Manutenção Preventiva de Redutores: Dicas Essenciais
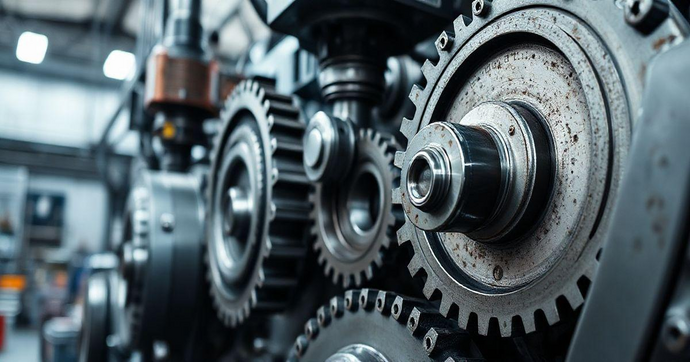
Por: Anderson - 24 de Dezembro de 2024
Manutenção preventiva de redutores é fundamental para garantir a eficiência e durabilidade dos equipamentos industriais. Ao longo deste artigo, vamos explorar a importância de manter redutores em bom estado, os principais tipos de redutores e como realizar a manutenção de forma efetiva. Você aprenderá sobre os sinais que indicam a necessidade de manutenção e os benefícios que isso traz para sua operação. Continue lendo para descobrir dicas práticas e assegurar o desempenho otimizado dos seus redutores.
Importância da Manutenção Preventiva de Redutores
A manutenção preventiva de redutores é uma prática essencial que não deve ser subestimada em nenhum ambiente industrial. Redutores são equipamentos que desempenham um papel crucial na transmissão de potência, convertendo a energia mecânica de um motor para um movimento adequado ao tipo de atividade que está sendo realizada. Por isso, compreendê-los e garantir sua regular manutenção é fundamental para o sucesso de qualquer operação.
Um dos principais benefícios da manutenção preventiva é a redução de falhas inesperadas. Assim como qualquer equipamento mecânico, redutores estão expostos ao desgaste natural e, se não forem monitorados regularmente, podem sofrer avarias que comprometem seu funcionamento. As falhas de redutores podem causar paradas não programadas, resultando em perda de produtividade e custos extras para a manutenção corretiva. Portanto, realizar manutenções periódicas ajuda a identificar problemas antes que eles se tornem críticos.
A manutenção preventiva permite também uma maior vida útil dos redutores. Equipamentos bem mantidos tendem a operar de forma mais eficiente e podem durar anos adicionais em comparação com aqueles que não recebem o cuidado adequado. Essa durabilidade é especialmente importante em indústrias onde a operação contínua é necessária. Ao evitar um desgaste excessivo e garantir a troca de lubrificantes e componentes desgastados, você maximiza a eficiência e prolonga a vida útil do seu redutor.
Outro aspecto relevante é que a manutenção preventiva de redutores pode contribuir para a melhora geral na eficiência energética da operação. Redutores que não estão em boas condições muitas vezes exigem mais energia para funcionar, aumentando o consumo energético e, consequentemente, os custos operacionais. Através de uma manutenção regular, os redutores são capazes de operar em seu ótimo nível de eficiência, reduzindo o consumo de energia e, ao mesmo tempo, diminuindo as emissões de carbono e o impacto ambiental.
O monitoramento e a manutenção preventiva não apenas previnem falhas, mas também asseguram que os redutores estejam operando dentro das especificações do fabricante. Isso inclui a verificação de alinhamentos, a lubrificação adequada e o ajuste de tensões nos componentes. Em instalações industriais complexas, manter os equipamentos em conformidade com as diretrizes do fabricante minimiza o risco de equipamentos subdimensionados ou sobrecarregados, gerando um ambiente de trabalho mais seguro e eficiente.
A comunicação e a documentação das manutenções realizadas também são parte do processo de manutenção preventiva eficaz. Manter registros detalhados das manutenções e inspeções realizadas nos redutores ajuda não só a acompanhar o histórico e o desempenho dos equipamentos, mas também a antecipar a necessidade de trocas ou intervenções maiores. Quando toda a equipe está ciente do status dos redutores, ela pode agir prontamente ao notar qualquer irregularidade, evitando problemas futuros.
Num mercado crescente e competitivo, a manutenção preventiva atua como uma vantagem estratégica. Muitas empresas que adotam essa prática não apenas veem um aumento na produtividade, como também constroem uma reputação de confiabilidade e segurança. Clientes e parceiros de negócios são atraídos por organizações que demonstram compromisso com a qualidade e a continuidade operacional.
Finalmente, é importante ressaltar que a capacitação da equipe que realiza a manutenção é crucial para o sucesso do processo. Investir em treinamentos e atualizações para os colaboradores, permitindo que eles compreendam os princípios de funcionamento dos redutores e as melhores práticas de manutenção, fará com que a empresa colha todos os benefícios que a manutenção preventiva tem a oferecer. Um bom treinamento garante que os trabalhadores estejam aptos a identificar anomalias e executar manutenções de acordo com as normas de segurança.
Em resumo, a manutenção preventiva de redutores é uma prática indispensável para manter a eficiência operacional e a segurança do ambiente industrial. Compreender sua importância e implementar um programa de manutenção regular pode fazer toda a diferença na produtividade e na rentabilidade de uma empresa. Para mais informações sobre como realizar a manutenção de redutor, acesse o link e conheça as melhores práticas.
Principais Tipos de Redutores e suas Manutenções
Os redutores desempenham um papel essencial na transmissão de potência em diversos tipos de máquinas e mecanismos. Eles são responsáveis por reduzir a velocidade de rotação de um motor, aumentando assim o torque que é transmitido para o equipamento acionado. Existem vários tipos de redutores, e cada um possui características específicas que influenciam diretamente suas manutenções. Neste artigo, discutiremos os principais tipos de redutores e as manutenções adequadas para garantir seu funcionamento eficaz.
Os redutores podem ser classificados em diferentes categorias. Entre os mais comuns, encontramos os redutores planetários, redutores de engrenagem helicoidal, redutores cônicos e redutores de corrente. Cada um desses tipos apresenta vantagens e desvantagens distintas, além de exigências específicas de manutenção.
Redutores Planetários: Os redutores planetários são conhecidos por sua eficiência e compacto design. Eles utilizam um conjunto de engrenagens que incluem um sol e planetas, permitindo uma redução significativa de velocidade e um aumento no torque. Para garantir o bom funcionamento dos redutores planetários, é indispensável realizar suas manutenções periodicamente. Isso inclui verificar o nível e a condição do lubrificante, além de inspecionar as engrenagens em busca de desgastes ou quebras. A troca do lubrificante deve ser feita de acordo com as indicações do fabricante, e o alinhamento do redutor deve ser checado para evitar desgastes irregulares.
Redutores de Engrenagem Helicoidal: Os redutores de engrenagem helicoidal são amplamente utilizados em aplicações que requerem uma operação silenciosa e uma construção robusta. Esses redutores são frequentemente utilizados em sistemas de transporte e maquinários pesados. A manutenção desses redutores inclui a revisão regular dos níveis de óleo, assim como a limpeza dos sistemas de resfriamento. Verificar a condição das engrenagens e a presença de folgas excessivas é essencial, pois qualquer desgaste pode comprometer a eficiência do redutor. Além disso, é necessário monitorar a temperatura de operação para prevenir superaquecimentos.
Redutores Cônicos: A principal característica dos redutores cônicos é a capacidade de fazer a alteração da direção do movimento. Esses redutores são utilizados frequentemente em aplicações em que é necessário um ângulo de saída diferente da entrada. Manutenções para redutores cônicos envolvem a verificação do estado dos rolamentos e a lubrificação regular do sistema. Devido à sua configuração, dispositivos cônicos podem acumular contaminantes mais facilmente, o que torna a limpeza regular fundamental. Assim, deve-se garantir que não haja obstruções em suas engrenagens, e a verificação de folgas deve ser feita com atenção. Ajustes podem ser necessários para garantir que o redutor opere dentro das especificações corretas.
Redutores de Corrente: Os redutores de corrente são uma solução robusta para aplicações que requerem altas cargas e longas distâncias de transmissão. Esses redutores geralmente precisam de manutenção menos frequente, mas ainda assim é importante verificar o estado da corrente e as tensões em intervalos regulares. A lubrificação da corrente é vital para prevenir desgastes excessivos. Se a corrente estiver esticada ou desgastada, isso pode causar falhas no equipamento e até acidentes. Portanto, a manutenção deve incluir a inspeção dos elos da corrente e a aplicação de lubrificante apropriado.
A manutenção regular é a chave para garantir que todos os tipos de redutores operem eficazmente e por longos períodos. Independentemente do tipo de redutor em uso, é essencial seguir as recomendações do fabricante a respeito de intervalos de manutenção e procedimentos específicos. Além disso, a formação da equipe que manuseia esses equipamentos é crítica. A compreensão das diferentes exigências de manutenção pode ajudar a prevenir problemas e a prolongar a vida útil dos redutores.
Com a implementação de um plano de manutenção efetivo, as empresas podem evitar custos operacionais desnecessários e interrupções na produção. Um bom planejamento inclui a programação de inspeções, a verificação do estado de componentes críticos e a realização de trocas de lubrificantes e reparos conforme necessário. Para mais informações sobre como realizar a manutenção em redutores, entre no link e conheça as melhores práticas para garantir o melhor desempenho dos seus redutores.
Quando Realizar a Manutenção Preventiva?
Realizar a manutenção preventiva de redutores é uma prática fundamental para garantir o funcionamento eficiente e seguro dos equipamentos. Entretanto, muitos se perguntam: quando exatamente essa manutenção deve ser realizada? A resposta é que a manutenção preventiva deve ser encarada como uma atividade contínua e planejada, que deve ocorrer em intervalos regulares, além de ser repleta de ações pontuais em resposta a situações específicas que possam surgir.
A primeira consideração a se ter em mente é o plano de manutenção preconizado pelo fabricante do redutor. Esse plano geralmente inclui recomendações sobre a periodicidade das manutenções, que podem variar de acordo com o tipo de redutor, a aplicação e as condições operacionais. Por exemplo, redutores que operam em ambientes mais agressivos ou com cargas mais altas podem necessitar de manutenções mais frequentes. Portanto, é imprescindível consultar o manual do fabricante e seguir as orientações dadas.
Além dos períodos fixos de manutenção previstos, existem situações que demandam manutenções extraordinárias. Um sinal claro de que é hora de realizar uma manutenção preventiva é a presença de ruídos anormais durante a operação. Esses ruídos podem indicar desgastes nas engrenagens ou problemas com os rolamentos, que, se não abordados, podem levar a falhas maiores e mais onerosas. Assim, se um operador notar qualquer ruído que não seja habitual, deve-se programar uma manutenção preventiva o quanto antes.
Outro ponto a ser observado é a temperatura de operação do redutor. A monitorização contínua da temperatura é uma prática recomendada, pois um aumento acentuado pode ser um indicativo de problemas internos, como falta de lubrificação ou componentes desgastados. Quando se constata que a temperatura excede os limites estabelecidos, a execução de uma manutenção preventiva deve ser imediata para evitar danos ainda mais severos ao equipamento.
A vibração excessiva é outro fator a ser considerado. O uso de softwares de monitoramento que analisem as vibrações dos redutores pode ser uma ótima estratégia. As variações nas vibrações podem indicar desalinhamentos ou desgastes nos componentes. Nesse caso, a melhor prática é realizar uma manutenção preventiva regularmente e antes que esses problemas se tornem impeditivos para o ciclo produtivo.
Outro ponto importante a ser destacado é a troca de lubrificantes. A lubrificação regular dos redutores é crucial para o seu bom funcionamento. Seguir as recomendações do fabricante sobre a periodicidade da troca de óleo ou graxa pode prevenir falhas e prolongar a vida útil do equipamento. Em geral, a troca deve ser realizada em intervalos específicos ou quando os lubrificantes apresentarem mudanças em sua viscosidade, coloração ou presença de contaminantes.
Além das manutenções programadas e situações de emergência, a realização de inspeções visuais periódicas também faz parte do regime de manutenção preventiva. Olhar atentamente para os componentes do redutor em busca de sinais de desgaste, corrosão ou vazamentos pode evitar problemas futuros. Identificar pequenos problemas desde cedo pode permitir intervenções menos custosas em comparação com uma manutenção corretiva, que muitas vezes envolve a troca completa do equipamento ou de suas partes.
Em indústrias onde a segurança é primordial, como em fábricas de produtos químicos ou metalúrgicas, a manutenção preventiva deve seguir uma programação rigorosa. Em cenários onde a integridade dos trabalhadores está em risco devido a possíveis falhas de equipamentos, é recomendável realizar auditorias de manutenção. Essas auditorias permitem que se identifiquem as áreas críticas que precisam de atenção especial, criando um plano ágil e eficaz de ação.
A calibração também deve ser levada em consideração, especialmente em ambientes industriais sensíveis, onde equipamentos laboratoriais possam estar envolvidos. A calibração de equipamentos laboratoriais é uma parte essencial para garantir a precisão e a segurança no funcionamento de máquinas e processos, o que também se relaciona diretamente à eficácia dos redutores. Por isso, é fundamental verificar a calibragem quando novos equipamentos são adicionados ou sempre que uma manutenção significativa for feita no redutor.
Em resumo, a manutenção preventiva deve ser uma parte integrante da rotina de operação dos redutores, com atenção especial a períodos e situações que justifiquem intervenções. A criação de um cronograma detalhado, juntamente com a observação constante do desempenho e das condições dos equipamentos, garantirá que a manutenção seja realizada de forma eficaz e, consequentemente, resultará em um aumento da produtividade e da segurança na operação industrial.
Passos para uma Manutenção Efetiva de Redutores
A manutenção efetiva de redutores é um componente crucial para garantir a eficiência operacional, a segurança e a durabilidade dos equipamentos em qualquer ambiente industrial. Realizar uma manutenção adequada não apenas aprimora a performance dos redutores, mas também minimiza o risco de falhas e paradas não programadas. A seguir, detalharemos os principais passos para implementar uma manutenção eficaz dos redutores, abordando desde a inspeção regular até a troca de componentes.
1. Elaboração de um Plano de Manutenção
O primeiro passo para uma manutenção efetiva é desenvolver um plano abrangente que inclua todas as atividades de manutenção programada, inspeções e os intervalos de tempo para a realização dessas tarefas. Esse plano deve ser baseado nas orientações do fabricante e nas condições de operação do redutor. Ter um cronograma organizado ajuda a garantir que nenhuma atividade essencial seja esquecida e que a manutenção ocorra em tempo hábil.
2. Treinamento da Equipe
Um dos fatores mais importantes para uma manutenção bem-sucedida é garantir que toda a equipe envolvida esteja devidamente treinada. O conhecimento técnico sobre os redutores, incluindo suas especificações e os procedimentos de manutenção, é essencial para a execução eficaz das manutenções. Investir no treinamento contínuo da equipe também garante que eles estejam atualizados com as melhores práticas e técnicas de manutenção.
3. Inspeções Visuais Regulares
Realizar inspeções visuais regulares nos redutores é uma etapa fundamental. Durante essas inspeções, os operadores devem procurar sinais de desgaste, vazamentos de lubrificante, corrosão ou quaisquer anomalias que possam indicar um problema iminente. Qualquer sinal de preocupação deve ser registrado e tratado imediatamente para evitar falhas mais graves. A rotina de inspeções deve ser documentada para referência futura.
4. Monitoramento de Temperatura e Vibração
O monitoramento constante da temperatura e da vibração dos redutores é uma prática eficaz para detectar problemas antes que eles se tornem críticos. Equipamentos como termômetros industriais e sensores de vibração podem ser utilizados para garantir que os redutores estejam operando dentro das especificações. Se os parâmetros de temperatura ou vibração excederem os níveis normais, isso pode ser indicativo de superfícies de contato inadequadas, falta de lubrificação ou desalinhamento, os quais requerem atenção imediata.
5. Lubrificação Adequada
A lubrificação é um aspecto crítico na manutenção de redutores. O óleo ou graxa devem ser trocados de acordo com as especificações do fabricante e o ambiente de operação. A falta de lubrificante ou a presença de contaminação podem levar a um desgaste acelerado das engrenagens, resultando em falhas graves. É importante não apenas realizar as trocas dentro dos prazos, mas também verificar o nível e a condição do lubrificante, assegurando que ele esteja limpo e na quantidade adequada.
6. Verificação e Substituição de Componentes
Durante a manutenção, é vital inspecionar todos os componentes do redutor, incluindo rolamentos, engrenagens e vedantes. A sua verificação regular ajuda a identificar peças que precisam ser ajustadas, lubrificadas ou substituídas. Sempre que um componente vital mostrar sinais de desgaste excessivo, ele deve ser substituído prontamente para evitar falhas futuras. Os registros de trocas de componentes devem ser mantidos para uma melhor gestão do ciclo de vida do equipamento.
7. Alinhamento Adequado
O alinhamento correto entre o motor e o redutor é vital para o funcionamento eficaz. Um desalinhamento pode causar vibrações excessivas e prejudicar a eficiência do equipamento. Verificar o alinhamento e realizar os ajustes necessários deve ser parte do protocolo de manutenção regular. Isso não apenas ajuda na retenção da eficiência, mas também reduz o desgaste e prolonga a vida útil dos redutores e dos motores.
8. Documentação e Registro de Atividades
Todas as atividades de manutenção devem ser documentadas minuciosamente. Esse registro deve incluir as datas das inspeções, as ações realizadas, os materiais utilizados e quaisquer problemas encontrados. A documentação ajuda a monitorar o desempenho dos redutores ao longo do tempo e permite que os operadores identifiquem padrões de falhas recorrentes, possibilitando ajustes nas manutenções futuras para melhorar a eficácia geral.
9. Avaliação de Desempenho
Finalmente, é importante avaliar periodicamente a eficácia da manutenção realizada. Medir a frequência de falhas, o tempo de inatividade e a eficiência dos redutores podem fornecer informações sobre a qualidade do plano de manutenção e indicar áreas que podem ser melhoradas. Essa avaliação contínua é essencial para garantir que seus métodos de manutenção estejam sempre atualizados e sejam eficazes.
A manutenção efetiva de redutores é uma combinação dessas etapas, todas interconectadas e essenciais para o sucesso geral da operação. Implementar um regime de manutenção estruturado e contínuo garantirá que seus redutores operem de maneira eficiente e segura, reduzindo custos e aumentando a produtividade no ambiente industrial.
Sinais de Que o Redutor Precisa de Manutenção
A manutenção preventiva de redutores é fundamental para garantir o funcionamento eficaz e confiável dos sistemas mecânicos em que são utilizados. Para evitar falhas significativas e paradas inesperadas, é crucial estar atento a sinais que podem indicar que um redutor precisa de manutenção. Neste artigo, exploraremos os principais sinais que, se notados, devem levar a uma inspeção e, possivelmente, a uma ação corretiva.
1. Ruídos Anormais
Um dos primeiros sinais de que um redutor pode estar enfrentando problemas é a presença de ruídos anormais durante a operação. Esses ruídos podem variar de zumbidos a rangidos e podem ser causados por desgastes nas engrenagens, rolamentos danificados ou falta de lubrificação. Se o operador notar um som diferente do habitual, é recomendável interromper a operação e inspecionar o redutor imediatamente. Ignorar esses ruídos pode levar a falhas catastróficas que exigem reparos extensivos.
2. Vibrações Excessivas
As vibrações no redutor devem ser monitoradas regularmente. Um aumento repentino nas vibrações pode indicar desalinhamento, desgaste excessivo de peças ou problemas nos rolamentos. O uso de equipamentos de monitoramento pode ajudar a identificar vibrações anormais. Se as vibrações ultrapassarem os níveis aceitáveis, é essencial realizar uma manutenção adequada para evitar danos adicionais ao redutor e a outros componentes conectados ao sistema.
3. Temperatura Elevada
O monitoramento da temperatura operacional é crucial para a saúde dos redutores. Se a temperatura exceder os limites específicos indicados pelo fabricante, isso pode sinalizar problemas como falta de lubrificação, acúmulo de sujeira ou falha em componentes internos. O superaquecimento pode provocar danos permanentes ao redutor se não for tratado prontamente. Por isso, é importante incorporar termômetros industriais e outros dispositivos de monitoramento térmico nos sistemas para uma avaliação contínua.
4. Vazamentos de Lubrificante
Os vazamentos de lubrificantes são um sinal claro de que há algo errado com o redutor. Se forem notados vazamentos de óleo ou graxa, isso pode indicar que as vedações estão danificadas ou que há falhas internas. A ausência de lubrificação adequada pode levar ao desgaste prematuro dos componentes internos, resultando em falhas. É essencial abordar qualquer vazamento imediatamente e substituir as vedações conforme necessário.
5. Aumento no Consumo de Energia
Um aumento no consumo de energia pode ser outro sinal de que o redutor precisa de manutenção. Se o motor que aciona o redutor estiver trabalhando mais do que o habitual para manter a mesma carga, isso pode indicar problemas como atrito excessivo devido a falta de lubrificação ou resistência em componentes desgastados. Essa situação não apenas aumenta os custos operacionais, mas também pode levar a um desgaste adicional do motor, afetando todo o sistema. Portanto, identificar e corrigir a causa do aumento no consumo de energia é crucial.
6. Desgaste Visível
Durante as inspeções regulares, os operadores devem estar atentos a qualquer sinal de desgaste visível nas engrenagens, rolamentos ou carcaça do redutor. A presença de fissuras, desgastes irregulares ou deformações nos componentes do redutor pode ser um indicativo de sobrecarga ou problemas de alinhamento. Se tais sinais forem identificados, uma manutenção mais detalhada e até mesmo a substituição de componentes pode ser necessária para evitar falhas operacionais.
7. Falha Intermitente
Se o redutor apresentar falhas intermitentes, em que a operação fica inconsistente, isso é um sinal preocupante de que algo não está funcionando corretamente. As falhas intermitentes podem ser causadas por diversos fatores, incluindo problemas elétricos, desequilíbrios mecânicos ou falhas nos controles eletrônicos. É fundamental investigar a raiz desse problema o mais rápido possível para evitar interrupções na produção e garantir a segurança da operação.
8. Alinhamento Inadequado
Um alinhamento inadequado entre o redutor e o motor pode levar a problemas sérios a longo prazo, incluindo aumento do desgaste e falhas prematuras. Os operadores devem monitorar regularmente o alinhamento do sistema e fazer os ajustes necessários. Se houver falhas frequentes no alinhamento, pode ser necessário realizar uma revisão mais detalhada do projeto e da instalação do redutor.
Para garantir a saúde geral do redutor, é vital que as equipes de manutenção estejam sempre atentas a esses sinais. A implementação de um regime de monitoramento regular, combinado com uma cultura de manutenção preventiva, pode ajudar a identificar problemas antes que eles se tornem críticos e a maximizar a vida útil do redutor.
Se você deseja saber mais sobre como realizar a manutenção preventiva em redutores, acesse as informações disponíveis e aprenda a prolongar a vida útil dessas importantes máquinas em seu ambiente industrial.
Benefícios da Manutenção Preventiva para Indústrias
A manutenção preventiva é um conjunto de ações programadas que visam manter o desempenho e a integridade dos equipamentos industriais, evitando falhas e prolongando sua vida útil. Quando se trata de máquinas e sistemas críticos, como redutores, a manutenção preventiva é indispensável. Neste artigo, exploraremos os diversos benefícios que essa prática traz para as indústrias.
1. Aumento da Disponibilidade Operacional
Um dos principais benefícios da manutenção preventiva é o aumento da disponibilidade operacional dos equipamentos. Quando as manutenções são realizadas de maneira programada, as falhas inesperadas são reduzidas significativamente. Isso significa que os equipamentos estarão mais disponíveis para operação, resultando em maior eficiência na produção. A capacidade de prever quando os equipamentos precisarão de reparos minimiza o tempo de inatividade e assegura que a linha de produção possa continuar funcionando sem interrupções prolongadas.
2. Redução de Custos com Manutenção Corretiva
A realização de manutenção preventiva ajuda a evitar os altos custos associados à manutenção corretiva. Quando falhas ocorrem, os custos de reparo geralmente são muito mais altos do que o que seria gasto em manutenção programada. Além disso, a manutenção corretiva pode resultar em pausas na produção que não só afetam a eficiência da fábrica, mas também podem impactar as receitas. Assim, investir em manutenção preventiva é, em última análise, uma forma de economizar dinheiro a longo prazo.
3. Prolongamento da Vida Útil dos Equipamentos
Um benefício direto da manutenção preventiva é o prolongamento da vida útil dos equipamentos. Através da verificação regular e da substituição de peças desgastadas, os equipamentos operam dentro das especificações por mais tempo. Essa longevidade é especialmente crítica em indústrias que possuem investimentos substanciais em maquinário, onde a substituição de equipamentos pode ser um gasto significativo. Além disso, equipamentos que são mantidos adequadamente geralmente têm desempenho superior ao longo de sua vida útil.
4. Melhoria da Segurança no Trabalho
A manutenção preventiva não só beneficia a eficiência e a produtividade, mas também melhora a segurança no ambiente de trabalho. Equipamentos mal mantidos podem representar riscos sérios aos funcionários, como falhas que podem levar a acidentes severos. Através de processos regulares de manutenção preventiva, possíveis problemas podem ser identificados e corrigidos antes que se tornem perigosos. Isso cria um ambiente de trabalho mais seguro e protege os funcionários de lesões relacionadas ao uso de equipamentos defeituosos.
5. Melhoria na Qualidade dos Produtos
Um equipamento bem mantido tende a produzir produtos com qualidade superior. Interruptores ou redutores desgastados podem levar a inconsistências na produção, resultando em produtos finais com defeitos. A manutenção preventiva contribui para o controle de qualidade, garantindo que os equipamentos operem conforme os parâmetros estabelecidos. Isso é crucial em indústrias onde a qualidade do produto é diretamente relacionada à satisfação do cliente e à reputação da marca.
6. Aumento da Eficiência Energética
Além de manter o equipamento em boas condições, a manutenção preventiva também otimiza a eficiência energética. Equipamentos que não são mantidos adequadamente frequentemente consomem mais energia devido ao atrito excessivo, componentes desalinhados ou partes faltando. Através de uma manutenção eficaz, as empresas podem reduzir seu consumo de energia, resultando não apenas em economias financeiras, mas também em uma redução do impacto ambiental. Isso está alinhado com as práticas de sustentabilidade que muitas empresas estão buscando cada vez mais.
7. Aumento da Satisfação do Cliente
Como resultado de todos os benefícios mencionados, a manutenção preventiva também pode levar a um aumento na satisfação do cliente. A prestação de serviços ou a produção de produtos de alta qualidade, sem interrupções e de forma eficiente, resulta em clientes satisfeitos que provavelmente voltarão. Quando uma empresa é conhecida por sua confiabilidade, ela se destaca no mercado e se torna uma escolha preferida para os consumidores.
8. Melhoria na previsão de Orçamento
A manutenção preventiva permite que as indústrias planejem seus orçamentos de maneira mais eficaz. Com um cronograma de manutenção bem definido, os custos associados à manutenção podem ser previstos com mais precisão. Isso ajuda as empresas a evitar surpresas financeiras e a se preparar para os gastos regulares com manutenção, tornando a gestão financeira mais eficiente e controlada.
9. Melhoria na Credibilidade da Marca
Empresas que mantêm altos padrões de operação e segurança geralmente desfrutam de uma credibilidade de marca superior. A manutenção preventiva sinaliza para clientes, parceiros e stakeholders que a empresa valoriza a qualidade e a segurança. Isso pode resultar em uma vantagem competitiva em um mercado onde a confiabilidade é uma característica desejável.
Em resumo, a manutenção preventiva é uma prática que apresenta uma gama de benefícios significativos para as indústrias. Desde a redução de custos e o aumento da eficiência até a melhoria da segurança e da qualidade dos produtos, os resultados de um bom regime de manutenção são claros. Pela excelência operacional, as indústrias são capazes de operar de maneira mais eficaz, economizar dinheiro e promover um ambiente de trabalho mais seguro e produtivo.
Erros Comuns na Manutenção de Redutores
A manutenção de redutores é uma atividade essencial para garantir a eficiência e a durabilidade dos equipamentos em ambientes industriais. No entanto, muitos profissionais ainda cometem erros que podem prejudicar a eficácia da manutenção. Identificar e corrigir esses erros é fundamental para assegurar que os redutores operem em condições ideais. Neste artigo, abordaremos alguns dos erros mais comuns na manutenção de redutores e como evitá-los.
1. Negligenciar a Importância da Manutenção Preventiva
Um dos erros mais críticos que muitas indústrias cometem é negligenciar a manutenção preventiva em favor da manutenção corretiva. A manutenção corretiva é reativa, ocorrendo apenas após uma falha ou avaria. Isso pode resultar em altos custos e paradas inesperadas. Investir em um plano de manutenção preventiva pode evitar esses problemas e aumentar a vida útil dos equipamentos. Portanto, é fundamental que as empresas estabeleçam um cronograma regular para as manutenções preventivas e sigam as recomendações do fabricante.
2. Ignorar o Manual do Fabricante
Outro erro comum é ignorar as diretrizes e recomendações presentes no manual do fabricante do redutor. Cada equipamento possui especificações únicas em relação a lubrificação, intervalos de manutenção e inspeções. Não seguir essas recomendações pode resultar em falhas prematuras ou em um desempenho abaixo do esperado. Os profissionais devem sempre consultar o manual e se familiarizar com as práticas e requisitos específicos do redutor em questão.
3. Não Realizar Inspeções Visuais Regulares
Não realizar inspeções visuais regulares é um erro frequentemente encontrado nas práticas de manutenção. As inspeções visuais são essenciais para identificar sinais de desgaste, vazamentos e danos antes que eles se tornem problemas mais sérios. A falta de inspeções pode levar a falhas inesperadas e interrupções na produção. Portanto, é crucial que os operadores incluam inspeções regulares como parte de sua rotina de manutenção.
4. Utilizar Lubrificantes Inadequados
O uso de lubrificantes inadequados ou a falta de lubrificação podem causar danos severos aos redutores. É vital utilizar os tipos e as quantidades de lubrificantes recomendados pelo fabricante. A escolha errada de lubrificante pode resultar em atrito excessivo, aquecimento e desgaste acelerado das componentes. Além disso, a manutenção regular de níveis de lubrificante também é necessária. A falta de atenção a esse aspecto pode comprometer seriamente a operação do redutor.
5. Desconsiderar o Alinhamento
Um erro crítico que pode afetar diretamente o desempenho dos redutores é o desalinhamento entre o redutor e o motor. O desalinhamento leva a um desgaste irregular, aumento da vibração e sobrecarga com o tempo. Sempre que um novo redutor é instalado ou um motor é substituído, deve-se garantir que o alinhamento esteja correto. O alinhamento deve ser verificado e ajustado periodicamente para assegurar que ambos os componentes funcionem de maneira eficiente.
6. Falta de Documentação das Intervenções
A documentação inadequada das atividades de manutenção é um erro que muitas vezes é ignorado. Manter registros detalhados de todas as intervenções realizadas, incluindo inspeções, trocas de componentes, ajustes e lubrificação, é essencial para uma boa gestão da manutenção. Esses registros ajudam as equipes a identificar padrões de falhas e prever necessidades futuras, facilitando a execução de um plano de manutenção mais eficaz.
7. Esperar até que os Sinais de Problemas se Tornem Evidentes
Outro erro comum é esperar até que os sinais de problemas se tornem evidentes para tomar alguma medida. Os operadores muitas vezes ignoram ruídos anormais, vibrações excessivas ou aumento da temperatura até que se tornem problemas sérios. É importante estar atento a qualquer mudança no funcionamento do redutor e agir antes que as pequenas anomalias se transformem em falhas críticas.
8. Não Investir em Treinamento para a Equipe
A falta de treinamento adequado para a equipe responsável pela manutenção dos redutores é um erro que não pode ser subestimado. Um pessoal bem treinado é fundamental para a execução de uma manutenção eficaz. Investir na capacitação da equipe em relação às boas práticas de manutenção, à identificação de problemas e à operação correta dos equipamentos é um passo crucial para evitar erros durante o processo de manutenção.
9. Ignorar a Importância da Calibração
A calibração dos equipamentos é outra área frequentemente negligenciada. Uma calibração adequada é necessária para garantir que os instrumentos utilizados para monitorar a operação dos redutores estejam medindo corretamente. Isso inclui a verificação de termômetros e manômetros, que são essenciais para monitorar as condições operacionais. Ignorar a calibração pode levar a interpretações errôneas dos dados, resultando em manutenções desnecessárias ou, inversamente, em a não realização de manutenções que seriam essenciais.
Evitar esses erros comuns na manutenção de redutores pode fazer toda a diferença na eficiência operacional de uma indústria. Implementar um plano de manutenção preventiva, seguir as diretrizes do fabricante, realizar inspeções regulares e manter a documentação em dia são práticas que garantem a saúde dos equipamentos. Além disso, investir na capacitação da equipe e assegurar a calibração adequada dos instrumentos são componentes-chave para o sucesso da manutenção. Praticando essas medidas, as indústrias podem aumentar a eficiência, prolongar a vida útil dos seus equipamentos e garantir um ambiente de trabalho seguro e produtivo.
Ferramentas Necessárias para a Manutenção Preventiva
A manutenção preventiva é uma parte vital da operação de máquinas e equipamentos em um ambiente industrial, incluindo redutores. Para garantir que essa prática seja realizada de maneira eficaz, é fundamental dispor das ferramentas adequadas. Neste artigo, abordaremos as principais ferramentas necessárias para a manutenção preventiva de redutores, dividindo-as em categorias para facilitar a compreensão e organização.
1. Ferramentas Básicas de Mão
As ferramentas básicas de mão são essenciais para a manutenção diária e incluem chaves, alicates, e chaves de fenda. Essas ferramentas são utilizadas para realizar ajustes e aperto em porcas e parafusos de redutores. A qualidade dessas ferramentas é vital, pois um equipamento de baixa qualidade pode causar danos aos componentes ao aplicar força inadequada.
As chaves de ajuste como a chave inglesa são indispensáveis, assim como as chaves de boca e de catraca, que se adaptam a diferentes tamanhos de parafusos e porcas. Para verificar folgas ou desgastes, um calibre de folga deve ser uma parte do kit básico de ferramentas. Ele permite que os técnicos verifiquem se os componentes estão dentro das especificações antes de realizar a manutenção.
2. Ferramentas de Medição
As ferramentas de medição são indispensáveis para garantir que as operações de manutenção sejam realizadas dentro das especificações recomendadas. Entre as ferramentas de medição, destacam-se os manômetros, termômetros e medidores de vibração. Essas ferramentas são essenciais para monitorar as condições de operação dos redutores, como pressão, temperatura e níveis de vibração.
Por exemplo, manômetros são utilizados para medir a pressão do lubrificante dentro do redutor, enquanto termômetros ajudam a monitorar a temperatura de operação. O uso de um medidor de vibração pode alertar sobre anomalias operacionais que podem levar a falhas se não forem tratadas a tempo. A calibração regular desses instrumentos também é importante, garantindo que eles forneçam leituras precisas.
Para uma verificação mais minuciosa, um osciloscópio pode ser empregado para analisar as ondas de vibração de forma mais detalhada, permitindo identificar problemas específicos de alinhamento ou desequilíbrio.
3. Ferramentas de Lubrificação
A lubrificação é uma parte crucial da manutenção preventiva de redutores. Ferramentas como bombas de lubrificante, aplicadores automáticos e pistolas de graxa são essenciais para a aplicação do lubrificante adequado. A utilização correta dessas ferramentas garante que o lubrificante seja aplicado nas quantidades e locais apropriados, evitando tanto a falta quanto o excesso de lubrificação. O controle dos intervalos de lubrificação deve seguir as recomendações do fabricante e ser parte do plano de manutenção.
Além disso, as sondas de lubrificação podem ser usadas para medir a viscosidade do lubrificante, ajudando a garantir que ele mantenha as propriedades desejadas durante seu ciclo de vida. O uso de lubrificantes de alta qualidade e adequados ao tipo de redutor pode contribuir para a redução do desgaste e para a eficiência energética do sistema.
4. Equipamentos de Proteção Individual (EPIs)
Embora não sejam ferramentas no sentido tradicional, os Equipamentos de Proteção Individual (EPIs) são fundamentais para a segurança de quem realiza a manutenção. O uso de luvas, óculos de proteção, protetores auditivos e capacetes deve ser sempre uma prioridade ao trabalhar com máquinas e ferramentas. Isso não só proporciona segurança ao trabalhador como também reduz o risco de acidentes que podem levar a paradas inesperadas na produção.
5. Ferramentas Específicas para Desmontagem e Montagem
Durante a manutenção preventiva, pode ser necessário desmontar e montar componentes do redutor. Para essa finalidade, ferramentas específicas, como extratores de rolamentos e chaves de fenda de várias formas, são indispensáveis. Essas ferramentas facilitam a retirada de componentes sem danificá-los, permitindo um acesso mais fácil para inspeções e manutenções.
Além disso, se o redutor utilizar engrenagens com montagens de interferência, dispor de ferramentas como aquecedores de indução pode simplificar o processo de desmontagem e montagem dos componentes. Isso evita danos que podem ocorrer devido ao uso de força excessiva durante a retirada de peças apertadas.
6. Materiais de Limpeza e Desengordurantes
A manutenção preventiva também deve incluir a limpeza. A sujeira e os contaminantes podem comprometer o desempenho dos redutores, dificultando a lubrificação e aumentando o desgaste. Por isso, é essencial utilizar materiais de limpeza adequados como desengordurantes e panos de microfibra para a limpeza de superfícies e componentes. Os produtos devem ser escolhidos com cuidado para evitar a degradação de qualquer parte do equipamento.
O uso de uma estrutura de armazenamento adequada e materiais para conter respingos durante as operações de limpeza é igualmente importante, pois evita contaminações que podem resultar em falhas no funcionamento do redutor.
7. Software de Gestão de Manutenção
Para otimizar todo o processo de manutenção, muitas indústrias estão adotando software de gestão de manutenção computadorizada (CMMS). Esses sistemas permitem registrar e monitorar as atividades de manutenção, gerenciar inventários de ferramentas e insumos, e acompanhar os detalhes da manutenção preventiva em tempo real. Uma gestão mais eficiente através de tecnologia pode ajudar equipes a ser mais organizadas e proativas na abordagem da manutenção.
Em resumo, dispor das ferramentas certas é fundamental para uma manutenção preventiva eficaz nos redutores. Desde ferramentas básicas de mão e instrumentos de medição até sistemas de gestão e equipamentos de proteção, cada elemento desempenha um papel importante na garantia do sucesso da manutenção. Investir em ferramentas adequadas resulta em uma operação mais segura e eficiente, reduzindo falhas e aumentando a vida útil dos equipamentos e, consequentemente, a rentabilidade da indústria.
Em conclusão, a manutenção preventiva de redutores é um aspecto imprescindível para o sucesso e a eficiência nas operações industriais. Através da identificação dos tipos de redutores, as ferramentas necessárias e os sinais que indicam a necessidade de intervenção, as empresas podem implementar estratégias que garantam a longevidade e o desempenho otimizado de seus equipamentos. Os benefícios dessa prática, como a redução de custos, o aumento da disponibilidade operacional e a melhoria da segurança, demonstram que investir em manutenção preventiva é uma decisão inteligente e necessária. Portanto, ao adotar um regime de manutenção eficaz e seguir as melhores práticas discutidas, você estará não apenas aumentando a produtividade, mas também contribuindo para um ambiente de trabalho mais seguro e confiável. A prevenção é a chave para maximizar os resultados e garantir que seus redutores operem sempre em sua melhor forma.