Calibração de Manômetro: Importância e Como Fazer
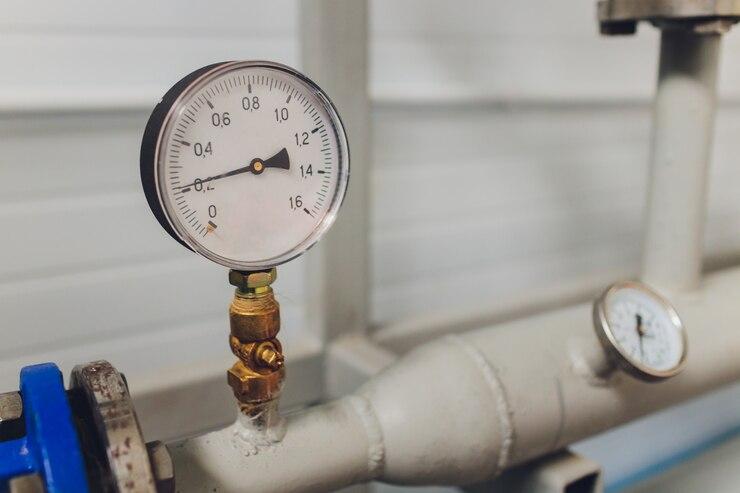
Por: Anderson - 09 de Outubro de 2024
A calibração manômetro é um processo fundamental para assegurar a precisão nas medições de pressão. Neste artigo, você irá entender a importância da calibração regular, como realizá-la de maneira eficaz e quais são os erros mais comuns que podem comprometer a confiabilidade dos manômetros. Prepare-se para aprender e garantir a eficiência dos seus instrumentos de medição!
O que é calibração de manômetro
A calibração de manômetro é um procedimento técnico que garante a precisão das medições de pressão realizadas por um manômetro. Essa prática envolve a comparação das leituras do manômetro em teste com um padrão de referência em condições controladas. A calibragem é essencial em diversas indústrias, desde a petroquímica até a alimentícia, onde a precisão nos dados é crucial para a qualidade e segurança do produto final.
Um manômetro funciona de forma a medir a pressão de um sistema, seja ele um gás ou um líquido, fornecendo leituras em unidades como psi (libras por polegada quadrada) ou bar. Entretanto, ao longo do tempo, diversos fatores, como desgaste mecânico, corrosão, alterações de temperatura e vibrações, podem afetar a precisão das leituras. Por isso, a calibração regular é necessária para assegurar que o manômetro esteja fornecendo dados corretos e confiáveis.
Durante o processo de calibração, o manômetro em questão é submetido a condições conhecidas de pressão, reunindo leituras comparativas. A partir disso, ajustes podem ser feitos para corrigir quaisquer desvios em relação ao padrão. Em algumas situações, o dispositivo deve ser ajustado fisicamente, enquanto em outras é possível realizar a correção através de software.
Importância da calibração de manômetro
A calibração de manômetros não é apenas uma questão de precisão, mas também de segurança e conformidade. Em setores regulados, como o farmacêutico e o alimentício, a normativa estabelece a frequência e os protocolos que devem ser seguidos. A calibração inadequada pode levar a falhas na produção, resultando em produtos fora das especificações, o que pode comprometer a segurança do consumidor.
Processo de calibração
O processo de calibração pode ser dividido em várias etapas:
- Preparação: Antes de iniciar a calibração, é fundamental que o manômetro esteja limpo e em boas condições de funcionamento. A equipe responsável deve inspecionar visualmente e garantir que não haja sujeira ou danos que possam interferir na calibração.
- Seleção do padrão de referência: Um equipamento de calibração de alta precisão deve ser utilizado como padrão. É importante que o padrão esteja calibrado e certificado, garantindo a confiabilidade e a precisão necessárias para a comparação.
- Calibração: Neste estágio, o manômetro a ser testado é exposto a uma série de pressões conhecidas. Isso pode ser feito utilizando um equipamento de calibração que aplica pressão ao manômetro em várias etapas. À medida que diferentes pressões são aplicadas, as leituras do manômetro devem ser registradas.
- Ajuste: Se as leituras do manômetro estiverem fora das especificações, ajustes poderão ser realizados. Isso pode envolver o ajuste mecânico do manômetro ou a introdução de correções compensatórias no sistema.
- Documentação: Após a calibração, todas as leituras, ajustes feitos e os resultados finais devem ser documentados. Esta documentação deve ser conservada como parte do histórico do manômetro, servindo para auditorias futuras e análises de tendência.
Fatores que afetam a calibração
Diversos fatores podem impactar a eficácia da calibração de manômetros. Alguns dos mais comuns incluem:
- Temperatura: As variações de temperatura podem influenciar a pressão dos gases e líquidos, impactando as leituras dos manômetros. Portanto, a calibração deve ser realizada em condições de temperatura controlada sempre que possível.
- Umidade: A umidade excessiva pode causar corrosão nos componentes internos do manômetro, afetando a precisão. Ambientes úmidos podem, portanto, demandar calibrações mais frequentes.
- Vibrações: Manômetros instalados em áreas com altas vibrações podem apresentar desgaste acelerado ou descalibração. O local de instalação deve ser avaliado para minimizar esses impactos.
- Fadiga do material: O uso prolongado pode levar à fadiga de componentes do manômetro, especialmente em ambientes industriais severos. A monitorização constante é necessária para garantir a precisão ao longo do tempo.
Erro de calibração
É importante mencionar que a calibração não é um processo único, mas sim uma prática contínua. Mesmo um manômetro recém-calibrado pode começar a apresentar erros no decorrer do tempo. Erros de calibração podem ser classificados como:
- Erro sistemático: Este tipo de erro ocorre devido a constantes de calibração que não estão dentro dos padrões. Comumente, está associado a falhas no próprio instrumento.
- Erro aleatório: Erros aleatórios podem ocorrer devido a fatores imprevisíveis que afetam a medição. Esses erros são mais difíceis de identificar e corrigir, pois podem variar de uma mediçação para outra.
Benefícios da calibração de manômetro
A calibração regular de manômetros traz uma série de benefícios tanto para a operação como para a segurança:
- Precisão nas medições: Com manômetros devidamente calibrados, as medições serão mais precisas, garantindo a qualidade do produto final.
- Segurança: Em várias indústrias, uma pressão inadequada pode levar a situações perigosas. A calibração ajuda a prevenir esses riscos.
- Conformidade regulatória: Muitas indústrias são obrigadas a seguir normas e regulamentos rigorosos. A calibração garante que você esteja em conformidade com as exigências legais.
- Redução de custos: Manter a precisão nas medições pode evitar desperdícios e custos desnecessários associados a produtos defeituosos ou falhas de operação.
Conclusão
A calibração de manômetro é um aspecto crucial para garantir a precisão e a segurança nos processos industriais. Ao compreender o que é, como é realizada e sua importância, as empresas podem tomar medidas proativas para assegurar que seus instrumentos operem de maneira eficiente e confiante. Manter um programa de calibração regular é uma prática recomendada que não deve ser negligenciada.
Importância da calibração regular
A calibração regular de manômetros é um aspecto essencial para a manutenção da precisão e confiabilidade nos processos de medição de pressão. A seguir, vamos explorar as inúmeras razões que destacam a importância desse procedimento e como ele pode impactar diretamente a eficiência e a segurança em diversas indústrias.
O que é calibração regular?
A calibração regular refere-se à prática contínua de verificar e ajustar instrumentos de medição, como manômetros, em intervalos de tempo determinados. Esse processo envolve a comparação das leituras do manômetro com um padrão conhecido e confiável. A programação de calibrações é fundamental para assegurar que o equipamento esteja sempre funcionando dentro das especificações, atendendo aos padrões estabelecidos.
Garantia de precisão nas medições
Um dos principais objetivos da calibração regular é garantir a precisão das medições feitas pelos manômetros. A precisão é fundamental em setores onde pequenas variações na pressão podem resultar em consequências significativas. Por exemplo, na indústria farmacêutica, medições incorretas de pressão podem comprometer a eficácia dos produtos, levando a riscos para a saúde dos consumidores. Portanto, a calibração regular assegura que o manômetro forneça dados confiáveis e precisos.
Regulamentação e conformidade
Muitas indústrias operam sob regulamentações rigorosas que exigem a calibração regular dos instrumentos de medição. A conformidade com essas normas é vital não apenas para a segurança do produto, mas também para a proteção legal da empresa. Em setores como o alimentício e o farmacêutico, por exemplo, a calibração é frequentemente auditada, e a não conformidade pode resultar em multas severas, recall de produtos e até mesmo ações legais. Portanto, manter um cronograma de calibração regular é uma prática vital que ajuda a garantir a conformidade com as regulamentações.
Segurança operacional
Manômetros descalibrados podem levar a leituras imprecisas, resultando em decisões operacionais equivocadas que podem colocar em risco a segurança da equipe e das instalações. Em processos industriais críticos, como reações químicas, a pressão deve ser controlada com precisão para evitar explosões ou vazamentos. A calibração regular é essencial para garantir que os manômetros estejam fornecendo medições corretas, minimizando o risco de acidentes.
Redução de custos
Embora muitos possam ver a calibração regular como uma despesa, ela pode, na verdade, resultar em economias significativas a longo prazo. Manómetros que não são calibrados adequadamente podem levar a medições erradas, resultando em produtos defeituosos e desperdício de materiais. Além disso, falhas operacionais podem custar muito em termos de tempo de inatividade e reparos. Ao manter o equipamento calibrado, as empresas podem evitar esses custos associados e, assim, melhorar sua linha de receita.
Melhoria na eficiência operacional
A calibração regular de manômetros também contribui para a eficiência operacional. Quando os instrumentos estão precisos e funcionando corretamente, os processos industriais podem ser otimizados. Isso significa menos erros e retrabalho, maior rendimento e aumento na produtividade. Em um ambiente competitivo, ter operações eficientes pode ser o diferencial que posiciona uma empresa na dianteira do mercado.
Aumento da vida útil do equipamento
Além de garantir a precisão, a calibração regular pode ajudar a prolongar a vida útil dos manômetros e outros instrumentos de medição. Quando calibrados adequadamente, os equipamentos funcionam dentro de suas especificações, reduzindo o desgaste e o estresse sobre os componentes. Isso resulta em menos necessidade de reparos e substituições, contribuindo para uma operação mais econômica e sustentável.
Documentação e rastreabilidade
A calibração regular proporciona um registro auditável do histórico de manutenção do equipamento. Esse registro é essencial para rastreabilidade, não apenas para a conformidade regulatória, mas também para a melhoria contínua dos processos. Manter documentação organizada sobre as calibrações realizadas permite que as empresas identifiquem padrões de desempenho e façam ajustes proativos em suas operações.
Impacto na satisfação do cliente
A qualidade consistente dos produtos e serviços é fundamental para manter a satisfação do cliente. Manômetros mal calibrados podem comprometer a qualidade do produto final, resultando em insatisfação e reclamações. Ao garantir que os manômetros sejam calibrados regularmente e forneçam medições precisas, as empresas podem assegurar que estão atendendo às expectativas de seus clientes, o que resulta em fidelização e reputação positiva no mercado.
Conclusão
Em suma, a calibração regular de manômetros é um componente crítico da operação em muitas indústrias. Desde a garantia da precisão nas medições até a conformidade regulatória e a segurança operacional, os benefícios são numerosos e significativos. Portanto, instituir um programa de calibração regular é uma prática que todas as empresas devem considerar. Esse compromisso com a qualidade não apenas protege a empresa, mas também contribui para um ambiente de trabalho seguro e produtivo, beneficiando todas as partes envolvidas, desde as equipes internas até os clientes finais.
Como realizar a calibração de manômetros
A calibração de manômetros é um processo essencial para garantir a precisão das leituras de pressão em diversos sistemas e aplicações. Embora possa parecer uma tarefa técnica complexa, a calibração pode ser realizada eficientemente seguindo algumas etapas fundamentais. Abaixo, descrevemos um guia abrangente que facilitará a realização da calibração de manômetros, abrangendo os principais procedimentos e práticas recomendadas.
Equipamentos necessários para calibração
Antes de iniciar o processo de calibração, é crucial reunir todos os equipamentos e ferramentas necessárias. Os itens fundamentais incluem:
- Manômetro a ser calibrado: O instrumento que será submetido ao processo de calibração.
- Padrão de referência: Um manômetro ou outro dispositivo de medição de pressão calibrado e certificado, que servirá como comparação.
- Fonte de pressão: Um dispositivo capaz de gerar pressões conhecidas, como uma bomba de calibração ou um manômetro com um gerador de vácuo.
- Conexões e mangueiras: Acessórios para conectar os manômetros e a fonte de pressão, garantindo condições adequadas para medições.
- Ferramentas de ajuste: Caso o manômetro precise de ajustes, ferramentas adequadas serão indispensáveis.
- Equipamentos de proteção: É importante utilizar EPI (Equipamentos de Proteção Individual) durante o procedimento para garantir a segurança.
Preparação do ambiente de calibração
Um ambiente controlado é essencial para a calibração precisa dos manômetros. Algumas considerações importantes incluem:
- Temperatura: A calibração deve ser realizada em uma temperatura estável e controlada para evitar flutuações que possam afetar as medições.
- Umidade: O ambiente deve ser seco, já que a umidade excessiva pode interferir nas leituras.
- Vibrações: O local de calibração deve ser isento de vibrações que poderiam afetar o resultado.
Passo a passo para a calibração de manômetros
A seguir, descrevemos as etapas detalhadas para realizar a calibração de manômetros de forma eficaz:
1. Inspeção visual do manômetro
Antes de começar a calibração, faça uma inspeção visual detalhada do manômetro. Verifique se há sinais de dano, corrosão ou obstrução no visor. Um manômetro danificado pode levar a erros de medição e comprometer a precisão do processo.
2. Conexão dos manômetros
Conecte o manômetro a ser calibrado e o padrão de referência à fonte de pressão. A conexão deve ser realizada utilizando mangueiras e adaptadores adequados. A vedação das conexões é essencial para evitar vazamentos, que podem interferir nas medições.
3. Geração de pressão
Ative a fonte de pressão para gerar pressão controlada no sistema. É importante começar com pressões baixas e aumentar gradualmente, fazendo isso em intervalos definidos. Registre os valores de pressão gerados pela fonte e as leituras dígitas de ambos os manômetros (o calibrado e o padrão).
4. Registro das leituras
À medida que a pressão é incrementada, registre as leituras dos dois manômetros em uma tabela ou planilha. Isso ajudará na comparação e análise dos dados. É aconselhável fazer isso em pelo menos cinco pontos diferentes, abrangendo toda a faixa de medição do manômetro em questão.
5. Análise dos dados
Após a coleta das leituras, compare os valores do manômetro a ser calibrado com aqueles do padrão de referência. Essa análise permitirá identificar desvios e erros de medição. A diferença entre os valores pode ser considerada erro sistemático e ajuda a determinar se ajustes são necessários.
Correção e ajustes
Dependendo dos resultados da calibração, pode ser necessário realizar ajustes no manômetro. Essa etapa envolve:
- Ajuste mecânico: Muitos manômetros possuem uma configuração ajustável, geralmente acessível através de um parafuso ou botão. Se a leitura estiver consistentemente acima ou abaixo do padrão, o ajuste deve ser feito com cuidado.
- Correção de software: Em sistemas digitais ou manômetros modernos, pode ser necessário ajustar as configurações de software para garantir uma medição precisa. Isso geralmente é feito através de um menu de configuração.
Documentação do processo de calibração
Após a calibração e ajustes, é vital documentar todo o processo. Essa documentação deve incluir:
- Data e hora da calibração;
- Nome do operador que realizou a calibração;
- Resultados das medições antes e depois do ajuste;
- Condições ambientais durante a calibração;
- Qualquer observação relevante sobre o processo.
Frequência de calibração
A frequência ideal para a calibração de manômetros pode variar dependendo do tipo de aplicação, das condições de operação e dos requisitos regulamentares. No geral, recomenda-se que a calibração seja feita periodicamente, com uma frequência típica variando de três a doze meses. No entanto, manômetros usados em ambientes severos ou críticos podem exigir calibrações mais frequentes.
Considerações adicionais
Além dos passos mencionados, aqui estão algumas considerações extras ao realizar a calibração de manômetros:
- Escolha do momento: Realize a calibração em um tempo alternativo ao uso intensivo, evitando interrupções na produção.
- Pessoal capacitado: Apenas operadores treinados e qualificados devem realizar a calibração, garantindo a integridade do processo.
- Manutenção do padrão de referência: Assegure que o manômetro de referência esteja sempre calibrado e certificado, a fim de garantir medições confiáveis.
Treinamento e atualização
É sempre importante que a equipe responsável pela calibração esteja atualizada sobre as melhores práticas e padrões da indústria. Participar de cursos de formação e workshops pode ajudar na implementação de melhorias e adequações em processos que beneficiem a calibração.
Conclusão
A calibração de manômetros é um procedimento crucial para garantir a precisão das medições de pressão, mantendo a segurança e a eficiência nas operações industriais. Seguindo as etapas descritas neste guia, as empresas podem garantir que seus manômetros estejam sempre calibrados e aptos a fornecer dados confiáveis. A manutenção da precisão das medições não apenas assegura a qualidade do produto final, mas também contribui para a segurança dos trabalhadores e do ambiente operacional.
Erros comuns na calibração de manômetros
A calibração de manômetros é um procedimento essencial para garantir a precisão das medições de pressão em diversas indústrias. No entanto, durante esse processo, vários erros podem ocorrer, comprometendo a confiabilidade das leituras e, consequentemente, a segurança e eficiência das operações. Neste artigo, discutiremos os erros comuns na calibração de manômetros e como evitá-los, garantindo que suas medições sejam sempre precisas.
1. Falta de Preparação Adequada
Um dos erros mais comuns na calibração de manômetros é a falta de preparação adequada antes do processo. Isso envolve não só a verificação do manômetro a ser calibrado, mas também do equipamento de referência e da sala onde a calibração será realizada. É fundamental assegurar que:
- O manômetro esteja limpo e em boas condições de funcionamento.
- O equipamento de referência esteja calibrado e certificado.
- O ambiente de calibração esteja em condições apropriadas (temperatura, umidade e vibrações controladas).
2. Conexões Inadequadas
Conexões ruins entre o manômetro a ser calibrado, o equipamento de referência e a fonte de pressão podem resultar em vazamentos, interferindo nas medições. Para evitar este erro:
- Use mangueiras e conexões adequadas e em bom estado.
- Verifique a vedação de todas as conexões antes de aplicar a pressão.
- Evite usar adaptadores inadequados que possam comprometer a saída de pressão.
3. Aplicação de Pressão Incorreta
Aplicar pressão incorretamente é outro erro comum. Isso pode ocorrer devido a uma calibração apressada ou à falta de um manômetro de referência confiável. Para evitar essa situação, siga estas diretrizes:
- Aumente a pressão de forma gradual, registrando as leituras em pontos definidos.
- Utilize uma fonte de pressão adequada e controle rigorosamente as condições de teste.
- Certifique-se de que as leituras sejam coletadas em uma faixa de pressão relevante para o manômetro em teste.
4. Maneira de Registrar os Dados
Registrar os dados de calibração de maneira inadequada pode levar a erros de interpretação posteriores. Para evitar esse erro, utilize um método de registro que facilite a análise, tais como:
- Criação de uma tabela organizada para comparar os dados do manômetro calibrado e do padrão de referência.
- Registrar todas as condições de calibração, como temperatura e umidade.
- Comprovar os dados de calibração com datas e assinaturas dos responsáveis.
5. Ignorar o Erro Sistemático
Os erros sistemáticos referem-se a desvios consistentes nas medições do manômetro calibrado em comparação com a referência. Ignorar ou não detectar esses erros pode levar a falhas sérias. Para evitar esse problema:
- Realize um teste preliminar, utilizando o manômetro em diferentes pressões antes de aplicar ajustes.
- Documente quaisquer desvios sistemáticos e faça os ajustes necessários com base na análise.
- Considere a frequência de uso e a história de calibração do manômetro a ser calibrado.
6. Falhas nas Correções
Após identificar os desvios, ajustes mecânicos ou de software são frequentemente necessários. No entanto, algumas vezes, essas correções podem ser mal executadas. Para garantir correções precisas, considere:
- Seguir as instruções do fabricante para ajustes mecânicos e de software.
- Realizar a calibração uma segunda vez após os ajustes para garantir a precisão.
- Treinar a equipe sobre as práticas de correção adequadas.
7. Não Documentar o Processo
A falta de documentação completa e precisa do processo de calibração pode levar a problemas futuros relacionados à conformidade e à rastreabilidade. Para evitar esse erro:
- Mantenha registros detalhados sobre cada calibração, incluindo dados de referência e resultados.
- Crie um histórico de calibração para cada instrumento, incluindo datas e responsáveis.
- Armazene a documentação de forma que possa ser facilmente acessada para auditorias.
8. Calibração em Condições Inadequadas
Realizar a calibração em condições inadequadas, como temperaturas extremas ou umidade excessiva, pode afetar os resultados. Para evitar isso:
- Planeje as calibrações em ambientes controlados e estáveis.
- Permita a aclimatação dos instrumentos ao ambiente antes de iniciar o processo de calibração.
- Avalie as condições ambientais regularmente.
9. Subestimar a Frequência de Calibração
Alguns profissionais podem subestimar a quantidade de calibrações necessárias, especialmente em ambientes industriais severos. O não cumprimento do cronograma de calibração regular pode resultar em medições imprecisas ao longo do tempo. Para evitar esse erro:
- Estabeleça um cronograma de calibrações baseado no uso e nas condições de operação do equipamento.
- Revise e ajuste a frequência de calibração com base no histórico do manômetro.
- Treine a equipe para manter registros e relatar qualquer irregularidade que indique a necessidade de uma calibração antecipada.
10. Não Treinamento da Equipe
A falta de treinamento adequado da equipe envolvida na calibração é um dos fatores que pode levar a erros. O pessoal não treinado pode não estar ciente das melhores práticas ou procedimentos corretos. Para garantir a eficácia da calibração:
- Proporcione treinamento contínuo para todos os envolvidos no processo de calibração.
- Utilize simulações e workshops para ensinar as práticas de calibração corretamente.
- Mantenha a equipe atualizada sobre novas tecnologias e procedimentos no campo da calibração.
Conclusão
Os erros comuns na calibração de manômetros podem ter implicações vastas não apenas para a precisão das medições, mas também para a segurança operacional, conformidade e eficiência geral das operações. Compreender esses erros e suas causas é crucial para implementar melhores práticas, garantir a precisão das medições e promover um ambiente de trabalho seguro e eficaz. Capacitar a equipe, manter registros precisos e seguir diretrizes rigorosas de calibração ajudará a mitigar esses erros, assegurando que os manômetros sempre forneçam dados confiáveis para processos industriais.
Em resumo, a calibração de manômetros é um processo crítico que não deve ser subestimado. Garantir a precisão das medições é essencial para a qualidade e segurança dos produtos e serviços em diversas indústrias. Através da compreensão da importância da calibração regular, do conhecimento sobre como realizar o processo de forma eficaz e da identificação dos erros comuns que podem ocorrer, você está equipado para otimizar a operação dos seus manômetros. A implementação de boas práticas de calibração resultará em instrumentos confiáveis, contribuindo para a eficiência operacional e a segurança dos processos. Portanto, não deixe de priorizar a calibração regular e proteja a integridade dos seus dados de medição!