sua precisão.
Outro fator crítico é a **falta de um procedimento documentado** para a calibração. Trabalhar sem um processo claro pode levar a confusões e erros durante a calibragem. Documentar corretamente cada etapa, desde a preparação inicial até a coleta de dados, é essencial para manter a integridade do processo. Crie um procedimento padrão de operação (SOP) que detalhe cada etapa da calibração, incluindo as condições ambientais, os instrumentos utilizados e as leituras registradas. Isso não apenas ajuda a evitar erros, mas também serve como um guia para a equipe que realiza a calibração.
Um erro frequentemente cometido durante a calibração é **não levar em conta as condições ambientais**. Fatores como temperatura, umidade e pressão atmosférica podem afetar as medições dos instrumentos. Ignorar essas condições pode introduzir variáveis que comprometem a precisão. Para mitigar esse risco, sempre verifique as condições ambientais antes de calibrar. Se necessário, considere realizar a calibração em um ambiente controlado, onde as variáveis possam ser mantidas dentro de níveis aceitáveis.
Além disso, a **falta de manutenção nos instrumentos** também pode levar a medições imprecisas. Instrumentos que não recebem manutenção regular, como limpeza e inspeção, podem apresentar falhas ou desgastes que afetam seu desempenho. Regularmente, inspecione e realize a manutenção nos instrumentos para garantir que eles funcionem corretamente. Esse pequeno cuidado pode evitar muitos problemas no processo de calibração.
Um erro que pode ocorrer durante a coleta de dados é **não registrar as medições de forma adequada**. A anotação errada de dados ou a omissão de informações cruciais pode levar a um histórico de calibração incompleto ou impreciso. Para evitar esse problema, desenvolva um sistema de registro padronizado para anotar as medições durante a calibração. A utilização de formulários organizados ou softwares pode facilitar essa tarefa e garantir que todos os dados sejam coletados corretamente.
Um erro adicional comum é **não realizar calibrações regulares.** Muitos profissionais tendem a realizar a calibração somente quando percebem problemas de precisão, mas essa abordagem pode trazer consequências para os processos. A calibração deve ser realizada em intervalos regulares, conforme recomendado pelo fabricante e as normas do setor. Estabeleça um cronograma consistente de calibração para garantir que todos os instrumentos permaneçam dentro dos padrões estabelecidos.
Por último, a **falta de treinamento adequado da equipe responsável pela calibração** pode resultar em erros significativos. Mesmo os melhores equipamentos e processos podem falhar se a equipe não estiver bem treinada. Para evitar isso, ofereça treinamento regular e apropriado para todos os operadores envolvidos no processo de calibração. A capacitação contínua ajuda a manter a equipe atualizada sobre novas técnicas, equipamentos e melhores práticas.
Em conclusão, a calibração de instrumentos de pressão é um processo crítico que deve ser realizado com atenção aos detalhes. Reconhecer os erros comuns que podem ocorrer durante o processo e adotar medidas para evitá-los pode fazer toda a diferença na precisão das medições e na eficiência das operações. Com a preparação adequada, atenção às especificações do fabricante e investimento em formação, as empresas podem garantir que suas calibrações sejam realizadas com sucesso e que seus sistemas operem de forma eficiente e segura.
Fatores que Afetam a Precisão da Calibração
A calibração de instrumentos de pressão é uma atividade essencial para garantir a precisão e a confiabilidade nos processos industriais. No entanto, a precisão das medições pode ser influenciada por uma série de fatores externos e internos. Neste artigo, discutiremos os principais fatores que afetam a precisão da calibração e como cada um deles pode impactar os resultados finais.
Um dos fatores mais significativos que afetam a precisão da calibração é a **temperatura**. As medições de pressão podem ser sensíveis a variações de temperatura, pois as propriedades dos materiais dos instrumentos e dos fluidos em medições podem mudar com a temperatura. Por exemplo, um manômetro pode expandir ou contrair com o aumento ou diminuição da temperatura ambiente, o que altera a precisão da leitura. Para minimizar esses efeitos, é essencial calibrar os instrumentos em condições de temperatura controlada e registrar a temperatura durante os testes. Além disso, muitos instrumentos possuem especificações que limitam seu uso a determinadas faixas de temperatura, e ignorar essas diretrizes pode causar leituras erradas.
Outro fator crucial é a **umidade**. A umidade extrema pode afetar tanto o desempenho do instrumento quanto a integridade dos componentes eletrônicos dos instrumentos de medição. Instrumentos mal vedados podem sofrer a condensação interna se expostos a níveis elevados de umidade, resultando em falhas de medição temporárias ou permanentes. Para evitar problemas relacionados à umidade, é recomendável realizar a calibração em ambientes onde a umidade relativa seja controlada e documentar as condições ambientais que possam ter impactado os resultados.
Os **vibrações e choques** também desempenham um papel importante na precisão da calibração. Os instrumentos de pressão e seus componentes podem ser sensíveis a vibrações externas, o que pode ocasionar leituras erradas. Durante a calibração, qualquer vibração percebida pode ser amplificada e resultar em flutuações nas leituras das medições. Para mitigar esse problema, recomenda-se realizar a calibração em uma superfície estável e, se possível, utilizar suportes que absorvam vibrações. Também pode ser útil realizar medições em diferentes condições operacionais para garantir a precisão das medições em situações reais.
A **qualidade do manômetro de referência** utilizado é outro fator crítico. Para garantir medições precisas, é essencial que o manômetro de referência seja calibrado e certificado regularmente. Um manômetro de baixa qualidade ou não calibrado pode influenciar negativamente os resultados da calibração, mesmo que todos os outros fatores estejam controlados. Sempre verifique o histórico de calibração do manômetro de referência e faça uso de padrões de alta precisão. Isso garante que suas medições sejam confiáveis.
Além disso, o **desgaste dos instrumentos** ao longo do tempo pode afetar substancialmente a precisão de suas medições. Instrumentos que não passam por manutenção adequada podem apresentar problemas, como vazamentos ou falhas mecânicas. A manutenção regular é crucial para garantir que os instrumentos estejam funcionando nas especificações corretas. Criar um cronograma de manutenção e garantir que todos os instrumentos tenham um histórico de cuidados pode ajudar a prolongar sua vida útil e sua precisão.
A **altura sobre o nível do mar** e a **pressão atmosférica** são fatores igualmente relevantes. A pressão do ar em altitudes diferentes pode interferir na leitura de instrumentos de pressão. Por exemplo, em grandes altitudes, a pressão atmosférica é menor, o que pode causar leituras falsas em instrumentos calibrados para níveis do mar. Se seu processo envolve medições em diferentes altitudes, é importante ajustar os instrumentos conforme necessário. A calibração deve ser realizada considerando a altura onde o instrumento será utilizado.
O **tempo de resposta do instrumento** também pode afetar a precisão. Quando um instrumento de pressão é exposto a uma alteração repentina na pressão, ele pode levar um tempo para se estabilizar e fornecer uma leitura precisa. Certifique-se de que os operadores saibam esperar o tempo necessário para que os instrumentos estabilizem as leituras antes de registrar os dados. Essa prática simples pode melhorar significativamente a precisão das medições.
Outro fator que pode contribuir para imprecisões na calibração é a **maneira como os dados são registrados e analisados**. A falta de um processo documental adequado pode levar a erros de interpretação de dados. Para evitar problemas, é importante que todos os operadores saibam como registrar dados com precisão e que exista um sistema organizado para essa documentação. Isso não apenas melhora a precisão, mas também proporciona uma trilha clara de auditoria para revisões futuras.
Por último, mas não menos importante, a **experiência e o conhecimento da equipe responsável** pela calibração influenciam diretamente a precisão das medições. Um operador experiente é mais capaz de identificar e corrigir problemas potenciais antes que eles afetem os resultados. Por isso, é imprescindível proporcionar formação contínua e desenvolvimento profissional para a equipe que realiza a calibração. O treinamento sobre novos equipamentos ou técnicas também poderá melhorar o conhecimento da equipe e a qualidade do trabalho realizado.
Em suma, a precisão da calibração de instrumentos de pressão pode ser afetada por uma série de fatores ambientais e funcionais. Compreender e mitigar esses fatores é essencial para garantir medições confiáveis e seguras. Ao considerar a temperatura, umidade, vibração, qualidade dos instrumentos, manutenção e outros fatores discutidos, você pode otimizar o processo de calibração e manter a integridade dos seus sistemas de medição.
Normas e Regulamentações na Calibração de Instrumentos
A calibração de instrumentos é uma prática vital para garantir a precisão e a confiabilidade das medições em diversas indústrias. Para assegurar que os processos de calibração sejam realizados de maneira eficaz, existem normas e regulamentações que orientam as melhores práticas e garantem conformidade com os padrões industriais. Neste artigo, exploraremos as principais normas e regulamentações que regem a calibração de instrumentos, discutindo sua importância e aplicação no dia a dia das operações industriais.
Uma das normas mais reconhecidas globalmente é a **ISO 9001**, que estabelece requisitos para um sistema de gestão da qualidade. Embora essa norma não se concentre exclusivamente na calibração, sua implementação exige que as organizações documentem processos críticos, incluindo a calibração de instrumentos. A ISO 9001 busca garantir que as empresas mantenham um padrão de qualidade em todas as suas operações e assegura que os produtos ou serviços entregues atendam às expectativas dos clientes. A calibração adequada de instrumentos é um componente essencial para cumprir essas exigências de qualidade, visto que medições precisas são fundamentais para o controle de processos e para a produção de produtos seguros e eficazes.
Outra norma importante é a **ISO/IEC 17025**, que especifica os requisitos gerais para a competência de laboratórios de ensaio e calibração. Esta norma é específica para laboratórios que realizam calibrações e ensaios, sendo um referencial essencial para garantir a precisão dos resultados obtidos. O cumprimento da ISO/IEC 17025 garante que o laboratório tenha a competência técnica necessária e assegura que as calibrações sejam realizadas de maneira confiável. A norma abrange aspectos como rastreabilidade das medições, validação de métodos de calibração e gestão da qualidade, ajudando a promover a consistência nos resultados.
As **normas da ASTM International** também desempenham um papel significativo na calibração. A ASTM possui uma série de normas que fornecem diretrizes específicas para a calibração de diferentes tipos de instrumentos. Por exemplo, normas como ASTM E2877 e ASTM E2339 estabelecem métodos e práticas para garantir a precisão na calibração de manômetros e outros instrumentos de medição. As normas da ASTM são amplamente utilizadas em setores como fabricação, engenharia e ciências da vida, onde a precisão é sinônimo de segurança e eficácia.
Além das normas internacionais, é importante considerar as **regulamentações locais e nacionais** que afetam a calibração de instrumentos. Em muitos países, órgãos reguladores, como a ANVISA no Brasil, exigem que dispositivos médicos e equipamentos utilizados na produção farmacêutica sejam calibrados de acordo com normas específicas. Essas regulamentações visam garantir não apenas a qualidade dos produtos, mas também a segurança do consumidor. Assim, as empresas precisam estar atentas às exigências locais para garantir que os seus processos de calibração estejam em conformidade, evitando possíveis penalidades legais.
A conformidade com as regulamentações técnicas e normas também é fundamental para as empresas que desejam obter certificações e acreditações. Por exemplo, a acreditação de laboratórios de calibração pode ser obtida mediante o cumprimento de certas normas, como a ISO/IEC 17025. Essa acreditação assegura aos clientes que a empresa opera de acordo com padrões reconhecidos internacionalmente, instilando confiança em sua capacidade de realizar calibrações precisas e confiáveis. Ter modelos de qualidade estabelecidos pode também abrir portas para oportunidades comerciais e parcerias essenciais.
Investir em um programa de calibração que atenda a essas normas não é apenas uma questão de conformidade; é uma estratégia que pode contribuir para a eficiência operacional. Por exemplo, a implementação de boas práticas de calibração de acordo com as normas pode levar a uma redução de desperdícios, melhorias na produtividade e uma diminuição dos custos relacionados à falhas dos instrumentos. Empresas que se comprometem a seguir normas e regulamentações tendem a se destacar no mercado, evidenciando não apenas um compromisso com a qualidade, mas também uma atitude responsável em relação à segurança.
Além das normas previamente mencionadas, a **DIN ISO 10012** merece destaque. Esta norma estabelece diretrizes para a gestão da metrologia e é aplicada principalmente em indústrias que utilizam medições e calibrações como parte de seus processos. O cumprimento das diretrizes da DIN ISO 10012 ajuda as empresas a assegurar que os seus instrumentos e processos de calibração estejam em conformidade com padrões reconhecidos, ao mesmo tempo em que promove uma cultura de qualidade e eficiência.
Por fim, as empresas que operam em nível internacional devem estar cientes de que as normas e regulamentações podem variar significativamente entre diferentes países e regiões. Isso significa que a empresa pode precisar adaptar seus processos de calibração para atender a requisitos locais. Para garantir conformidade, muitas organizações estabelecem sistemas de gestão que incluem auditorias regulares e treinamentos para a equipe sobre as normas relevantes. Essa abordagem ajuda a minimizar riscos e a garantir que todas as medições feitas estejam em conformidade com as normas aplicáveis.
Em resumo, a calibração de instrumentos é um componente crucial para garantir a qualidade e a segurança nas operações industriais. A conformidade com normas e regulamentações, como ISO 9001, ISO/IEC 17025 e AST, é fundamental para assegurar que as calibrações sejam feitas de maneira competente e confiável. A observância dessas normas não apenas assegura a precisão das medições, mas também contribui para o fortalecimento da reputação e da eficiência das organizações. Portanto, investir tempo e recursos para entender e implementar essas diretrizes é essencial para o sucesso e a durabilidade no mercado competitivo atual.
Manutenção e Verificação de Instrumentos de Pressão
A manutenção e verificação de instrumentos de pressão são atividades fundamentais para assegurar a precisão, a eficiência e a segurança em diversos processos industriais. Instrumentos de pressão, como manômetros, transmissores e medidores, desempenham um papel crucial em várias operações, desde controle de processos até medições críticas em ambientes de trabalho. Neste artigo, abordaremos a importância da manutenção e verificação desses instrumentos, além de discutir as melhores práticas para garantir o seu desempenho ideal.
A **manutenção** regular de instrumentos de pressão é essencial para evitar falhas e garantir que as medições sejam sempre precisas. Cada tipo de instrumento possui requisitos específicos de manutenção, que devem ser seguidos de acordo com as recomendações do fabricante. Essas recomendações podem incluir a limpeza, o ajuste e a substituição de peças desgastadas. Ignorar essa manutenção pode resultar em medições imprecisas, que podem levar a decisões erradas em processos críticos e aumentar o risco de falhas operacionais.
É importante estabelecer um **cronograma de manutenção** que se baseie nas recomendações do fabricante e na frequência de uso dos instrumentos. Além disso, alguns setores possuem regulamentações específicas que exigem manutenções em intervalos determinados, especialmente em indústrias como a farmacêutica e a alimentícia. A documentação cuidadosa de todas as atividades de manutenção é fundamental, pois proporciona um histórico confiável do desempenho do instrumento e assegura conformidade com normas e regulamentos.
Além da manutenção programada, a **verificação frequente** dos instrumentos de pressão é igualmente importante. Verificações podem incluir testes de desempenho, que devem ser realizados em intervalos regulares para garantir que os instrumentos estejam funcionando corretamente e com a precisão necessária. Durante o processo de verificação, os instrumentos são submetidos a testes que comparam suas leituras com padrões conhecidos e calibratedores, permitindo identificar rapidamente quaisquer desvios que possam ocorrer.
Outra prática recomendada é a **calibração regular** dos instrumentos de pressão. A calibração e a verificação trabalham em conjunto para garantir a precisão. A calibração deve ser realizada com pelo menos uma frequência definida, mas em condições de operação variável ou em situações onde a segurança é um aspecto preocupante, como em indústrias químicas, uma calibração mais frequente pode ser necessária. O objetivo é garantir que todas as leituras estejam dentro das tolerâncias especificadas pelo fabricante e que os instrumentos estejam aptos para fornecer medições confiáveis. Durante a calibração, deve-se fazer um teste com um manômetro de referência devidamente calibrado, o que assegura a precisão dos dados obtidos.
É fundamental que os operadores e a equipe de manutenção estejam **treinados e capacitados** para operar, manter e verificar os instrumentos de pressão. O conhecimento sobre o funcionamento dos dispositivos é essencial para a identificação precoce de sinais de falha e para a realização de manutenções corretivas quando necessário. O treinamento regular e a atualização sobre as melhores práticas são investimentos que podem resultar em economias significativas e na prevenção de falhas dispendiosas.
Além da manutenção e calibração, outro aspecto importante é a **condição do ambiente** onde os instrumentos estão instalados. Fatores como temperatura, umidade, vibração e poluição podem afetar o desempenho dos instrumentos de pressão. É essencial que as instalações sejam planejadas de forma a minimizar a exposição a condições ambientais adversas. Em ambientes com exigências rigorosas, como salas limpas ou locais com vapores químicos agressivos, a proteção adequada dos instrumentos é vital para assegurar funcionalidade e longevidade.
Um aspecto muitas vezes negligenciado na manutenção de instrumentos de pressão é a **limpeza**. Poeira, sujeira e contaminantes podem acumular-se, podendo afetar diretamente a precisão do instrumento. É recomendável seguir as diretrizes do fabricante para a limpeza, utilizando os produtos adequados que não danifiquem os dispositivos. Um programa de limpeza regular deve ser implementado, especialmente em ambientes onde a conformidade com normas rigorosas é exigida.
Outra prática recomendada é a **substituição de peças desgastadas**. Componentes do instrumento, como vedações, flanges e conectores, podem se deteriorar com o tempo devido ao uso contínuo e à exposição ao ambiente. É importante manter um estoque adequado de peças de reposição e realizar a troca das peças desgastadas conforme se torna necessário. A programação dessa substituição não só ajuda a manter as medições precisas, mas também estende a vida útil do instrumento.
Implementar um sistema de **gestão de manutenção** pode ser extremamente benéfico. Isso envolve a utilização de softwares de gestão que possibilitam o acompanhamento da manutenção e do desempenho dos instrumentos. Esses sistemas permitem agendar automaticamente as manutenções, registrar quando as calibrações devem ser feitas e gerenciar as peças de reposição. Além disso, um sistema de gestão pode ajudar a fornecer informações valiosas para análises de desempenho e melhoria contínua.
Finalmente, a **documentação inadequada** pode levar a um histórico impreciso e impactar a eficácia dos processos de manutenção e verificação. Manter um registro detalhado de todas as manutenções realizadas, calibrações, verificações e qualquer incidente relacionado ao desempenho dos instrumentos é essencial. Essa documentação fornece uma visão clara do histórico de cada instrumento, ajudando na identificação de padrões de desempenho e potenciais problemas recorrentes.
Em resumo, a manutenção e verificação de instrumentos de pressão são atividades cruciais para garantir a precisão e confiabilidade nas medições, assegurando a segurança e a eficiência nas operações industriais. Estabelecer rotinas de manutenção programada, realizar verificações regulares, garantir a capacitação da equipe e adotar melhores práticas garante que os instrumentos funcionem da maneira desejada e atendam aos requisitos exigidos pela indústria. A implementação de um sistema de gestão eficaz e a atenção ao ambiente onde os instrumentos estão instalados apenas reforçam o papel vital que a manutenção e verificação desempenham na indústria moderna.
Em conclusão, a calibração de instrumentos de pressão é um passo fundamental para assegurar não apenas a precisão das medições, mas também a segurança e eficiência nos processos industriais. Através da compreensão da importância da calibração, dos métodos adequados, dos equipamentos necessários e das práticas de manutenção, as empresas podem garantir que seus instrumentos funcionem sempre em sua melhor forma. Além de minimizar os erros comuns e seguir as normas e regulamentações estabelecidas, investir em treinamento contínuo para as equipes envolvidas na calibração é essencial para manter a qualidade dos processos. Assim, ao adotar uma abordagem proativa em relação à calibração e à manutenção, as organizações não apenas melhoram sua eficiência operacional, mas também fortalecem seu comprometimento com a segurança e qualidade, promovendo uma cultura de excelência em todas as suas operações.