Calibração de Válvulas de Segurança: Guia Prático
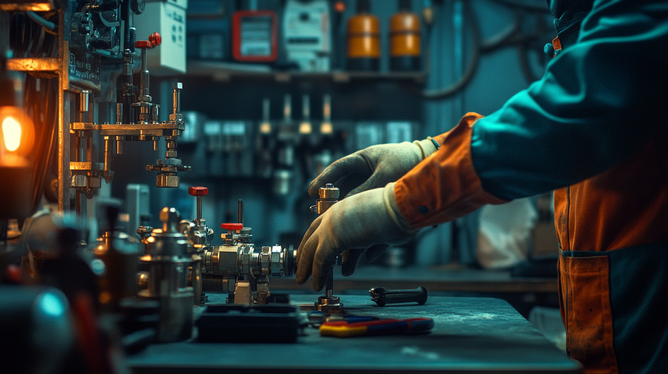
Por: Anderson - 21 de Dezembro de 2024
Calibração de válvulas de segurança é um processo crucial para garantir a operação eficiente e segura de sistemas industriais. Estas válvulas desempenham um papel vital na proteção de equipamentos e na segurança operacional. Neste artigo, abordaremos a importância da calibração, como realizá-la de maneira eficaz, os erros comuns a evitar e a manutenção preventiva necessária para prolongar a vida útil das válvulas. Continue lendo para se aprofundar nesse tema essencial e garantir a segurança da sua operação.
Importância da Calibração de Válvulas de Segurança
A calibração de válvulas de segurança é um aspecto fundamental em ambientes industriais, onde a segurança e a eficiência operacional estão sempre em primeiro plano. Estas válvulas são projetadas para liberar pressão excessiva em sistemas, evitando situações de risco que poderiam levar a acidentes graves, danos a produtos e até mesmo a perda de vidas. Neste contexto, é essencial entender por que a calibração dessas válvulas não deve ser negligenciada.
A calibração garante que as válvulas funcionem dentro dos parâmetros especificados pelo fabricante. Isso significa que, quando a pressão atinge um limite crítico, a válvula abrirá e fechará conforme necessário, protegendo o sistema de falhas. A calibração adequada é um componente essencial para garantir que os processos operacionais não sejam interrompidos por falhas mecânicas.
Segurança como prioridade
A segurança é a principal razão pela qual as válvulas de segurança existem. Elas são projetadas para prevenir explosões e vazamentos que podem acontecer devido ao excesso de pressão em um sistema. Sem a calibração adequada, há um risco significativo de que a válvula não funcione como deveria, o que poderia resultar em consequências desastrosas. Um incidente de pressão pode causar incêndios, explosões e outras catástrofes que poderiam ser evitadas se as válvulas estivessem devidamente calibradas.
Além disso, a calibração regular das válvulas de segurança também ajuda a assegurar a conformidade com regulamentos e normas industriais, que costumam ser rigorosos. O não cumprimento das diretrizes de segurança pode resultar em multas, penalidades legais e até mesmo o fechamento temporário das operações. Portanto, investir na calibração das válvulas não é apenas uma questão de segurança, mas também de conformidade legal.
Eficiência operacional
Outro aspecto importante da calibração de válvulas de segurança é sua contribuição para a eficiência operacional. Quando uma válvula está devidamente calibrada e em boas condições de funcionamento, ela ajuda a manter a pressão do sistema ao nível ideal. Isso não apenas aumenta a eficiência dos processos, mas também minimiza o desgaste do equipamento. O tempo de inatividade causado por falhas pode ser extremamente custoso, tanto em termos financeiros quanto de produtividade.
Uma válvula que não opera corretamente pode causar um aumento da pressão, que pode levar a uma série de problemas no sistema. Isso pode resultar em paradas não programadas, manutenção adicional e custos operacionais mais altos. A calibração, portanto, não é apenas uma necessidade técnica, mas também uma estratégia financeira inteligente.
Prevenção de custos a longo prazo
Ao investir na calibração regular das válvulas de segurança, as empresas podem prevenir custos substanciais a longo prazo. O custo de uma falha catastrófica pode ser muito superior ao investimento em calibrações e manutenções programadas. As válvulas de segurança que não são calibradas adequadamente podem resultar não apenas em perdas de produtos, mas também em danos significativos ao equipamento, aumento de custos de seguros e despesas legais.
As falhas nas válvulas de segurança também podem resultar em ambientes de trabalho perigosos, que podem levar a acidentes. As consequências de um acidente não se restringem apenas aos danos materiais; elas também incluem custos associados a lesões, morte e potenciais ações judiciais. Portanto, a calibração deve ser vista como um investimento na prevenção de custos e na proteção do ambiente de trabalho.
Validade das garantias do fabricante
A maioria dos fabricantes de válvulas de segurança oferece garantias que estão vinculadas a manutenções regulares e calibrações. Se uma empresa não seguir as recomendações do fabricante, pode acabar anulando a garantia. Isso significa que, em caso de falha, a empresa será responsável por todos os custos de reparo ou substituição, o que pode ser extremamente caro.
Portanto, garantir que as válvulas de segurança sejam calibradas regularmente não só aumenta a segurança do processo, mas também protege os interesses financeiros da empresa. A documentação adequada da calibração também pode ser necessária para qualquer inspeção futura e para garantir que as normas de qualidade sejam atendidas.
Melhoria contínua e aprendizado
A calibração de válvulas de segurança também oferece uma oportunidade valiosa para as empresas se envolverem em um processo de melhoria contínua. Ao revisar e ajustar as válvulas regularmente, as equipes têm a chance de identificar problemas e soluções que podem não ter sido evidentes anteriormente. A análise dos padrões de funcionamento das válvulas permite que as empresas aprimorem ainda mais seus sistemas e processos.
Além disso, a calibração regular pode levar a insights sobre o desempenho de outras partes do sistema que poderiam ser melhoradas. A cultura de segurança e eficiência beneficiará todos os aspectos da operação, não só as válvulas de segurança, mas todos os sistemas e equipamentos envolvidos no processo produtivo.
Formação e conscientização dos colaboradores
Calibrações não são apenas um requisito técnico; elas também são uma oportunidade de educação e treinamento para os funcionários envolvidos nas operações. A formação regular sobre como e quando realizar a calibração pode ajudar os trabalhadores a entender melhor a importância de cada componente do sistema em que estão operando.
A conscientização sobre a importância da calibração das válvulas de segurança pode melhorar a cultura de segurança geral dentro de uma organização. Funcionários mais informados e capacitados são mais propensos a seguir os protocolos de segurança e a desempenhar sua função de maneira eficaz, aumentando assim a segurança e a eficiência no local de trabalho.
Considerações Finais
A calibração de válvulas de segurança é um aspecto essencial da operação industrial que não pode ser ignorado. Desde garantir a segurança e conformidade até melhorar a eficiência econômica e operacional, os benefícios são significativos. Portanto, as empresas devem considerar práticas de calibração como uma prioridade, investindo em treinamentos adequados, manutenção regular e sistemas de monitoramento que garantam a operação eficaz das válvulas de segurança.
Em resumo, a calibração de válvulas de segurança é uma misura essencial não apenas para a proteção de sistemas, mas também para a sustentabilidade operacional e o bem-estar dos colaboradores. As empresas que investem nesta prática estão não apenas cumprindo com suas obrigações legais e de segurança, mas também assegurando um futuro mais seguro e eficiente para suas operações.
Como Realizar a Calibração de Válvulas de Segurança
Realizar a calibração de válvulas de segurança é um procedimento essencial para garantir a segurança e a eficiência de sistemas industriais. Uma calibração adequada assegura que as válvulas funcionem de acordo com suas especificações, protegendo o sistema contra excessos de pressão que podem resultar em acidentes. Neste guia, abordaremos as etapas necessárias para eu realizar a calibração de válvulas de segurança de forma correta e eficaz.
Preparação para a Calibração
A preparação é uma etapa crucial antes de iniciar o processo de calibração das válvulas de segurança. Aqui estão algumas diretrizes a serem seguidas:
- Documentação: Antes de tudo, verifique os manuais e especificações técnicas do fabricante. Cada tipo de válvula pode ter requisitos específicos para calibração.
- Ferramentas necessárias: Prepare as ferramentas necessárias, que podem incluir calibradores de pressão, manômetros e equipamentos de proteção individual (EPIs).
- Condições do ambiente: Assegure-se de que a área esteja em condições adequadas, como limpeza e iluminação apropriada, para a realização da calibração.
Desconexão e Inspeção Inicial
Antes de iniciar a calibração, é extremamente importante desconectar a válvula de segurança do sistema. Isso deve ser feito de maneira segura, seguindo os protocolos estabelecidos. Após a desconexão, é recomendável proceder com uma inspeção inicial.
Durante a inspeção, verifique se há sinais visíveis de desgaste, corrosão ou danos na válvula. Componentes danificados devem ser reparados ou substituídos antes de prosseguir com a calibração. A condição da válvula pode impactar diretamente no sucesso do processo de calibração e, portanto, não deve ser subestimada.
Configuração do Equipamento de Calibração
Com a válvula desconectada e a inspeção realizada, o próximo passo é configurar o equipamento de calibração. Isso geralmente envolve:
- Conectar o manômetro: O manômetro deve ser conectado à entrada da válvula de segurança para medir a pressão de abertura. Certifique-se de que a conexão esteja firme e segura.
- Ajustar o equipamento: Configure o equipamento de calibração de acordo com as especificações do fabricante da válvula. Isso pode incluir a seleção de unidades de pressão adequadas e a qualidade do sinal.
Processo de Calibração
Após a configuração do equipamento, você está pronto para iniciar o processo de calibração. Aqui estão os passos principais:
1. Aplicação de PressãoGradualmente, comece a aplicar pressão à válvula utilizando uma fonte de pressão calibrada. Observe atentamente o manômetro à medida que a pressão aumenta. É importante que a pressão seja aumentada de maneira controlada e segura para evitar danos à válvula.
2. Verificação da Pressão de AberturaEnquanto a pressão é aplicada, monitore o manômetro para identificar o ponto exato em que a válvula se abre. Este ponto é conhecido como pressão de abertura. A válvula deve abrir no valor de pressão especificado pelo fabricante.
Se a válvula abrir antes ou depois do valor esperado, ajustes devem ser feitos. A maioria das válvulas de segurança possui um mecanismo de ajuste que permite calibrar a pressão de ativação. Siga as instruções do fabricante para realizar esses ajustes de maneira adequada.
3. Testa a Pressão de FechamentoApós a calibração da pressão de abertura, é importante também verificar a pressão de fechamento da válvula. Para isso, você deve diminuir lentamente a pressão aplicada e observar o ponto em que a válvula fecha novamente.
A pressão de fechamento deve ser igual ou superior ao valor especificado pelo fabricante. Caso contrário, novos ajustes deverão ser realizados.
Documentação da Calibração
Uma vez que a calibração tenha sido realizada, é fundamental documentar todos os resultados. Esta documentação deve incluir:
- Pressão de abertura testada
- Pressão de fechamento testada
- Condições e configurações do equipamento de calibração utilizado
- Ajustes realizados
- Data da calibração e nome do responsável pela realização do processo
A documentação não só serve como um registro valioso, mas também pode ser necessária para auditorias e inspeções futuras. Além disso, um histórico de calibração bem documentado é crucial para manter a conformidade com regulamentos.
Reinstalação da Válvula e Verificações Finais
Após a conclusão da calibração e da documentação, a válvula de segurança pode ser reinstalada no sistema. A instalação deve ser feita de acordo com as orientações do fabricante. Após a instalação, é importante realizar verificações finais.
Verifique todas as conexões de tubulação e orifícios por possíveis vazamentos. Uma válvula com vazamentos pode comprometer o funcionamento do sistema e deve ser corrigida imediatamente.
Rotina de Manutenção e Calibrações Futuras
Para garantir que a válvula de segurança continue funcionando corretamente, é essencial estabelecer uma rotina de manutenção que inclua calibrações regulares. A periodicidade das calibrações pode variar de acordo com as orientações do fabricante, as condições de operação e a criticidade do sistema.
Recomenda-se que as empresas definam um cronograma de manutenção preventiva que inclua inspeções e calibrações em intervalos regulares. Além disso, manter registros de todas as calibrações e manutenções realizadas facilitará o acompanhamento e a análise de desempenho ao longo do tempo.
Considerações Finais
A calibração de válvulas de segurança é um procedimento indispensável para garantir a segurança e eficiente operação em ambientes industriais. Seguir as etapas adequadas, desde a preparação até a documentação, não apenas assegura que a válvula funcione conforme esperado, mas também protege os operadores e a integridade dos sistemas em uso.
Realizar calibrações regulares e manter um histórico detalhado não é apenas uma questão de conformidade; é um investimento na proteção dos ativos da empresa e na segurança de todos os envolvidos. Portanto, não subestime a importância deste procedimento e priorize sempre a calibração de válvulas de segurança em sua rotina operacional.
Principais Erros na Calibração de Válvulas de Segurança
A calibração de válvulas de segurança é um processo crítico para a segurança e eficiência em ambientes industriais. Embora seja uma prática vital, muitos erros podem ocorrer durante o processo de calibração, comprometendo não apenas o funcionamento da válvula, mas também a segurança dos trabalhadores e a integridade do sistema como um todo. Neste artigo, discutiremos os principais erros cometidos na calibração de válvulas de segurança, assim como suas consequências e como evitá-los.
Falta de Preparação Adequada
A primeira etapa essencial em qualquer processo de calibração é a preparação adequada. Um dos erros mais comuns é simplesmente não se preparar adequadamente antes de iniciar a calibração. Isso pode incluir:
- Não revisar documentação: Ignorar os manuais e especificações do fabricante pode levar a uma falta de compreensão sobre os requisitos da válvula e dos procedimentos de calibração.
- Ferramentas inadequadas: Utilizar ferramentas inadequadas ou mal-calibradas pode resultar em leituras imprecisas, levando a calibrações errôneas.
- Ambiente inseguro: Não garantir que o ambiente onde a calibração será realizada esteja seguro e limpo pode resultar em acidentes durante o processo.
Inspeção Inicial Negligenciada
A inspeção inicial da válvula de segurança deve ser uma prática padrão antes de qualquer calibração. Ignorar essa etapa essencial pode acarretar consequências sérias. Os problemas que podem passar despercebidos incluem:
- Desgaste visível: Caso a válvula apresente sinais de desgaste, como corrosão ou danos na estrutura, isso pode afetar seu desempenho pós-calibração.
- Defeitos internos: Problemas que não são imediatamente visíveis, como superaquecimento interno ou falhas em componentes, podem causar falhas na calibração e na operação posterior.
Calibração em Condições Irregulares
A calibração deve ser realizada quando a válvula estiver em condições normais de operação. No entanto, um erro comum é realizar a calibração em condições irregulares, como temperaturas extremas ou pressões fora do normal. Isso pode levar a:
- Leituras imprecisas: Quando as condições não estão dentro dos parâmetros especificados, as leituras podem não refletir a verdadeira pressão de operação da válvula.
- Danos ao equipamento: Condições inadequadas podem causar estresse adicional na válvula durante a calibração, resultando em danos.
Desconsiderar a Necessidade de Testes de Após Calibração
Um grave erro após a calibração é não realizar testes adequados para verificar se a válvula está funcionando conforme o esperado. Testes são essenciais para identificar erros que podem ter ocorrido durante a calibração. Ignorar esta etapa pode resultar em:
- Falhas não detectadas: Se a válvula não passar por testes adequados, quaisquer falhas podem se manifestar apenas em uma situação crítica, levando a acidentes.
- Perda de tempo e recursos: Sem testes, um problema pode não ser identificado imediatamente, resultando em perdas financeiras e operacionais quando o problema for finalmente descoberto.
Não Documentar o Processo de Calibração
A documentação é uma parte essencial do processo de calibração, mas muitas vezes é negligenciada. Outros erros incluem:
- Falta de registros precisos: Não manter registros adequados das calibrações realizadas e dos resultados obtidos torna difícil o acompanhamento da eficácia das calibrações ao longo do tempo.
- Não registrar ajustes feitos: Se ajustes forem necessários durante o processo, é fundamental documentar esses detalhes. A falta dessa documentação pode levar à repetição de erros em calibrações futuras.
Subestimar a Importância da Manutenção Preventiva
Um erro frequente relacionado à calibração de válvulas de segurança é a falta de um programa de manutenção preventiva. Muitas vezes, as empresas realizam calibrações apenas quando os problemas surgem, em vez de adotar uma abordagem proativa. Isso pode levar a:
- Condições de operação inadequadas: Válvulas que não recebem manutenção regular podem operar fora das especificações, resultando em falhas de calibração.
- Custo elevado de reparos: Problemas que não são detectados durante as calibrações podem resultar em custos maiores de reparação quando finalmente descobertos.
Erros de Comunicação na Equipe de Trabalho
A calibração de válvulas de segurança normalmente envolve vários membros da equipe. A falta de comunicação clara entre os membros pode resultar em diversos erros, incluindo:
- Falta de alinhamento nos procedimentos: Quando não há clareza em relação aos procedimentos de calibração, diferentes membros da equipe podem seguir abordagens diferentes, levando a erros.
- Instruções não seguidas: Como resultado de erros de comunicação, pode haver uma maior probabilidade de que as instruções de calibração não sejam seguidas corretamente, resultando em falhas.
Uso Incorreto de Equipamentos de Calibração
O uso incorreto de equipamentos de calibração pode ter consequências sérias. Entre os erros comuns estão:
- Calibradores não calibrados: Utilizar equipamentos que não foram calibrados corretamente pode resultar em medições imprecisas, impactando diretamente a calibração da válvula.
- Configuração inadequada do equipamento: Não configurar os dispositivos de calibração de acordo com as especificações corretas pode comprometer a precisão das medições realizadas.
Não Treinar Adequadamente os Colaboradores
Um erro muitas vezes subestimado é a pressão inadequada que se aplica ao treinamento dos colaboradores envolvidos na calibração. Colaboradores não treinados podem cometer erros ao longo do processo. As consequências incluem:
- Execução incorreta da calibração: Funcionários que não entendem os procedimentos adequados podem falhar em garantir que a calibração seja realizada corretamente.
- Aumento da probabilidade de riscos: A falta de treinamento na operação e calibração de válvulas de segurança pode aumentar os riscos de acidentes no ambiente de trabalho.
Considerações Finais
Evitar os erros comuns durante a calibração de válvulas de segurança é vital para a manutenção da segurança e eficiência no ambiente industrial. Cuidar da preparação, realização de inspeções, documentação e treinamento adequado são práticas que devem ser priorizadas. Realizar calibrações corretas não apenas assegura a proteção contra vazamentos e explosões, mas também garante a integridade operacional de todo o sistema.
Compreender e reconhecer as principais falhas que podem ocorrer durante a calibração permitirá que as organizações adotem práticas mais seguras e eficazes, melhorando a performance e a segurança em suas operações. Portanto, é crucial um compromisso contínuo com essas práticas e uma cultura de conscientização sobre a importância da calibração de válvulas de segurança.
Manutenção Preventiva de Válvulas de Segurança
A manutenção preventiva de válvulas de segurança é uma prática crítica que garante a eficácia e a segurança em sistemas industriais. As válvulas de segurança desempenham um papel vital na proteção contra pressões excessivas em sistemas de tubulação e equipamento. Quando não mantidas corretamente, essas válvulas podem falhar, levando a acidentes, perdas financeiras e danos ao equipamento. Neste artigo, exploraremos a importância da manutenção preventiva, as melhores práticas e um guia sobre como implementar um programa eficaz.
Importância da Manutenção Preventiva
A importância da manutenção preventiva de válvulas de segurança não pode ser subestimada. Algumas das razões principais incluem:
- Segurança do Trabalho: A principal função das válvulas de segurança é proteger os trabalhadores e o ambiente de trabalho. Uma válvula que não está funcionando adequadamente pode resultar em explosões ou vazamentos perigosos.
- Redução de Custos: O custo de realizar a manutenção preventiva é significativamente menor do que lidar com os custos de reparação ou substituição devido a falhas. Além disso, falhas podem resultar em longos períodos de inatividade, que afetam direitamente a produtividade.
- Aumento da Confiabilidade: Manutenção regular ajuda a garantir que as válvulas operem de maneira eficiente e confiável, promovendo um ambiente de trabalho mais estável e consistência nas operações.
- Conformidade com Normas e Regulamentos: Muitas regulamentações exigem a execução regular de manutenções preventivas. Não fazê-lo pode resultar em penalidades legais e comprometer a reputação da empresa.
Conceito de Manutenção Preventiva
A manutenção preventiva é uma abordagem sistemática que visa realizar a manutenção das válvulas em intervalos regulares, independentemente de falhas óbvias ou problemas reportados. Essa abordagem inclui, mas não se limita a:
- Inspeções Regulares: Verificar o estado das válvulas e dos componentes relacionados em intervalos determinados para identificar possíveis sinais de desgaste.
- Calibragem: Realizar a calibração periódica das válvulas para garantir que estão abrindo e fechando nas pressões apropriadas.
- Limpeza: Manter as válvulas limpas e livres de substâncias que possam comprometer seu funcionamento.
- Substituição de Componentes: Trocar peças desgastadas ou danificadas antes que causem falhas.
Melhores Práticas para Manutenção Preventiva
Implementar um programa de manutenção preventiva eficaz de válvulas de segurança exige planejamento e consistência. Aqui estão algumas melhores práticas que devem ser seguidas:
1. Estabelecer um Cronograma de ManutençãoUm cronograma de manutenção deve ser desenvolvido com base nas recomendações do fabricante, no histórico de falhas, e nas condições operacionais. É importante documentar:
- Datas programadas para calibrações e inspeções.
- Resultados de inspeções anteriores e ajustes realizados.
- Responsáveis pelas atividades de manutenção.
Todos os membros da equipe envolvidos na operação e manutenção das válvulas de segurança devem receber treinamento contínuo para garantir que estejam atualizados sobre os procedimentos e melhores práticas. O treinamento deve incluir:
- As especificações dos equipamentos e válvulas utilizados.
- Procedimentos de calibração e inspeção.
- Segurança e manipulação adequada dos equipamentos.
A documentação efetiva é vital para o sucesso da manutenção preventiva. Isso inclui:
- Registros de todas as inspeções realizadas.
- Detalhes sobre quaisquer ajustes ou reparos executados.
- Resultados de calibrações e medições.
Esses registros ajudam a identificar padrões ao longo do tempo, permitindo que as empresas ajustem suas práticas de manutenção conforme necessário.
4. Inspeção Visual e AuditivaRealizar inspeções visuais e auditivas regulares é uma maneira eficaz de identificar problemas emergentes antes que eles se tornem mais sérios. Os técnicos devem estar atentos aos seguintes sinais:
- Ruidos incomuns que podem indicar falhas mecânicas.
- Sinais de vazamento ao redor das válvulas e conexões.
- Danos visíveis, como corrosão ou deterioração.
Passo a Passo para Implementar um Programa de Manutenção Preventiva
Implementar um programa de manutenção preventiva para válvulas de segurança implica seguir várias etapas fundamentais:
1. Avaliação do Sistema AtualAntes de implementar um novo programa de manutenção, é importante avaliar o sistema atual de gerenciamento de manutenção. Isso pode incluir:
- Revisão de registros de manutenção e calibrações anteriores.
- Análise de falhas anteriores e suas causas.
- Identificação de áreas que necessitam de melhorias.
Crie protocolos que definam como a manutenção será realizada. Isso deve incluir:
- Frequentemente deve a calibração e as inspeções serem realizadas.
- Instruções detalhadas para inspeções e limpezas.
- Características que devem ser verificadas durante as inspeções.
Os recursos necessários devem ser alocados adequadamente para garantir o sucesso do programa. Isso inclui:
- Equipamentos de medição e calibração adequados.
- Pessoal treinado para realizar a manutenção.
- Suprimentos e peças sobressalentes para reparos necessários.
Com o programa definido, comece a implementação. É essencial monitorar o progresso e a eficácia do programa. Isso pode incluir:
- Revisões regulares dos registros de manutenção.
- Realização de reuniões periódicas de revisão de desempenho.
- Ajustes ao programa com base nas observações e feedback dos operadores.
Desafios comuns na Manutenção Preventiva
Embora a manutenção preventiva seja uma prática recomendada, ela não está isenta de desafios. Alguns dos desafios comuns incluem:
- Resistência à Mudança: Funcionários podem ter dificuldade em adotar novos procedimentos ou protocolos. A comunicação e o treinamento eficazes são essenciais para superá-los.
- Custo Inicial: A implementação inicial de um programa de manutenção pode envolver custos, mas é importante lembrar que esses investimentos podem economizar dinheiro a longo prazo.
- Falta de Dados: Sem históricos completos de manutenção ou dados confiáveis, pode ser difícil planejar manutenção até que problemas surjam.
Conclusão
A manutenção preventiva de válvulas de segurança é uma prática essencial que não deve ser negligenciada. Com o advento de tecnologias modernas e procedimentos aprimorados, a manutenção pode garantir não apenas a segurança dos colaboradores, mas também a eficiência operacional das empresas. Implementar um programa estruturado e coordenado de manutenção preventiva irá resultar em um ciclo operacional mais forte, redução de custos e segurança no ambiente de trabalho. Assim, ao seguir as melhores práticas e estar ciente dos principais desafios, as empresas poderão operar com confiança, assegurando a eficácia de suas válvulas de segurança.
Em resumo, a calibração de válvulas de segurança é um procedimento indispensável que não pode ser subestimado. Através de uma colaboração eficaz entre as práticas de calibração e a manutenção preventiva, é possível assegurar não apenas a proteção dos trabalhadores e a integridade dos equipamentos, mas também a conformidade com as normas regulatórias. Como vimos, a preparação adequada, a documentação meticulosa e a capacitação contínua da equipe são componentes fundamentais para a eficácia desse processo. Evitar erros comuns e seguir as melhores práticas estabelecidas garantirá que suas válvulas operem conforme esperado, contribuindo para um ambiente de trabalho seguro e eficiente. Portanto, invista na calibração e manutenção de suas válvulas de segurança, e colha os benefícios de operações otimizadas e seguras em sua estrutura industrial.