Calibração de Equipamentos Laboratoriais: Passos Essenciais
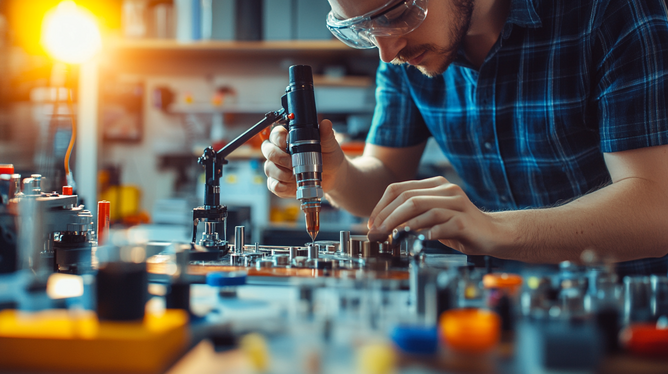
Por: Anderson - 15 de Novembro de 2024
Calibração de equipamentos laboratoriais é um processo essencial para garantir a precisão e a confiabilidade dos resultados obtidos em análises. Neste artigo, você aprenderá sobre a importância da calibração, os métodos mais utilizados e a frequência recomendada para realizar esse procedimento. Continue lendo para entender como a calibração pode impactar a qualidade do seu trabalho no laboratório.
1. Importância da Calibração de Equipamentos Laboratoriais
A calibração de equipamentos laboratoriais é uma prática fundamental que assegura a precisão dos resultados obtidos em diversos experimentos e análises. Quando falamos de laboratórios, seja na área de química, biologia, física ou engenharia, a confiabilidade dos dados gerados é crucial para a tomada de decisões e para a validade das pesquisas. Neste contexto, a calibração se torna um procedimento indispensável, pois garante que os instrumentos estejam funcionando corretamente e produzindo resultados que podem ser considerados válidos.
Um dos principais motivos pelos quais a calibração é tão importante é que ela ajuda a identificar e corrigir erros que podem ocorrer nos instrumentos ao longo do tempo. Os equipamentos laboratoriais, como balanças, espectrofotômetros e pHmetros, podem sofrer desgastes, influências ambientais e variações de temperatura, o que pode afetar diretamente a precisão das medições. A calibração regular permite que esses problemas sejam detectados e corrigidos, assegurando que os resultados obtidos sejam sempre confiáveis.
Além disso, a calibração é um requisito essencial para a conformidade com normas e regulamentos. Muitos laboratórios operam sob certificações que exigem a calibração periódica dos equipamentos. Isso é especialmente relevante em setores como farmacêutico, alimentício e de saúde, onde a precisão dos dados pode impactar diretamente na segurança e eficácia de produtos e processos. A falta de calibração pode resultar em não conformidades, que podem levar a sanções legais, perda de certificações e até mesmo riscos à saúde pública.
Outro ponto a ser considerado é a importância da calibração na melhoria da qualidade dos processos laboratoriais. Quando os instrumentos estão devidamente calibrados, a variabilidade nos resultados é reduzida, permitindo uma maior reprodutibilidade e consistência nas análises. Isso é particularmente relevante em pesquisas científicas, onde a capacidade de reproduzir resultados é um dos pilares da metodologia científica. Um experimento que gera dados inconsistentes devido a equipamentos não calibrados pode comprometer toda a pesquisa e levar a conclusões erradas.
A calibração também desempenha um papel crucial na otimização de recursos e na redução de custos. Quando os equipamentos estão calibrados, a probabilidade de erros e retrabalhos diminui, resultando em uma utilização mais eficiente dos insumos e do tempo dos profissionais envolvidos. Isso significa que, ao investir em calibração, os laboratórios podem economizar dinheiro a longo prazo, evitando desperdícios e melhorando a produtividade.
Adicionalmente, a calibração de equipamentos laboratoriais contribui para a segurança dos colaboradores. Equipamentos que não estão funcionando corretamente podem representar riscos, especialmente em laboratórios que lidam com substâncias químicas perigosas ou processos sensíveis. Ao garantir que os instrumentos estejam calibrados, os laboratórios podem minimizar esses riscos e proporcionar um ambiente de trabalho mais seguro para todos os envolvidos.
Por fim, é importante destacar que a calibração não é um processo único, mas sim um ciclo contínuo. Os equipamentos devem ser calibrados regularmente, de acordo com as recomendações dos fabricantes e as necessidades específicas de cada laboratório. Isso inclui a realização de manutenções preventivas, como a manutenção de redutor, que ajuda a garantir que os instrumentos operem com precisão e eficiência ao longo do tempo.
Em resumo, a calibração de equipamentos laboratoriais é um aspecto vital para a operação eficaz de qualquer laboratório. Ela assegura a precisão dos resultados, garante a conformidade com normas e regulamentos, melhora a qualidade dos processos, otimiza recursos e promove a segurança dos colaboradores. Portanto, investir em calibração é investir na qualidade e na confiabilidade dos dados gerados, o que, por sua vez, impacta diretamente na credibilidade e no sucesso das atividades laboratoriais.
2. Principais Métodos de Calibração
A calibração é um processo essencial para garantir a precisão e a confiabilidade dos equipamentos laboratoriais. Existem diversos métodos de calibração que podem ser utilizados, dependendo do tipo de equipamento, da aplicação e das normas específicas a serem seguidas. Neste artigo, abordaremos os principais métodos de calibração, suas características e quando cada um deles deve ser aplicado.
Um dos métodos mais comuns de calibração é a calibração por comparação. Este método envolve a comparação dos resultados obtidos por um equipamento em relação a um padrão de referência conhecido. O padrão de referência deve ser um instrumento de alta precisão que já tenha sido calibrado e que atenda a normas reconhecidas. Durante o processo, as medições do equipamento em teste são realizadas sob as mesmas condições em que o padrão foi calibrado, permitindo identificar desvios e realizar ajustes necessários. Este método é amplamente utilizado para equipamentos de medição, como balanças e termômetros.
Outro método importante é a calibração por ajuste. Este método é utilizado quando um equipamento apresenta um desvio significativo em relação ao padrão de referência. Após a comparação, o técnico responsável realiza ajustes diretamente no equipamento para corrigir as medições. Essa abordagem é comum em instrumentos como espectrofotômetros e pHmetros, onde é crucial que os resultados estejam dentro de faixas aceitáveis. A calibração por ajuste pode ser feita em campo ou em laboratório, dependendo da complexidade do equipamento e das condições de operação.
A calibração em ponto único é um método que envolve a verificação da precisão de um equipamento em um único ponto de medição. Esse método é frequentemente utilizado em equipamentos que operam em condições de temperatura ou pressão específicas. Por exemplo, a calibração de um termômetro pode ser realizada em um ponto de referência, como a temperatura de fusão do gelo, para garantir que o instrumento esteja medindo corretamente naquela condição específica. Embora seja um método simples e rápido, a calibração em ponto único pode não ser suficiente para instrumentos que operam em uma ampla faixa de medições, sendo mais adequado para equipamentos com aplicações limitadas.
A calibração em múltiplos pontos, por sua vez, é uma abordagem mais abrangente, onde o equipamento é testado em vários pontos de medição ao longo de sua faixa de operação. Esse método fornece uma visão mais completa da precisão do instrumento e é especialmente útil para equipamentos que precisam operar em diferentes condições. Por exemplo, um pHmetro pode ser calibrado em vários valores de pH, garantindo que o instrumento funcione adequadamente em toda a sua faixa de medição. Este método é considerado o mais eficaz para garantir a precisão em uma ampla gama de aplicações.
Além dos métodos mencionados, a calibração também pode ser realizada por meio de simulação. Este método é utilizado para equipamentos que não podem ser calibrados diretamente, como alguns tipos de sensores e dispositivos de medição. A simulação envolve a criação de condições controladas que imitam as situações reais em que o equipamento será utilizado. Por exemplo, um sensor de pressão pode ser calibrado em um ambiente de laboratório que reproduza as condições de pressão e temperatura do local de operação. A simulação é uma técnica valiosa, pois permite a calibração de equipamentos que, de outra forma, seriam difíceis de testar.
Outro aspecto importante a considerar na calibração é a manutenção em redutores, que pode impactar a precisão dos equipamentos. Redutores são componentes críticos em muitos sistemas de medição e controle, e sua manutenção adequada é fundamental para garantir que os instrumentos funcionem corretamente. A calibração deve ser realizada após qualquer manutenção significativa para assegurar que o equipamento esteja operando dentro das especificações desejadas.
Por fim, é importante ressaltar que, independentemente do método de calibração escolhido, a documentação adequada do processo é essencial. Registros de calibração devem incluir informações sobre os padrões utilizados, os resultados das medições, os ajustes realizados e as condições sob as quais a calibração foi feita. Essa documentação é necessária para garantir a rastreabilidade e a conformidade com normas e regulamentos aplicáveis.
Em resumo, a escolha do método de calibração adequado depende de vários fatores, incluindo o tipo de equipamento, a aplicação e as normas a serem seguidas. A calibração por comparação, ajuste, em ponto único, em múltiplos pontos e simulação são algumas das abordagens mais comuns. A manutenção regular, como a manutenção em redutores, também desempenha um papel crucial na precisão dos equipamentos. Com um plano de calibração bem estruturado, os laboratórios podem garantir a confiabilidade e a qualidade dos resultados obtidos.
3. Frequência Recomendada para Calibração
A calibração de equipamentos laboratoriais é um processo contínuo e essencial para garantir a precisão e a confiabilidade dos resultados obtidos. No entanto, um aspecto muitas vezes negligenciado é a frequência com que esses equipamentos devem ser calibrados. A determinação da frequência de calibração adequada depende de diversos fatores, incluindo o tipo de equipamento, a aplicação, as condições de uso e as normas regulatórias aplicáveis. Neste artigo, vamos explorar as diretrizes gerais sobre a frequência recomendada para calibração e como estabelecer um cronograma eficaz.
Primeiramente, é importante entender que cada tipo de equipamento possui características específicas que influenciam a necessidade de calibração. Equipamentos que são utilizados em ambientes críticos, onde a precisão é fundamental, geralmente requerem calibrações mais frequentes. Por exemplo, instrumentos de medição que operam em laboratórios de pesquisa ou em indústrias de alta tecnologia, como farmacêutica e alimentícia, podem necessitar de calibrações mensais ou trimestrais. A calibração de manômetro, por exemplo, deve ser realizada com frequência para garantir que as medições de pressão estejam sempre dentro dos limites especificados.
Por outro lado, equipamentos que operam em condições menos críticas podem ter uma frequência de calibração mais espaçada. Em muitos casos, a calibração semestral ou anual pode ser suficiente para garantir a precisão das medições. É fundamental, no entanto, que essa decisão seja baseada em uma avaliação do risco associado ao uso do equipamento e ao impacto que medições imprecisas podem ter nos resultados e na segurança. Um laboratório que lida com substâncias perigosas ou processos sensíveis deve considerar uma calibração mais frequente, enquanto um laboratório que realiza medições menos críticas pode optar por intervalos mais longos.
Outro fator a ser considerado na determinação da frequência de calibração é a intensidade de uso do equipamento. Equipamentos que são utilizados com frequência ou que passam por ciclos de operação intensos tendem a apresentar desgastes mais rápidos, o que pode afetar sua precisão. Portanto, é recomendável que esses equipamentos sejam calibrados com mais frequência. Por exemplo, uma balança utilizada diariamente em um laboratório de controle de qualidade pode precisar de calibração mensal, enquanto uma balança que é usada apenas ocasionalmente pode ser calibrada anualmente.
As condições ambientais também desempenham um papel crucial na frequência de calibração. Equipamentos que operam em ambientes com variações significativas de temperatura, umidade ou vibração podem exigir calibrações mais frequentes. Essas condições podem afetar o desempenho dos instrumentos e, consequentemente, a precisão das medições. Portanto, é importante que os laboratórios avaliem as condições ambientais em que seus equipamentos estão operando e ajustem a frequência de calibração conforme necessário.
Além disso, a calibração deve ser realizada sempre que um equipamento é submetido a manutenção ou reparos. Após qualquer intervenção significativa, é crucial recalibrar o equipamento para garantir que ele esteja funcionando corretamente. Isso é especialmente importante em equipamentos que possuem componentes móveis ou que são afetados por ajustes mecânicos. A calibração deve ser parte integrante do processo de manutenção, assegurando que os instrumentos estejam sempre prontos para fornecer resultados confiáveis.
As normas e regulamentações também influenciam a frequência de calibração. Muitos setores, como o farmacêutico, alimentício e de saúde, possuem diretrizes específicas que determinam a frequência com que os equipamentos devem ser calibrados. É essencial que os laboratórios estejam cientes dessas regulamentações e as sigam rigorosamente para garantir a conformidade e a segurança. Além disso, a documentação adequada das calibrações realizadas é fundamental para demonstrar a conformidade com as normas e para manter a rastreabilidade dos resultados.
Por fim, é importante ressaltar que a calibração não deve ser vista apenas como um requisito regulatório, mas como uma prática essencial para a qualidade e a confiabilidade dos resultados laboratoriais. Estabelecer uma frequência de calibração adequada é uma parte crucial do gerenciamento da qualidade em qualquer laboratório. Ao garantir que os equipamentos estejam sempre calibrados e funcionando corretamente, os laboratórios podem minimizar erros, aumentar a eficiência e garantir a segurança em suas operações.
Em resumo, a frequência recomendada para calibração de equipamentos laboratoriais varia de acordo com o tipo de equipamento, as condições de uso, a intensidade de operação e as diretrizes regulatórias. Equipamentos críticos podem exigir calibrações mensais ou trimestrais, enquanto equipamentos menos críticos podem ser calibrados anualmente. Avaliar cuidadosamente todos esses fatores permitirá que os laboratórios estabeleçam um cronograma de calibração eficaz, garantindo a precisão e a confiabilidade dos resultados obtidos.
4. Erros Comuns na Calibração de Equipamentos
A calibração de equipamentos é um processo crítico para garantir a precisão e a confiabilidade das medições em laboratórios e indústrias. No entanto, existem diversos erros que podem ocorrer durante esse processo, comprometendo a qualidade dos resultados obtidos. Neste artigo, abordaremos os erros mais comuns na calibração de equipamentos e como evitá-los, garantindo que os instrumentos estejam sempre em conformidade com as normas e especificações.
Um dos erros mais frequentes na calibração é a falta de um padrão de referência apropriado. A calibração deve sempre ser realizada em comparação com um padrão conhecido e rastreável, que tenha sido calibrado por um laboratório acreditado. Utilizar um padrão inadequado ou não rastreável pode levar a medições imprecisas e a uma falsa sensação de segurança em relação à precisão do equipamento. Portanto, é essencial que os técnicos responsáveis pela calibração verifiquem a validade e a rastreabilidade dos padrões utilizados.
Outro erro comum é a calibração realizada em condições inadequadas. A temperatura, umidade e vibração do ambiente podem influenciar significativamente os resultados da calibração. Por exemplo, calibrar um instrumento em um ambiente com temperaturas extremas ou flutuações rápidas pode resultar em medições imprecisas. Para evitar esse problema, é fundamental que a calibração seja realizada em condições controladas e que os equipamentos estejam estabilizados antes do início do processo.
A falta de formação e treinamento adequados dos profissionais responsáveis pela calibração é outro fator que pode comprometer a precisão dos resultados. Técnicos não treinados podem cometer erros ao utilizar os equipamentos, interpretar os resultados ou realizar os ajustes necessários. Investir em treinamento contínuo e em capacitação para os colaboradores é essencial para garantir que a calibração seja realizada de maneira correta e eficiente. Além disso, a documentação dos procedimentos de calibração deve ser clara e acessível para todos os envolvidos.
Um erro comum na calibração é a falta de manutenção preventiva dos equipamentos. Instrumentos que não são mantidos adequadamente podem apresentar desgastes e falhas, afetando sua precisão. A calibração deve ser realizada após qualquer manutenção significativa, mas também é importante realizar manutenções preventivas regularmente, a fim de minimizar o risco de falhas. Isso inclui a verificação de componentes, ajustes mecânicos e Termômetros industriais que podem fornecer suporte técnico e serviços de manutenção especializados.
Além disso, a falta de documentação adequada durante o processo de calibração pode levar a erros e confusões futuras. Registros incompletos ou incorretos podem dificultar a identificação de problemas e a rastreabilidade dos resultados. É crucial que todos os passos do processo de calibração sejam documentados, incluindo os padrões utilizados, as condições ambientais, os resultados das medições e quaisquer ajustes realizados. Essa documentação não apenas ajuda na conformidade com normas e regulamentos, mas também serve como referência para futuras calibrações.
Outro erro que pode ocorrer é a calibração em um único ponto de medição. Embora a calibração em ponto único possa ser adequada para alguns equipamentos, muitos instrumentos operam em uma faixa ampla de medições. A calibração em múltiplos pontos é mais eficaz para garantir a precisão em toda a faixa de operação do equipamento. Portanto, sempre que possível, deve-se optar pela calibração em múltiplos pontos para obter uma visão mais completa da performance do instrumento.
A negligência em seguir as recomendações do fabricante também é um erro comum. Cada equipamento possui especificações e diretrizes específicas para calibração, incluindo a frequência recomendada e os métodos a serem utilizados. Ignorar essas recomendações pode resultar em medições imprecisas e em não conformidade com normas regulatórias. Portanto, é essencial que os técnicos estejam cientes das diretrizes do fabricante e as sigam rigorosamente.
Por fim, a falta de um cronograma de calibração bem definido pode levar a atrasos e à calibração irregular dos equipamentos. A calibração deve ser parte integrante do plano de gerenciamento da qualidade do laboratório. Estabelecer um cronograma de calibração, que leve em consideração a frequência recomendada, as condições de uso e as normas regulatórias, é fundamental para garantir que todos os equipamentos estejam sempre em conformidade.
Em resumo, a calibração de equipamentos é um processo complexo que pode ser afetado por diversos erros comuns. A falta de um padrão de referência apropriado, condições inadequadas, falta de treinamento, manutenção preventiva, documentação insuficiente, calibração em um único ponto, negligência em seguir recomendações do fabricante e a ausência de um cronograma bem definido são alguns dos principais fatores que podem comprometer a precisão dos resultados. Ao estar ciente desses erros e implementar medidas para evitá-los, os laboratórios podem garantir a confiabilidade e a qualidade dos dados obtidos, contribuindo para o sucesso de suas operações.
Em conclusão, a calibração de equipamentos laboratoriais é um aspecto fundamental para assegurar a integridade e a precisão dos resultados obtidos em qualquer análise. Ao compreender a importância da calibração, os métodos disponíveis e a frequência adequada para sua realização, os profissionais podem garantir que seus instrumentos estejam sempre operando dentro dos padrões exigidos. Além disso, evitar os erros comuns na calibração é crucial para manter a confiabilidade dos dados e a conformidade com as normas regulatórias. Portanto, investir em um processo de calibração bem estruturado não apenas melhora a qualidade do trabalho no laboratório, mas também contribui para a segurança e a eficácia das operações. Ao final, a calibração é uma prática que beneficia não apenas os resultados individuais, mas também a reputação e a credibilidade do laboratório como um todo.