Manutenção Preventiva em Redutores: Guia Completo
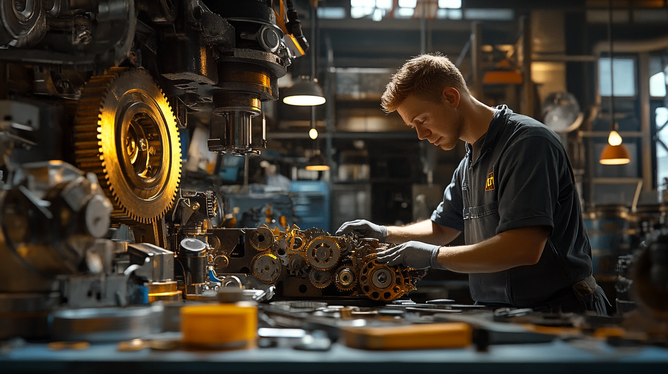
Por: Anderson - 18 de Novembro de 2024
A manutenção preventiva em redutores é crucial para garantir o funcionamento eficiente e a longevidade dos equipamentos. Neste artigo, vamos explorar a importância dessa prática, as principais técnicas que podem ser aplicadas, a frequência recomendada para manutenção e os erros mais comuns a serem evitados. Continue lendo para aprender como otimizar a performance dos seus redutores e evitar problemas futuros.
Importância da Manutenção Preventiva em Redutores
A manutenção preventiva em redutores é uma prática essencial dentro do gerenciamento de ativos industriais. Ela não apenas assegura o funcionamento adequado dos equipamentos, mas também ajuda a evitar paradas inesperadas que podem resultar em grandes prejuízos financeiros e operacionais. Neste contexto, entender a importância dessa abordagem pode trazer benefícios significativos para as operações de qualquer organização.
Os redutores desempenham um papel fundamental na transmissão de potência em maquinários, ajustando a velocidade e o torque de um motor para torná-los adequados a uma determinada aplicação. Por isso, sua manutenção deve ser tratada com seriedade. A não realização de manutenções regulares pode levar à falhas mecânicas, o que, em última análise, compromete a eficiência do sistema e causa danos extensos aos equipamentos.
Um dos principais motivos para implementar a manutenção preventiva em redutores é o aumento da vida útil dos equipamentos. Com a realização de inspeções e ajustes regulares, é possível identificar desgastes ou avarias antes que se tornem problemas graves. Isso significa que componentes críticos podem ser trocados a tempo, evitando danos maiores e desgaste excessivo das peças adjacentes.
Além de aumentar a vida útil, a manutenção preventiva também previne paradas não programadas. Paradas inesperadas podem afetar seriamente a produção, resultando em atrasos e custos adicionais. Ao implementar um plano de manutenção preventiva, as empresas podem planejar as intervenções em horários menos críticos, minimizando o impacto nas operações diárias.
Outro aspecto relevante diz respeito à segurança. Equipamentos em mau estado de funcionamento podem representar riscos sérios para os operadores e outras pessoas na área de trabalho. Fugas de óleo, superaquecimento e falhas mecânicas podem levar a acidentes, colocando em risco a saúde e a segurança dos funcionários. A manutenção preventiva ajuda a garantir que os redutores operem em condições seguras, mitigando esses riscos.
A manutenção preventiva também se traduz em economia. Embora a realização de manutenções regulares possa parecer um custo adicional, na verdade, ela ajuda a evitar gastos muito maiores decorrentes de falhas. Os custos com reparos emergenciais, peças de reposição e o tempo de máquina parada são muitas vezes significativamente maiores do que os gastos com a manutenção regular.
Os benefícios da manutenção preventiva em redutores não param por aqui. Ela também contribui para a melhoria da eficiência operacional. Equipamentos bem mantidos tendem a operar de maneira mais eficiente, reduzindo o consumo de energia e o desperdício. Isso, por sua vez, melhora a sustentabilidade da operação, pois diminui a pegada de carbono e os custos associados ao uso excessivo de energia.
Para garantir uma manutenção preventiva eficaz em redutores, as organizações devem adotar um plano estruturado que inclua inspeções regulares, lubrificação adequada e a troca de peças conforme necessário. Além disso, é importante capacitar a equipe de manutenção, garantindo que eles tenham o conhecimento e as habilidades para detectar problemas antes que se tornem graves.
A implementação de tecnologias como o monitoramento remoto e sensores de vibração também pode ser benéfica. Esses sistemas não apenas permitem que os operadores monitorarem o desempenho dos redutores em tempo real, mas também ajudam a prever falhas antes que ocorram. Com isso, as empresas podem adotar uma abordagem proativa para a manutenção e reduzir ainda mais o tempo de inatividade.
Finalmente, a documentação adequada também é um componente vital da manutenção preventiva. Manter registros detalhados dos serviços realizados, do desempenho dos equipamentos e das condições operacionais ajuda a identificar padrões e tendências, permitindo que as equipes de manutenção tomem decisões informadas sobre futuras intervenções.
Para exemplificar, considere uma indústria de manufatura que possui diversos redutores em sua linha de produção. Se a equipe de manutenção seguir um rigoroso cronograma de manutenção preventiva, a empresa pode desfrutar de uma operação mais suave, menos interrupções e equipamentos com vida útil prolongada. Como resultado, eles não apenas economizam dinheiro em reparos e substituições, mas também garantem uma produção consistente e de alta qualidade.
Em resumo, a manutenção preventiva em redutores é um aspecto crucial que cada organização deve considerar seriamente. Ao implementar práticas de manutenção regulares e proativas, as empresas podem aumentar a eficiência de suas operações, reduzir o risco de falhas e melhorar a segurança no ambiente de trabalho. Além disso, esses cuidados geram economias significativas a longo prazo, tornando-se um investimento valioso para qualquer organização.
Assim, a adoção de uma cultura de manutenção preventiva pode transformar completamente a maneira como a empresa opera. Em vez de reagir aos problemas, a manutenção preventiva permite que as empresas permaneçam à frente, fazendo os ajustes necessários antes que se tornem urgentes. Isso não só maximiza a produtividade, mas também coloca a empresa em uma posição vantajosa em relação à concorrência.
Portanto, é fundamental que as empresas reconheçam a importância da manutenção preventiva em redutores e a integrem em sua estratégia operacional. Ao fazer isso, elas não apenas asseguram a eficiência e a segurança dos seus equipamentos, mas também garantem um futuro mais sustentável e produtivo.
Principais Técnicas de Manutenção Preventiva
A manutenção preventiva é um conjunto de práticas projetadas para evitar falhas, aumentar a vida útil dos equipamentos e garantir operações eficientes, principalmente em redutores. Implementar as técnicas certas de manutenção não só minimiza os custos de operação, mas também melhora a segurança e a confiabilidade dos sistemas. Abaixo, exploraremos algumas das principais técnicas de manutenção preventiva que devem ser adotadas para otimizar o desempenho dos redutores.
Uma das técnicas fundamentais é a **inspeção regular**. Essa abordagem envolve a verificação sistemática dos redutores em intervalos predeterminados para identificar quaisquer sinais de desgaste ou falhas antecipadamente. Durante essas inspeções, pode-se verificar a condição do lubrificante, a integridade das peças, vazamentos e qualquer sinal de superaquecimento. Essa prática é essencial porque muitos problemas são mais fáceis de corrigir quando detectados cedo. As inspeções podem ser realizadas manualmente, mas também podem ser assistidas por tecnologia, como sensores que monitoram as condições em tempo real.
Outro aspecto importante da manutenção preventiva é a **lubrificação adequada**. A lubrificação é crucial para reduzir o atrito entre as partes móveis e minimizar o desgaste das engrenagens. Utilizar o tipo correto de lubrificante, em quantidades corretas, e realizar a lubrificação em intervalos regulares ajuda a garantir que os redutores funcionem de maneira eficaz. É importante também considerar o ambiente em que o redutor está operando, pois fatores como temperatura e contaminação podem influenciar na escolha do lubrificante. Durante as atividades de lubrificação, deve-se sempre verificar o estado e a limpeza das áreas de lubrificação, trocando o lubrificante conforme necessário e assegurando que esteja livre de contaminantes.
Além disso, a **calibração de componentes** é uma técnica que frequentemente é subestimada. Com o tempo, as tolerâncias de operação dos redutores podem mudar devido ao desgaste natural. Portanto, realizar calibrações regulares para assegurar que os redutores estejam funcionando dentro das especificações é essencial. Isso inclui ajustar a tensão da correia, verificar a precisão dos rolamentos e garantir que os eixos estejam alinhados corretamente. Calibrações adequadas não só melhoram a eficiência, mas também reduzem o estresse adicional em componentes que poderiam levar a falhas.
A **substituição programada de peças** é outra técnica essencial que se insere na estratégia de manutenção preventiva. Mesmo com as melhores práticas de manutenção, algumas partes do redutor têm uma vida útil finita. Isso é especialmente verdadeiro para peças que estão sujeitas a desgaste, como rolamentos e vedações. Ao criar um cronograma que preveja a substituição dessas peças antes de chegarem ao fim de sua vida útil, as empresas podem evitar quebras repentinas. Essa abordagem permite que as organizações planejem e orcem para as substituições, garantindo uma alocação eficaz de recursos.
Uma técnica frequentemente usada é o **monitoramento de condições**. Com o avanço da tecnologia, é possível integrar diversas formas de monitoramento aos redutores. Isso inclui a utilização de sensores de vibração, temperatura e pressão que fornecem dados em tempo real sobre as condições operacionais. Com essas informações, é possível realizar manutenções mais focadas e precisas, com base em dados de desempenho. A análise preditiva, que utiliza esses dados para antecipar falhas, pode ser uma adição valiosa ao arsenal de manutenção preventiva. Ao detectar mudanças nos padrões de operação, é possível agir preventivamente antes que ocorram falhas sérias.
Outra técnica importante é a **treinamento contínuo** da equipe de manutenção. Treinar os colaboradores sobre os melhores métodos e práticas de manutenção, bem como sobre as características específicas dos redutores, é vital. Equipamentos e tecnologias estão em constante evolução, e a equipe deve estar atualizada sobre as últimas práticas e tecnologias disponíveis. Além disso, promover uma cultura de segurança no local de trabalho, instigando a equipe a relatar quaisquer anomalias ou preocupações, pode prevenir problemas antes que eles se intensifiquem.
A **documentação meticulosa** também é uma peça chave na manutenção preventiva. Manter registros detalhados das atividades de manutenção, inspeções, substituições de peças e anomalias observadas é fundamental. Essa documentação não só fornece um histórico do redutor, mas também permite a análise de desempenho ao longo do tempo. Quando surgem problemas, a equipe pode consultar os registros para identificar se houve mudanças recentes que possam estar relacionadas ao problema. Além disso, a documentação é crucial para garantir a conformidade com normas e regulamentações de segurança.
Incorporar um **sistema de gerenciamento de manutenção assistida por computador (CMMS)** pode ser uma estratégia eficaz. Um CMMS ajuda a gerenciar todas as facetas da manutenção preventiva, desde o agendamento de tarefas até o rastreamento de peças e a geração de relatórios. Com um CMMS, as equipes podem implementar facilmente cronogramas de manutenção, manter um inventário de peças sobressalentes e gerar relatórios sobre o estado dos equipamentos. Essa abordagem não só agrupa todas as informações cruciais em um local, como também facilita a comunicação entre os membros da equipe e ajuda a garantir que nada seja esquecido.
Em situações específicas, a **análise de falhas** pode ser extremamente útil. Se um redutor falhar, é crucial realizar uma investigação detalhada para entender as causas. Essa análise pode ajudar a evitar que problemas semelhantes ocorram no futuro. Ao identificar quais componentes falharam e por quais motivos, a equipe pode implementar práticas de manutenção que abordem esses pontos fracos. Esse conhecimento pode se tornar parte do treinamento da equipe e também ser documentado para referência futura.
Por último, mas não menos importante, é fundamental promover uma **cultura de manutenção e responsabilidade** dentro da organização. Todos os colaboradores, desde a alta gerência até os operadores, devem entender a importância da manutenção preventiva. Criar programas de incentivo que recompensem o cumprimento de práticas de manutenção e a identificação de problemas em potenciais pode motivar todos a se empenharem em manter os redutores em suas melhores condições. Essa abordagem colaborativa não só melhora a eficiência como reforça a importância de todos no processo de manutenção.
Essas técnicas, quando implementadas corretamente, não apenas aumentam a eficácia do equipamento, mas também oferecem um retorno significativo sobre o investimento. Ao adotar essas práticas, as organizações podem se beneficiar de um funcionamento mais suave, minimização de paradas imprevistas e redução de custos, tornando a manutenção preventiva uma parte fundamental do sucesso operacional.
Em suma, a manutenção preventiva não é uma prática única, mas um conjunto diversificado de atividades e estratégias que devem ser adaptadas às necessidades específicas de cada sistema. As empresas que se comprometem a aplicar as técnicas acima podem esperar um aumento significativo na longevidade de seus redutores e uma melhora geral na eficiência operacional.
Frequência Recomendada para Manutenção
A frequência recomendada para manutenção de redutores é um dos aspectos mais críticos para garantir a eficiência e a longevidade desses equipamentos. A implementação de um cronograma adequado de manutenção não apenas melhora o desempenho, mas também reduz o risco de falhas inesperadas, o que pode levar a custos significativos e interrupções nas operações. Neste texto, discutiremos como determinar a frequência de manutenção ideal para redutores, levando em consideração vários fatores que influenciam essa decisão.
Um dos primeiros passos na definição da frequência de manutenção é compreender o **tipo de operação** em que o redutor está inserido. Redutores que operam em ambientes mais severos, onde estão expostos a altas temperaturas, umidade, contaminantes ou vibrações excessivas, normalmente requerem uma manutenção mais frequente. Nesses casos, as condições ambientais podem acelerar o desgaste dos componentes, tornando crucial realizar inspeções e serviços mais regulares. Por outro lado, em ambientes controlados e menos agressivos, pode ser possível ampliar os intervalos de manutenção.
Além das condições operacionais, o **nível de utilização** do equipamento também influencia a frequência de manutenção. Redutores que trabalham em turnos contínuos ou em aplicações que exigem altos ciclos de operação podem demandar inspeções mais frequentes. Por exemplo, um redutor utilizado em uma linha de produção que opera 24 horas por dia, 7 dias por semana, deve ser inspecionado com mais regularidade do que um redutor que funciona apenas em períodos intermitentes. Um critério comum é realizar a manutenção preventiva a cada 500 horas de operação para situações de alta demanda, mas ajustes podem ser necessários conforme a experiência operacional.
Os **fabricantes de redutores** frequentemente fornecem orientações sobre a frequência de manutenção recomendada, levando em consideração o projeto específico dos equipamentos. Essas orientações devem ser vistas como pontos de partida. Avaliar a condição específica do sistema e dos componentes é vital. Além disso, a documentação dos históricos de manutenção e falhas pode auxiliar na definição de um cronograma mais ajustado às necessidades reais do equipamento.
Outra abordagem eficaz é a utilização de **sensores e tecnologias de monitoramento** para avaliação em tempo real. A análise de dados obtidos por sensores de vibração, temperatura e fadiga pode informar quando é necessário realizar manutenção, em vez de seguir apenas um cronograma fixo. Essa estratégia permite que as empresas adotem uma abordagem mais proativa, evitando quebras indesejadas e prolongando a vida útil dos redutores. Utilizar técnicas de manutenção preditiva pode reduzir custos no longo prazo e simplificar o planejamento operacional.
Para redutores que são expostos a ambientes menos agressivos e operam em condições normais, uma frequência de manutenção semestral pode ser apropriada. Essas manutenções podem envolver inspeções visuais, lubrificação e verificação das condições operacionais. Além disso, a manutenção mais profunda, que pode incluir a substituição de peças e a lubrificação dos componentes internos, pode ser realizada anualmente. Essa programação garante que os redutores permaneçam em condições ideais, prontamente ajustados para evitar falhas de desempenho.
Adotar um **cronograma de manutenção diversificado** é fundamental. Ao planejar diferentes níveis de manutenção, é possível realizar verificações regulares que não exigem paradas longas, além de manutenções mais profundas que podem ser programadas durante períodos de baixa produção. É aconselhável reservar um tempo de inatividade para a manutenção programada em vez de se arriscar a interrupções inesperadas. Em alguns casos, a utilização de shutdowns planejados para realizar manutenções completas pode minimizar os impactos na produção e assegurar que o equipamento funcione de forma eficiente.
A **documentação e análise de condições** são peças importantes na definição de frequência de manutenção. Registrar as condições dos redutores após cada manutenção é fundamental para entender como o equipamento se comporta ao longo do tempo. Um histórico claro pode identificar padrões que ajudam a ajustar o cronograma de manutenção de maneira eficaz. Com documentação adequada, é possível analisar quando os redutores começaram a apresentar problemas e correlacionar isso com a frequência da manutenção realizada anteriormente.
Os **treinamentos e a capacitação dos operadores** também influenciam na eficácia da manutenção preventiva. Operadores que conhecem as especificações e os limites de operação dos redutores podem identificar problemas com mais precisão e rapidez. Isso permite realizar intervencões preventivas mais eficazes, podendo reportar condições anormais antes que se agravem. Portanto, incentivar um ambiente de trabalho em que operadores estejam atentos e informados é parte essencial da cultura de manutenção.
Outras técnicas que podem ser aplicadas incluem o uso do conceito de **Análise de Criticidade**. Essa abordagem permite que as empresas classifiquem seus redutores de acordo com seu impacto na operação. Redutores que desempenham funções críticas devem ter uma frequência de manutenção mais alta, enquanto equipamentos menos essenciais podem ter intervalos maiores. Essa análise deve incluir a análise dos custos que os redutores críticos podem gerar se falharem, ajudando a priorizar o cronograma de manutenção conforme as necessidades operacionais.
O **feedback e as experiências passadas** também desempenham um papel importante na definição da frequência de manutenção. Aprender com experiências anteriores, tanto positivas quanto negativas, ajuda na formulação de uma estratégia de manutenção mais eficaz. Converse com a equipe de manutenção, operadores e outros stakeholders para coletar informações sobre os problemas enfrentados e as soluções aplicadas. Essa troca de conhecimentos pode proporcionar insights valiosos para aprimorar o planejamento de manutenção.
Por fim, deve haver um equilíbrio entre a manutenção **preemptiva** e **reativa**. Muitas vezes, a manutenção é realizada apenas quando um problema maior se manifesta. No entanto, o ideal é criar um equilíbrio que permita que a maioria da manutenção prevista seja executada antes de haver um problema. Com um planejamento eficaz, intervenções programadas são realizadas sempre que possível, enquanto os equipamentos continuam a operar sem interrupções indesejadas.
Em resumo, a frequência recomendada para manutenção em redutores deve ser determinada com base em uma avaliação integrada das condições operacionais, especificações do fabricante, análise de dados e experiências passadas. A criação de um cronograma de manutenção adequado, que não só leve em conta a rotina de operação, mas também as condições ambientais e características específicas de cada redutor, é fundamental para assegurar a continuidade das operações e a redução dos custos associados a falhas inesperadas. Implementar tecnologias de monitoramento e capacitar a equipe são estratégias que contribuem para uma abordagem de manutenção mais eficaz e proativa, garantindo que os redutores funcionem de forma otimizada ao longo do tempo.
Erros Comuns na Manutenção de Redutores
A manutenção de redutores é uma parte crítica da gestão de ativos em muitas indústrias, pois garante a eficiência e a segurança dos equipamentos. No entanto, muitos usuários e equipes de manutenção cometem erros que podem levar a falhas dispendiosas e a uma vida útil reduzida dos redutores. Neste artigo, abordaremos os erros mais comuns na manutenção de redutores, suas causas e como evitá-los para garantir um desempenho ideal.
Um dos erros mais frequentes é a **neglectância da manutenção preventiva**. Muitas empresas subestimam a importância das manutenções regulares, acreditando que os redutores podem operar indefinidamente sem a necessidade de intervenções. Essa abordagem reativa pode ser fatal, pois falhas mecânicas podem ocorrer sem aviso prévio. Ao não seguir um cronograma de manutenção preventiva, os usuários se arriscam a experimentar custos significativos de reparo e perda de produção devido a paradas inesperadas. Portanto, é essencial que as operações estabeleçam e sigam um plano de manutenção que inclua inspeções e lubrificações regulares.
Outro erro comum é a **falta de registro e documentação** durante os serviços de manutenção. A manutenção sem documentação apropriada pode levar a legados de conhecimento perdidos e a repetições desnecessárias de erros. Por exemplo, se um problema específico foi corrigido no passado, mas não há registros sobre as ações tomadas, pode-se acabar cometendo o mesmo erro no futuro. Manter um registro completo das atividades de manutenção reduz os riscos de falhas e ajuda as equipes a tomar decisões mais informadas. Portanto, investir tempo na documentação das manutenções realizadas é fundamental.
A **escolha inadequada de lubrificantes** também é uma armadilha comum. Utilizar um lubrificante que não é apropriado para o ambiente operacional do redutor pode levar ao desgaste acelerado das peças. Cada redutor exige um tipo específico de lubrificante, considerando fatores como a temperatura de operação e a presença de contaminantes. Além disso, a falta de lubrificação ou a aplicação excessiva podem resultar em problemas de atrito ou superaquecimento. Assim, é fundamental que a equipe de manutenção esteja ciente das especificações do fabricante e siga as diretrizes para a lubrificação correta.
Um erro muitas vezes observado é a **não calibração dos redutores**. Calibrações regulares ajudam a garantir que os redutores operem dentro das especificações e não sofram desgastes desnecessários. A falha na calibração pode resultar em desvio de desempenho, altos níveis de vibração e desgaste acelerado das engrenagens. Portanto, é vital que as intervenções de calibração sejam realizadas em intervalos regulares, além de garantir que a equipe de manutenção tenha as ferramentas e conhecimentos necessários para fazê-lo adequadamente.
Além disso, muitos profissionais ignoram a **falta de treinamento e capacitação** adequada. É comum que as equipes de manutenção não sejam treinadas o suficiente sobre as especificações dos redutores e as melhores práticas de manutenção. Isso pode resultar em intervenções inadequadas, falhas na identificação de problemas e até mesmo danos acidentais aos componentes durante a manutenção. As empresas devem investir em treinamentos regulares para suas equipes, garantindo que todos estejam atualizados sobre as práticas recomendadas e as tecnologias mais recentes para a manutenção de redutores.
A **subestimação do ambiente operacional** é outro erro frequente. O desempenho e a durabilidade dos redutores podem ser seriamente afetados por condições ambientais como temperatura, umidade, poeira e vibração. Por exemplo, redutores que operam em ambientes hostis podem exigir intervalos de manutenção mais curtos. Não levar em consideração as condições ambientais durante a escolha dos intervalos de manutenção pode resultar em falhas. Portanto, é importante que as equipes avaliem essas condições e ajustem os cronogramas de manutenção conforme necessário.
Um erro comum é a **falta de comunicação** entre os operadores e a equipe de manutenção. Muitas vezes, problemas que foram notados pelos operadores não são relatados de forma oportuna à equipe de manutenção, resultando em falhas mais graves. A comunicação eficaz entre esses grupos é essencial para garantir que os problemas sejam abordados antes que se agravem. Estabelecer um canal de feedback claro e promover uma cultura onde os operadores se sintam confortáveis em relatar anomalias é crucial para a eficácia do programa de manutenção.
Outro erro a ser evitado é a **implementação inadequada de tecnologias de monitoramento**. Embora as tecnologias modernas de monitoramento, como sensores de vibração e temperatura, ofereçam oportunidades incríveis para otimizar a manutenção, algumas empresas não as utilizam corretamente. Isso pode incluir a instalação inadequada de sensores, erros na interpretação de dados ou mesmo a falta de integração com sistemas de gerenciamento. Para garantir que essas tecnologias tragam benefícios, as equipes devem receber orientação adequada sobre como configurar, interpretar e agir com base nas informações fornecidas.
Um erro menos frequentemente mencionado é a **falta de priorização na execução de manutenções**. Em termos práticos, pode ser tentador realizar manutenções menores e deixar de lado as questões mais críticas devido à falta de tempo ou recursos. Contudo, isso pode resultar em problemas maiores no futuro. A equipe de manutenção deve avaliar e priorizar tarefas com base no impacto potencial que cada uma pode ter na operação. Um sistema de gestão que priorize as manutenções mais críticas vai garantir que os redutores permanecerão operacionais e evitará paradas inesperadas.
Outro aspecto importante é a **tradição de utilizar métodos obsoletos** de manutenção. Muitas empresas ainda se baseiam em velhos hábitos em vez de adotar novas abordagens mais eficientes, como a manutenção preditiva e baseada em condição. Essa resistência à mudança pode se manifestar na falta de atualização das práticas de manutenção, mantendo as equipes presas a métodos ultrapassados que não atendem mais às necessidades operacionais atuais. Para evitar esse tipo de erro, as organizações devem estar abertas a novas tecnologias e métodos, investindo em inovação e atualização das práticas de manutenção.
Alguns profissionais ainda cometem o erro de **subestimar a importância da substituição de peças**. Se uma peça de um redutor mostra sinais de desgaste, ignorá-la e continuar a operação normalmente pode resultar em falhas significativas. Muitas vezes, as empresas hesitam em substituir peças com medo do custo, mas isso geralmente gera custos ainda maiores no futuro. Um cronograma de substituição regular deve ser integrado à manutenção preventiva, garantindo que cada peça crítica seja verificada e trocada quando necessário.
Por fim, um erro comum é a **reação inadequada a falhas**. Quando uma falha ocorre, algumas equipes podem optar por tomada de ação precipitada sem realizar uma análise correta da situação. Ao invés de resolver a causa raiz do problema, podem adotar soluções temporárias que não resolverão a questão subjacente. Isso muitas vezes resulta em falhas recorrentes. Portanto, é essencial realizar análise de falhas sempre que um problema surgir, para identificar não apenas o que ocorreu, mas por que ocorreu e como evitá-lo no futuro.
Em resumo, a manutenção de redutores é um processo complexo que pode ser aprimorado por meio da vigilância e da eliminação dos erros comuns mencionados. Ao investir na criação de um plano robusto de manutenção que inclua documentação adequada, formação de pessoal, escolha correta de lubrificantes, comunicações eficazes, e a atualização contínua sobre as melhores práticas, as empresas podem reduzir significativamente as paradas indesejadas e prolongar a vida útil dos equipamentos. Esses esforços não só resultam em operações de maior eficiência, mas também em um uso mais inteligente dos recursos e um impacto positivo nos resultados financeiros.
Em conclusão, a manutenção preventiva em redutores é um elemento vital para garantir que esses equipamentos operem de maneira eficiente e confiável ao longo do tempo. Como discutido, essa prática não apenas aumenta a vida útil dos redutores, mas também previne falhas inesperadas que podem resultar em paradas demoradas e custos elevados. A adoção de técnicas eficazes, a discussão sobre a frequência de manutenção e a conscientização sobre os erros comuns são passos cruciais para maximizar o desempenho dos equipamentos. Ao implementar um plano robusto de manutenção preventiva, as empresas não só otimizarão a performance dos seus redutores, mas também promoverão um ambiente de trabalho mais seguro e produtivo. Portanto, é essencial que todos os envolvidos no processo de manutenção se comprometam a seguir as melhores práticas discutidas, garantindo assim a eficiência e a sustentabilidade das operações. Que tal começar agora mesmo a aplicar essas estratégias e observar os benefícios que uma manutenção preventiva eficaz pode trazer para o seu negócio?