Procedimento de calibração de manômetros em 5 etapas
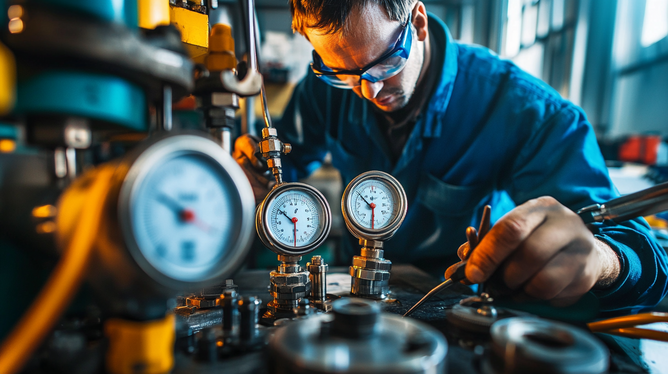
Por: Anderson - 19 de Novembro de 2024
O procedimento de calibração de manômetros é fundamental para garantir a precisão nas medições de pressão em diversos setores. Neste artigo, você aprenderá sobre a importância dessa calibração, as etapas necessárias para realizá-la corretamente, as ferramentas essenciais e os cuidados que devem ser tomados após a calibração. Com essas informações, você poderá assegurar que seus manômetros operem com a máxima eficiência, evitando problemas que possam impactar a qualidade do seu trabalho. Continue lendo e descubra como otimizar o desempenho desses instrumentos indispensáveis.
Importância da calibração de manômetros
A calibração de manômetros é um aspecto crítico no controle de qualidade e na manutenção de precisão nos processos industriais e laboratoriais. A importância desse procedimento transcende a simples verificação de um instrumento; trata-se de garantir que as medições realizadas estejam dentro de parâmetros aceitáveis para a operação segura e eficiente de equipamentos. Neste conteúdo, exploraremos as razões pelas quais a calibração de manômetros é essencial e os impactos diretos que ela tem no desempenho das operações.
Precisão nas medições
A precisão nas medições de pressão é vital em diversas indústrias, incluindo a farmacêutica, alimentícia, petroquímica e de energia. Equipamentos que dependem de manômetros para medir a pressão de gás, líquidos ou vapores precisam de medições confiáveis para evitar falhas operacionais. Um manômetro descalibrado pode resultar em leituras incorretas, levando a decisões erradas e potenciais riscos, como explosões ou vazamentos de substâncias perigosas.
No setor farmacêutico, por exemplo, uma medição imprecisa da pressão pode comprometer a qualidade dos produtos finais, causando contaminações ou variações que não atendem aos padrões de segurança. Portanto, a calibração regular dos manômetros é uma prática recomendada para assegurar que esses instrumentos estejam sempre atualizados e funcionando adequadamente.
Conformidade com normas e regulamentos
Além da precisão, a calibração de manômetros é geralmente uma exigência normativa. Muitas indústrias operam sob rigorosas regulamentações que exigem a calificação e manutenção regular dos equipamentos de medição. Estas normas são estabelecidas por órgãos reguladores, como a Anvisa no Brasil, e garantem que os equipamentos utilizados atendam a padrões de segurança e eficácia.
Empresas que não seguem essas diretrizes podem enfrentar penalidades, como multas e até interdições temporárias de suas operações. Portanto, manter os manômetros calibrados não é apenas uma questão de precisão, mas também de conformidade legal. A realização deste procedimento regularmente ajuda a empresa a evitar problemas legais e a manter sua reputação no mercado.
Economia e eficiência operacional
A calibração de manômetros deve ser vista como um investimento a longo prazo que pode resultar em economia significativa. Manômetros que não são calibrados corretamente podem levar a perdas de matéria-prima, investimentos em manutenção corretiva e paradas não planejadas. A precisão nas leituras de pressão permite um melhor controle dos processos, o que otimiza o uso de recursos e reduz desperdícios.
Por exemplo, quando um manômetro mede uma pressão mais baixa do que a real, pode-se acabar utilizando mais energia ou matérias-primas para alcançar os mesmos resultados, elevando os custos operacionais. Da mesma forma, uma leitura enganosa pode forçar uma manutenção excessiva do equipamento, aumentando o tempo de inatividade e, consequentemente, os custos com mantimentos e reparos. A calibração regular ajuda a evitar esses problemas, aumentando a eficiência e a produtividade da empresa.
Prevenção de falhas e acidentes
A calibração correta dos manômetros é crucial para a segurança no ambiente de trabalho. A medição imprecisa da pressão pode resultar em falhas catastróficas em equipamentos, causando ferimentos aos trabalhadores e danos ao ambiente. Em setores como o de petróleo e gás, onde a pressão desempenha um papel vital, uma falha de medição pode resultar em explosões e contaminações ambientais.
Adicionalmente, muitos processos industriais funcionam em condições extremas de pressão e temperatura, e manômetros descalibrados podem não apenas comprometer as medições, mas também danificar os equipamentos ou resultar em interrupções no fluxo de produção. Portanto, a calibração desempenha um papel importante na prevenção de acidentes e na proteção do capital humano e físico da empresa.
Estabilidade e desempenho do sistema
A estabilidade das operações industriais está intimamente ligada à precisão das medições realizadas pelos manômetros. A calibração garante que os instrumentos estejam dentro das especificações desejadas, o que melhora a previsibilidade dos processos. Sistemas que operam com pressão bem controlada permitem um melhor desempenho geral e minimizam variações que podem causar problemas de qualidade.
Com manômetros calibrados, os operadores podem identificar rapidamente anomalias e tomar decisões com base em dados confiáveis, evitando surpresas no processo produtivo. Essa previsibilidade não apenas melhora a qualidade dos produtos finais, mas também aumenta a confiança dos colaboradores e a satisfação dos clientes.
Impacto na reputação da empresa
A calibração regular dos manômetros demonstra um compromisso com a qualidade e a segurança, algo que é muito valorizado por clientes e parceiros de negócios. Empresas que implementam boas práticas de calibração são vistas como mais confiáveis e são capazes de construir uma reputação forte no mercado. Isso pode, por sua vez, abrir portas para novas oportunidades de negócios e parcerias.
A confiança que se estabelece por meio de medições precisas pode ser um diferencial competitivo em um mercado cada vez mais exigente. Os clientes estão cada vez mais atentos à qualidade dos produtos e serviços oferecidos, e investir na calibração dos manômetros é uma maneira de garantir que a empresa mantenha um padrão elevado e consistente.
Conclusão
Em resumo, a calibração de manômetros é um procedimento indispensável que impacta a precisão, a conformidade legal, a eficiência operacional, a segurança e a reputação de uma empresa. Não se trata apenas de manter os instrumentos atualizados, mas de estabelecer um padrão elevado de qualidade e segurança. Implementar um cronograma regular de calibração garante que os manômetros continuem a desempenhar suas funções corretamente, proporcionando um ambiente de trabalho seguro e produtivo. As vantagens de manter os manômetros calibrados vão muito além da economia e eficiência, sendo investissements diretos na qualidade e reputação da empresa no mercado.
Etapas do procedimento de calibração
O procedimento de calibração de manômetros é uma prática essencial que garante a precisão das medições de pressão. Para garantir que esse processo seja eficiente, é fundamental seguir uma série de etapas bem definidas. Abaixo, apresentamos um guia passo a passo sobre as etapas envolvidas no procedimento de calibração de manômetros.
1. Preparação e planejamento
A primeira etapa para o sucesso da calibração de manômetros é a preparação. Isso inclui o planejamento da calibração de acordo com as necessidades da operação e a análise das especificações do manômetro. É importante verificar a documentação técnica do equipamento, que inclui informações como faixa de medição, tipo de pressão (absoluta, manométrica ou diferencial) e precisão. Este planejamento prévio ajudará a evitar imprevistos durante o processo de calibração.
Outra consideração nesse estágio é agendar a calibração em um momento que minimize a interrupção da produção. Isso geralmente significa escolher períodos de baixa demanda ou programar a calibração durante turnos em que o uso do manômetro não seja crucial. Um planejamento adequado neste estágio pode economizar tempo e recursos no futuro.
2. Reunião das ferramentas e equipamentos necessários
Depois de planejar, a próxima etapa é reunir todas as ferramentas e equipamentos necessários para a calibração. Os instrumentos mais comuns utilizados no processo de calibração incluem:
- Pressurizador ou calibrador de pressão;
- Fonte de pressão padrão;
- Termômetro (se necessário);
- Conectores e tubos de pressão;
- Registro de calibração ou software para documentação.
É essencial verificar se todos os equipamentos estão em boas condições de funcionamento antes de iniciar o procedimento. Uma ferramenta inadequada pode resultar em medições imprecisas e comprometer todo o processo de calibração.
3. Verificação do instrumento de referência
Antes de iniciar a calibração do manômetro que está sendo testado, é importante verificar o instrumento de referência que será utilizado durante o processo. Esse instrumento de referência deve ter uma calibração recém-realizada e ser rastreável a padrões de laboratório nacionais ou internacionais. A precisão do instrumento de referência é crucial, pois qualquer erro nesse equipamento irá afetar diretamente a calibração do manômetro em teste.
Um procedimento comum é realizar uma verificação inicial ao aplicar pressão no instrumento de referência e comparar os resultados com os valores esperados. Se o instrumento de referência apresentar desvios significativos, a calibração do manômetro em questão não será confiável.
4. Conexão do manômetro e do instrumento de referência
Uma vez verificado o instrumento de referência, o próximo passo é conectar o manômetro a ser calibrado e o instrumento de referência ao sistema de pressão. É imprescindível que essas conexões sejam feitas de maneira adequada para evitar vazamentos, que podem comprometer os resultados da calibração.
Após a conexão, atente-se para a presença de ar ou bolhas dentro do sistema, pois isso pode influenciar as medições. Por isso, muitos profissionais recomendam realizar um purgamento do sistema para eliminar qualquer ar ou impurezas antes de iniciar a calibração.
5. Aplicação de pressão e registro das leituras
Uma vez que tudo está preparado e conectado, é hora de aplicar pressão ao sistema. A pressão deve ser aumentada gradualmente, e é aconselhável fazer isso em incrementos, começando do zero até a pressão máxima especificada para o manômetro. Durante essa aplicação de pressão, é importante registrar cuidadosamente as leituras tanto do manômetro em teste quanto do instrumento de referência.
Um exemplo de procedimento inclui ajustar a pressão em dois ou três pontos bem definidos, como 25%, 50% e 75% da faixa total do manômetro. Em cada um desses pontos, devem ser realizadas medições estáveis, permitindo que as leituras se estabilizem antes de serem registradas.
6. Análise das medições e cálculo da correção
A próxima etapa envolve a análise das medições registradas. Para cada ponto de pressão aplicado, compare os valores obtidos pelo manômetro em teste com os valores do instrumento de referência. Isso permitirá identificar quaisquer desvios e a necessidade de ajustes.
Um gráfico de comparação pode ser criado para visualizar melhor a diferença entre as leituras do manômetro calibrado e o instrumento de referência. A partir dessa comparação, podem ser realizados cálculos para determinar o fator de correção, caso necessário. Este fator será utilizado para ajustar as leituras do manômetro em teste, garantindo que elas estejam mais alinhadas com as medições reais.
7. Ajustes necessários
Se a análise das medições indicar que o manômetro está fora das especificações desejadas, ajustes deverão ser feitos. Esses ajustes podem ser realizados de várias maneiras, dependendo do tipo de manômetro. Por exemplo, muitos manômetros modernos têm um mecanismo de ajuste que permite calibrar o zero ou a escala sem necessidade de desmontagem.
Se o manômetro não permitir ajustes manuais, pode ser necessária uma recalibração mais abrangente, o que pode incluir a substituição de componentes ou até mesmo a retificação do equipamento. O importante é garantir que, após esses ajustes, as medições do manômetro estejam dentro das especificações adequadas.
8. Documentação do processo de calibração
Após a calibração, é essencial documentar todo o processo. A documentação deve incluir informações como a data da calibração, valores de referência, recepção de ajustes, instrumentos utilizados e todos os resultados obtidos. Essa documentação é importante para garantir que há um registro histórico do estado do manômetro, e pode ser exigido durante auditorias de qualidade ou inspeções.
Adicionalmente, a documentação serve como uma referência para futuras calibrações e ajuda a identificar tendências que podem indicar desgaste ou necessidade de manutenção do manômetro ao longo do tempo.
9. Teste final e verificação
Antes de reintegrar o manômetro calibrado ao sistema operacional ou à linha de produção, recomenda-se realizar um teste final. Esse teste deve consistir na aplicação de pressão novamente para confirmar que as leituras agora estão corretas e dentro dos parâmetros desejados. Isso garante que o processo de calibração foi bem-sucedido e que o manômetro pode operar com precisão.
Os resultados desse teste final devem ser registrados, assim como os resultados iniciais, para formar um conjunto de dados completos sobre a calibração do manômetro.
10. Programação de calibrações futuras
Após concluir o procedimento de calibração de um manômetro, é necessário programar calibrações futuras. A determinação da frequência de calibração varia de acordo com o tipo de manômetro, as condições de operação e as exigências regulamentares. No geral, muitos manômetros requerem calibrações a cada seis meses, anualmente ou conforme o uso, mas deve-se analisar cada caso individualmente.
Manter um cronograma regular de calibração ajuda a assegurar que todos os manômetros estejam sempre em condições ideais de operação, garantindo assim a precisão contínua das medições e a segurança das operações.
Considerações finais
Realizar a calibração dos manômetros de maneira sistemática é um elemento essencial para garantir a precisão e a segurança em diversos setores. Seguir cada uma das etapas mencionadas não apenas assegura a qualidade das medições, mas também traz benefícios econômicos, de segurança e de conformidade regulatória. Portanto, é fundamental que as práticas de calibração sejam sempre reconhecidas e implementadas como parte integrante da operação e do controle de qualidade. A adesão a um procedimento estruturado e rigoroso de calibração reflete o compromisso da empresa com a excelência e a dependabilidade dos seus processos.
Ferramentas necessárias para a calibração
A calibração de manômetros é uma tarefa que requer precisão e atenção aos detalhes. Para garantir que esse procedimento seja realizado de maneira eficiente e eficaz, é essencial ter à disposição as ferramentas corretas. Abaixo, apresentamos uma lista abrangente das ferramentas necessárias para a calibração de manômetros, além de explicações sobre a função de cada uma delas e como elas contribuem para a precisão das medições.
1. Manômetro de referência
Um manômetro de referência é um instrumento de medição altamente preciso que serve como padrão durante o processo de calibração. A escolha do manômetro de referência é fundamental, pois ele deve ter sido calibrado recentemente e ser rastreável a padrões reconhecidos nacional ou internacionalmente. Isso garante que as medições sejam fiáveis e que qualquer erro na calibração do manômetro em teste possa ser identificado e corrigido.
Existem diferentes tipos de manômetros de referência, incluindo manômetros de precisão digitais e analógicos. Os manômetros digitais, em geral, oferecem maior facilidade de leitura e são menos suscetíveis a erros de parallax, sendo preferidos na maioria das aplicações industriais.
2. Fonte de pressão padrão
Uma fonte de pressão padrão é uma ferramenta essencial que permite a geração de pressões conhecidas e controladas, que serão aplicadas ao manômetro a ser calibrado. Esta fonte pode ser um cilindro de gás pressurizado, um dispositivo pneumático ou hidráulico, ou uma bomba de pressão. O importante é que a fonte de pressão utilizada seja capaz de fornecer uma faixa de pressão que cubra adequadamente os valores que o manômetro em teste apresentará durante seu uso normal.
Além disso, a fonte de pressão deve ter um monitoramento adequado para garantir a estabilidade e a precisão da pressão aplicada. Calibrar a fonte de pressão em intervalos programados também é uma boa prática, pois a precisão de seu funcionamento afetará diretamente a calibração do manômetro.
3. Pressurizador ou calibrador de pressão
Um pressurizador ou calibrador de pressão pode ser utilizado como uma alternativa para aplicar pressão precisa ao manômetro que está sendo calibrado. Este dispositivo gera uma pressão controlada que pode ser medida e ajustada com alta precisão. Calibradores de pressão são frequentemente projetados para funcionar em uma variedade de faixas de pressão e geralmente incluem recursos para facilitar a medição e ajustes rápidos.
Esses dispositivos vêm em diferentes formatos, desde manômetros simples com escala até calibradores digitais, que oferecem uma ampla gama de funções, como armazenar dados de calibração e imprimir relatórios.
4. Conectores e tubos de pressão
Para conectar o manômetro em teste ao sistema de pressão, é necessário ter uma variedade de conectores e tubos de pressão. Essas peças garantem uma conexão hermética e devem ser adequadas para suportar as pressões aplicadas. É fundamental que não haja vazamentos no sistema, pois isso pode comprometê-lo e levar a medições imprecisas.
As opções de tubos de pressão variam em diâmetro e material, sendo importante escolher o tipo adequado para a aplicação. Mangueiras de borracha, tubos de aço inoxidável e conexões rápidas são algumas das opções disponíveis. Verifique se todos esses componentes estão em boas condições e livres de desgaste antes do uso.
5. Termômetro
Embora a calibração de manômetros se concentre principalmente na pressão, a temperatura também pode influenciar o desempenho dos equipamentos. Em situações onde as medições de pressão são sensíveis à temperatura, é recomendável ter um termômetro à disposição para monitorar as condições ambientais durante o processo de calibração.
Os termômetros digitais são uma escolha popular devido à sua precisão e facilidade de leitura. O controle da temperatura pode ser crucial, especialmente em aplicações industriais onde alterações térmicas podem afetar a precisão dos instrumentos de medição.
6. Registro de calibração e software de documentação
A documentação do processo de calibração é vital para o controle de qualidade e para rastreamento no caso de inspeções ou auditorias. Para isso, é aconselhável ter à disposição um registro de calibração onde todos os dados relevantes sejam registrados. Muitas vezes, pode até ser interessante utilizar um software especializado, que facilite o rastreamento e armazenamento de informações.
Esses softwares oferecem funcionalidades que permitem ao usuário criar relatórios, programar futuras calibrações e manter registros históricos, ajudando na administração e na conformidade com normas e regulamentações.
7. Conjunto de ferramentas manuais
Um conjunto básico de ferramentas manuais é sempre uma adição valiosa em todo o processo de calibração. Ferramentas como chaves de fenda, alicates, chaves inglesas e outras podem ser necessárias para ajustes e manutenção durante o procedimento de calibração. Garanta que essas ferramentas estejam organizadas e acessíveis para que ajustes e reparos possam ser realizados rapidamente, mantendo a eficiência do processo.
8. Equipamento de proteção individual (EPI)
A segurança deve ser uma prioridade no ambiente de trabalho durante a calibração de manômetros. Portanto, o uso de Equipamentos de Proteção Individual (EPI) é essencial. Isso pode incluir luvas, óculos de proteção, protetores auriculares e, dependendo do ambiente, vestimentas especiais para proteção contra produtos químicos ou temperatura extrema.
Assegure-se de que todos os profissionais envolvidos na calibração estejam cientes dos protocolos de segurança e estejam adequadamente equipados. A falta de precauções adequadas pode resultar em acidentes que podem ser evitados.
9. Certificações e calibrações anteriores
Outro aspecto importante durante a calibração de manômetros é ter acesso a certificações e registros de calibrações anteriores. Isso inclui verificar a data da última calibração e quaisquer outros relatórios relevantes que possam influenciar o processo. Os responsáveis pela calibração devem ser familiarizados com os padrões necessários e os requisitos associados e, a partir dessa documentação, tomar decisões sobre a situação atual do manômetro e a necessidade de novas calibrações.
10. Manutenção e cuidados pós-calibração
A manutenção contínua dos instrumentos e ferramentas utilizadas na calibração também é uma parte importante do processo. Após a calibração, todos os dispositivos e ferramentas devem ser devidamente limpos e verificados para garantir que permanecerão em boas condições até a próxima vez que forem utilizados. Estabelecer rotinas de verificação e manutenção pode ajudar a prolongar a vida útil do equipamento e evitar erros futuros.
A periodização de inspeções e manutenções preventivas deve ser parte integrante do plano de calibração. Isso garante que qualquer desgaste ou danos sejam identificados e corrigidos antes que comprometam a precisão das medições.
11. Treinamento e qualificação da equipe
Ter as ferramentas corretas é apenas uma parte do quebra-cabeça; igualmente importante é garantir que a equipe responsável pela calibração esteja bem treinada e qualificada. Os profissionais que realizam a calibração devem ter conhecimento técnico sobre os manômetros, as ferramentas utilizadas e os procedimentos a serem seguidos. Investir em treinamento aumenta consideravelmente a eficiência e a precisão durante a calibração, além de garantir a segurança dos envolvidos.
Programas regulares de treinamento podem incluir workshops, cursos de atualização e certificações que mantenham a equipe informada sobre as melhores práticas e inovações tecnológicas no campo da calibração.
Concluindo
Dobrar esforços na preparação e execução da calibração de manômetros resulta em um processo mais eficiente, seguro e confiável. A combinação de ferramentas apropriadas e equipe qualificada não só garante medições precisas, mas também melhora a segurança no local de trabalho, a conformidade legal e a reputação da empresa. Ao seguir essas diretrizes e assegurar que as ferramentas necessárias estejam sempre disponíveis e em perfeita condição, as organizações podem otimizar seus processos de calibração e aprimorar a qualidade de suas operações.
Cuidados e manutenções pós-calibração
A calibração de manômetros é uma etapa crucial para garantir medições precisas e confiáveis nos processos industriais e laboratoriais. No entanto, a calibração por si só não é o fim da jornada; os cuidados e manutenções pós-calibração são igualmente importantes. Essa fase envolve práticas que asseguram que os manômetros permaneçam em boas condições de funcionamento e que as medições continuem a ser precisas ao longo do tempo. Todos os cuidados necessários após a calibração devem ser cuidadosamente planejados e executados. A seguir, discutiremos os cuidados e manutenção que devem ser realizados após a calibração de manômetros.
1. Documentação das Calibrações
Uma vez concluído o processo de calibração, é fundamental documentar todos os detalhes do procedimento realizado. Isso inclui registrar a data da calibração, os resultados obtidos, as condições ambientais durante a calibração, os instrumentos utilizados e quaisquer correções aplicadas. A documentação deve ser feita em formulários padronizados de calibração, que podem incluir campos para carimbos de aprovações e assinaturas dos responsáveis. Essa documentação é importante não apenas para auditorias internas, mas também para auditorias externas que possam ser realizadas por órgãos reguladores.
Além disso, a documentação ajuda a manter um histórico dos manômetros, permitindo que tendências sejam observadas e futuras calibrações sejam planejadas. Conservar um registro adequado pode prever a necessidade de manutenção, ajustes ou substituições no futuro, melhorando a eficiência operativa.
2. Inspeção Visual Regular
A manutenção pós-calibração deve incluir inspeções visuais regulares dos manômetros. Isso envolve examinar os instrumentos em busca de sinais de danos, corrosão, vazamentos ou desgastes físicos. Qualquer anomalia identificada deve ser corrigida imediatamente, a fim de evitar problemas mais sérios no futuro.
Durante essas inspeções, cheque se as conexões e juntas estão bem fixadas e se não há vazamentos de fluídos. Uma verificação minuciosa pode ser a chave para prevenir falhas indesejadas no manômetro e prolongar sua vida útil. Além disso, é importante garantir que os manômetros estejam sempre limpos, pois sujeira e contaminantes podem afetar o desempenho e a precisão da medição.
3. Calibrações Regulares
É importante estabelecer um cronograma regular de calibrações para que os manômetros continuem a operar dentro das especificações. Dependendo do uso, muitos manômetros exigem calibrações a cada seis meses ou anualmente. No entanto, o intervalo pode variar com base em fatores como a natureza da aplicação, a frequência de uso e o ambiente operacional. Documentar e monitorar as calibrações anteriores permitirá ajustar esses intervalos com base no histórico de desempenho do manômetro.
As calibrações regulares garantem que qualquer desvio na precisão seja identificado e corrigido antes que possa impactar as operações. Portanto, um cronograma bem definido e respeitado é uma parte essencial dos cuidados pós-calibração.
4. Manejo Adequado durante o Uso
Após a calibração, o manejo adequado dos manômetros deve ser uma prioridade. Operadores e usuários devem ser treinados em como utilizar os instrumentos corretamente, seguindo as diretrizes estabelecidas pela fabricante. Erros de manuseio podem levar a danificações e leituras imprecisas.
Além disso, os manômetros devem ser instalados segundo as orientações do fabricante, garantindo a posição correta e evitando tensões mecânicas que possam comprometer a eficiência do instrumento. As condições ambientais ao redor do manômetro devem ser cuidadosamente monitoradas, evitando exposição a extremos de temperatura, umidade ou produtos químicos que possam causar danos.
5. Armazenamento Adequado
O armazenamento adequado dos manômetros também é uma parte essencial dos cuidados pós-calibração. Quando não estiverem em uso, os manômetros devem ser guardados em ambientes limpos e secos, livres de poeira e contaminantes que possam afetar seu funcionamento. É recomendável usar capas protetoras ou caixas que impeçam a entrada de impurezas e protejam os instrumentos contra impactos e quedas.
O armazenamento em posições estratégicas, evitando locais sujeitos à vibração excessiva ou temperaturas extremas, contribuirá para a preservação da precisão e integridade dos manômetros a longo prazo.
6. Treinamento Contínuo da Equipe
A capacitação dos colaboradores que operam e manutenem os manômetros é fundamental. Os profissionais devem ser instruídos continuamente sobre as melhores práticas de operação, cuidados pós-calibração e procedimentos de segurança. Atividades de treinamento periódico ajudarão a reforçar a importância do procedimento e garantir que todos sigam as diretrizes estabelecidas.
Essa formação continua a promover uma cultura de segurança e qualidade, onde todos os membros da equipe se sentem responsáveis pela manutenção da precisão e confiabilidade dos manômetros, contribuindo para a eficiência geral da operação.
7. Identificação e Resolução de Problemas
Outro aspecto crítico dos cuidados pós-calibração é a identificação e resolução de problemas que possam surgir com os manômetros. Caso um manômetro apresente leituras inconsistentes ou fora do esperado, ele deve ser retirado imediatamente de operação e inspectado. A equipe deve estar capacitada para identificar rapidamente se o problema é decorrente de falha de calibração, desgaste do componente, vazamentos ou necessidade de substituição.
A implementação de um protocolo de solução de problemas pode ajudar a considerar diferentes cenários em que o sistema não está funcionando corretamente, visando a identificação rápida de falhas e tomada de decisão adequada. Não ignore quaisquer sinais de problemas; isso pode prevenir acidentes e salvar tempo e recursos ao evitar que problemas menores se tornem maiores.
8. Manutenção Preventiva
A manutenção preventiva deve ser uma prioridade na gestão dos manômetros. Isso envolve realizar reparos e substituições necessárias antes que um problema sério ocorra. Por meio de inspeções periódicas, a equipe poderá identificar sinais de desgaste ou deterioração e tomar as ações apropriadas.
Estabelecer registros de manutenção facilitará avaliações futuras e permitirá que as empresas identifiquem padrões que possam sugerir a necessidade de uma manutenção mais frequente. A manutenção preventiva ajuda a garantir que o manômetro esteja sempre em condições ideais, minimizando interrupções na produção e mantendo a precisão das medições.
9. Engajamento com os Fabricantes
Os fabricantes dos manômetros muitas vezes oferecem suporte contínuo e recomendações para a calibração, manutenção e operação dos dispositivos. Engajar-se com os fabricantes pode ajudar a obter informações valiosas sobre as melhores práticas e modelos de calibração que podem ser adotados. Além disso, aproveitar a assistência técnica, quando necessário, pode ajudar a resolver problemas ou quando a calibração não produzir resultados via métodos padrão.
Consultar as diretrizes e manuais dos fabricantes é uma maneira de assegurar que as práticas adotadas estejam alinhadas com as recomendações e garantam a durabilidade dos instrumentos.
10. Revisão Contínua dos Procedimentos
Os cuidados e manutenções pós-calibração devem ser revisados continuamente para garantir que estejam atualizados e em conformidade com os padrões da indústria. As circunstâncias e as necessidades operacionais podem mudar, e as práticas que uma vez foram adequadas podem deixar de ser eficazes. Assim, é aconselhável criar um ciclo de revisão regular onde as práticas de calibração e manutenção sejam avaliadas e ajustadas conforme necessário.
Esse processo de revisão não só melhora a eficiência do sistema de calibração, mas, também, alinha os procedimentos com as melhores práticas do setor. Esta abordagem proativa melhora a segurança e a qualidade das medições e atividades associadas.
Conclusão
Cuidar e manter os manômetros de forma adequada após a calibração é essencial para garantir que continuem a operar com precisão e eficiência. Desde a documentação meticulosa até a manutenção preventiva e ao engajamento com os fabricantes, cada passo desempenha um papel integral na preservação da integridade dos instrumentos de medição.
Um compromisso com práticas robustas de pós-calibração não só melhora a confiabilidade das medições, mas também contribui para a segurança operacional, a economia de recursos e a longevidade do equipamento. Adotar uma abordagem consciente e proativa aos cuidados pós-calibração, garantirá que as medições fiquem sempre dentro dos parâmetros desejados e sejam um suporte sólido nos processos industriais.
Em conclusão, o procedimento de calibração de manômetros é um aspecto crucial para a operação eficiente e segura em diversos setores. A precisão nas medições de pressão não apenas assegura a qualidade dos produtos e serviços, mas também protege a segurança dos processos e a integridade dos equipamentos. Ao longo deste artigo, discutimos a importância da calibração, as etapas necessárias para realizá-la corretamente, as ferramentas indispensáveis e os cuidados que devem ser tomados após a calibração. Implementar essas práticas ajudará a garantir que seus manômetros funcionem com a máxima eficiência, evitando falhas e problemas que podem comprometer a qualidade do trabalho. Portanto, adote uma abordagem proativa em relação à calibração e manutenção de seus instrumentos, e assegure a excelência na operação de sua empresa.