Calibração de Instrumentos Industriais: Importância e Métodos
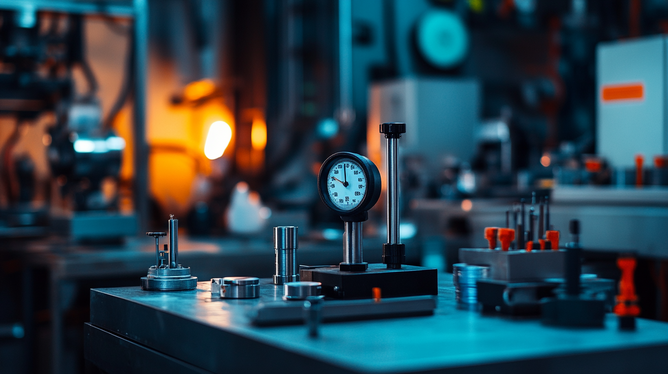
Por: Anderson - 21 de Dezembro de 2024
Calibração de instrumentos industriais é um processo crucial que assegura a precisão e a confiabilidade dos equipamentos utilizados nas mais diversas indústrias. Neste artigo, iremos explorar a importância da calibração, os métodos mais comuns utilizados para realizá-la e os fatores que podem afetar esse processo. Além disso, também abordaremos a necessidade de manutenção e verificação regular dos instrumentos, garantindo assim a qualidade e a eficiência operacional. Continue lendo para entender como a calibração pode impactar sua produção.
Importância da Calibração de Instrumentos Industriais
A calibração de instrumentos industriais é um aspecto vital da operação de equipamentos em diversos setores, tais como farmacêutico, petroquímico, alimentício e de manufatura. Este processo visa garantir que os instrumentos de medição estejam operando com precisão, o que é essencial para a qualidade do produto final e a segurança das operações. A calibração adequada não só cumpre requisitos normativos, mas também contribui significativamente para a eficiência e a confiabilidade dos processos industriais.
Um dos principais benefícios da calibração de instrumentos é a redução de erros de medição. Dispositivos imprecisos podem levar a ajustes inadequados nas operações, resultando em desperdício de material, produtos defeituosos e, em última análise, custos adicionais. Ao calibrar regularmente os instrumentos, as empresas podem minimizar esses riscos e garantir que os dados coletados sejam confiáveis e representativos da realidade.
Além disso, a calibração é fundamental para manter a conformidade com as normas e regulamentações da indústria. Muitos setores são regidos por normas rígidas que exigem a calibração regular de equipamentos. Por exemplo, laboratórios e fábricas que lidam com produtos químicos ou farmacêuticos devem operar dentro de padrões específicos para garantir a segurança e a eficácia dos produtos. A não conformidade pode resultar em multas substanciais, recall de produtos e até mesmo ações legais. Portanto, assegurar que os instrumentos estejam sempre calibrados ajuda a mitigar esses riscos legais.
Outro aspecto importante da calibração é a melhoria da eficiência operacional. Instrumentos calibrados corretamente podem operar com mais eficiência, uma vez que produzem medições mais precisas. Isso significa que os operadores podem fazer ajustes em tempo real com base em dados precisos, melhorando a resposta a variações no processo e otimizando o uso de recursos. Isso não apenas melhora a produtividade, mas também pode resultar em uma redução significativa nos custos operacionais.
A calibração também desempenha um papel crucial na proteção e na vida útil dos equipamentos. Instrumentos que não estão calibrados corretamente podem sofrer desgaste excessivo devido a operações inadequadas. Por exemplo, um medidor de pressão que não está calibrado pode causar sobrecarga em uma válvula, levando a falhas prematuras e, por conseguinte, a custos de manutenção elevados e tempos de inatividade não planejados. Com a calibração regular, as empresas podem prolongar a vida útil de seus equipamentos e reduzir os gastos com manutenção.
Do ponto de vista da qualidade do produto, a calibração é essencial para garantir que os produtos atendam a especificações rigorosas. Em setores como o alimentício, onde a segurança e a qualidade são críticas, qualquer variação nas medições pode levar a consequências sérias. A calibração assegura que todos os parâmetros de produção, como temperatura, pressão e composição química, estejam dentro dos limites especificados. Isso não só garante produtos de alta qualidade, mas também fortalece a confiança dos consumidores na marca.
Além disso, a calibração ajuda a criar um ambiente de trabalho seguro. Equipamentos mal calibrados podem causar acidentes graves, colocando em risco a segurança dos operadores e do ambiente de trabalho. Por exemplo, sensores de temperatura mal calibrados em um reator químico podem não detectar um superaquecimento, potencialmente levando a um acidente. A calibração regular e sistemática é, portanto, uma medida preventiva essencial para garantir a segurança no local de trabalho.
As empresas também podem se beneficiar do uso de tecnologias modernas na calibração. Com a evolução das tecnologias de automação, agora é possível integrar sistemas de calibração em operações industriais. Muitos dispositivos modernos vêm com capacidades de auto-calibração, o que simplifica o processo e reduz a necessidade de intervenção manual. Além disso, a utilização de software para monitoramento e registro de calibrações assegura um histórico detalhado, facilitando auditorias e o cumprimento de regulamentações.
Para garantir que a calibração de instrumentos industriais seja eficaz, é vital que o processo seja realizado de forma sistemática e programada. Isso inclui a definição de intervalos regulares de calibração, que podem variar dependendo do tipo de instrumento, das condições operacionais e das recomendações do fabricante. Muitas empresas optam por criar um cronograma de calibração que seja parte integrante do seu sistema de gestão da qualidade, garantindo que os equipamentos sejam revisados regularmente e mantidos em conformidade.
Além disso, o treinamento adequado dos operadores e da equipe de manutenção é essencial para o sucesso da calibração. Os profissionais devem compreender a importância do processo, as metodologias corretas e como interpretar os resultados das calibrações. Isso ajudará a criar uma cultura de qualidade dentro da organização, onde todos os funcionários entendem seu papel na manutenção da precisão e segurança dos instrumentos.
Por último, é importante destacar que a calibração não é um processo único, mas sim um ciclo contínuo. À medida que os instrumentos são usados, eles podem sofrer desgastes e variações, o que afetará sua precisão. Assim, a calibração deve ser vista como uma prática regular e contínua, que deve ser mantida ao longo da vida útil do equipamento. Com a implementação de um programa de calibração robusto, as empresas não só garantirão a precisão de suas medições, mas também melhorarão a eficiência e a segurança de suas operações.
Em resumo, a calibração de instrumentos industriais é uma prática essencial que afeta todos os aspectos da operação de uma empresa. Desde a qualidade do produto até a eficiência e a segurança, todos se beneficiam de medições precisas e confiáveis. Não deve ser subestimada, pois sua importância se reflete diretamente nos resultados financeiros e na reputação da empresa no mercado. Portanto, investir em calibração é investir no sucesso a longo prazo do negócio.
Métodos Comuns de Calibração
A calibração de instrumentos industriais é um processo crucial que garante a precisão e a confiabilidade dos equipamentos utilizados na produção. Para atingir esses objetivos, existem vários métodos de calibração que podem ser empregados, dependendo do tipo de instrumento, das especificações do fabricante e dos requisitos normativos. Neste artigo, vamos explorar alguns dos métodos mais comuns de calibração, suas aplicações e as melhores práticas associadas a cada um deles.
Um dos métodos mais tradicionais de calibração é o método de comparação. Esse método envolve a comparação das medições do instrumento a ser calibrado com um instrumento padrão de referência, que possui uma precisão conhecida. O instrumento de referência deve ser indiscutivelmente mais preciso e deve ter sido calibrado recentemente. Aí, as medições são realizadas em várias faixas, e qualquer desvio é registrado. Esse método é amplamente utilizado para a calibração de instrumentos de medição de temperatura, pressão e vazão. A vantagem desse método é que ele é relativamente simples e pode ser realizado em campo ou no laboratório.
Outro método significativo é a calibração por ajuste. Nesse caso, o instrumento é ajustado até que as medições correspondam às medidas do padrão de referência. Esse método é mais comum em instrumentos que possuem mecanismos de ajuste incorporados, como manômetros e termômetros. É importante, contudo, que o ajuste seja feito por profissionais treinados, para garantir que as mudanças feitas não comprometam a inteireza ou desempenho do equipamento. A calibração por ajuste é uma prática que não só assegura a precisão mas pode ser parte do uso cotidiano do equipamento em ambientes industriais.
O método de zero e span é uma técnica muito utilizada para calibração de instrumentos analógicos e digitais. Neste método, o operador ajusta o ponto zero do instrumento (o pontinho que representa nenhuma leitura) e, em seguida, define o span (a faixa entre o valor mínimo e máximo que o instrumento pode medir). Por exemplo, em um termômetro, isso poderia significar calibrar a temperatura de 0°C (água congelada) e 100°C (água fervente). Esse método é bastante eficaz para garantir que o instrumento opere corretamente ao longo de toda a sua faixa medida. A calibração de zero e span é especialmente importante em ambientes onde precisão extrema é crucial, como na indústria farmacêutica e alimentícia.
O método de calibração por transferência é outro procedimento útil, especialmente quando os instrumentos não podem ser retirados do local de operação. Nesse método, um instrumento de referência é utilizado em conjunto com o instrumento a ser calibrado da seguinte forma: o instrumento de referência é usado para medir a variável no sistema, e essas medições são usadas para ajustar as leituras do instrumento sob teste. Este método é extremamente útil em cenários onde a interrupção dos processos de produção deve ser minimizada, permitindo que as medições sejam realizadas com precisão sem a necessidade de desconectar o instrumento do sistema operacional.
O método de calibração automática é uma tendência crescente na indústria moderna, principalmente devido à evolução das tecnologias de automação. Muitos instrumentos modernos vêm equipados com recursos de auto-calibração, onde o próprio instrumento pode se comparar a padrões internos ou externos e ajustar automaticamente as medições conforme necessário. Essa abordagem é particularmente benéfica em ambientes altamente controlados, onde a manutenção contínua de precisão é essencial, e pode reduzir significativamente a carga de trabalho do pessoal de manutenção.
A calibração por meio de simulação é um método amplamente utilizado especialmente em instrumentos que não podem ser calibrados diretamente em condições normais. Esse método envolve a criação de condições de medição que simulam a operação do instrumento em diferentes cenários. Por exemplo, um sensor de pressão pode ser calibrado simulando diferentes níveis de pressão em um ambiente de teste controlado. Essa abordagem não só proporciona medições seguras, mas também garante a eficácia do instrumento sob condições operacionais reais.
É igualmente importante considerar a calibração por meio de medições de referência. Esse método envolve a utilização de padrões de referência que possuem um nível de precisão conhecida e verificada. Os padrões podem ser equipamentos certificados ou referência de medição de massa, como pesos de calibração que são usados para verificar balanças industriais. É vital que estes padrões sejam mantidos em condições ideais e calibrados regularmente, já que a precisão do instrumento em teste depende da precisão do padrão de referência.
Quando se trata de equipamentos eletrônicos, a calibração do sistema de controle é uma abordagem comumente utilizada. Essa técnica é frequentemente aplicada a equipamentos de medição complexos que envolvem vários sensores e atuadores interligados em um sistema de controle. A calibração do sistema envolve ajustes não apenas nos sensores individualmente, mas também em como eles interagem dentro do sistema como um todo. Isso pode envolver simulações computadorizadas e ajustes finos das entradas e saídas do sistema até que ele atinja níveis desejáveis de precisão e eficiência.
Adicionalmente, as melhores práticas de calibração devem sempre considerar as recomendações do fabricante, que muitas vezes incluem informações sobre a frequência ideal de calibração e métodos preferidos. A documentação completa do processo de calibração é essencial, uma vez que fornece um histórico que pode ser útil para auditorias e verificações de conformidade. A manutenção de registros claros e organizados também ajuda na identificação de padrões que podem emergir ao longo do tempo, como uma freqüência anormal de desvios em certos instrumentos.
A escolha do método de calibração mais adequado depende das particularidades de cada instrumento e do ambiente em que ele opera. Fatores como a complexidade do instrumento, as condições de operação e os requisitos regulatórios podem influenciar na escolha do método. Por isso, é aconselhável que as empresas realizem uma análise detalhada de suas necessidades e consultem especialistas sempre que necessário.
Vale ressaltar que a calibração não deve ser realizada apenas quando surgem problemas. Em vez disso, deve ser uma parte integral do ciclo de vida do instrumento, o que inclui planejamento correto, execução e verificação. Isso não só assegura a precisão das medições ao longo do tempo, mas também ajuda a construir uma cultura de qualidade e melhoria contínua dentro da organização.
Em resumo, os métodos de calibração são variados e desempenham um papel crítico na precisão operacional de todos os instrumentos industriais. Desde a calibração por comparação até as técnicas mais modernas como auto-calibração, cada método tem seu lugar e utilização dependendo das especificidades do equipamento e do ambiente de operação. Investir em calibração regular e correta é crucial para assegurar o funcionamento eficaz dos instrumentos industriais e, por consequência, o sucesso das operações empresariais como um todo.
Fatores que Afetam a Calibração
A calibração de instrumentos industriais é um processo crítico que garante a precisão e confiabilidade na medição de variáveis físicas. No entanto, diversos fatores podem afetar a eficácia deste processo e a qualidade das medições resultantes. Identificar e compreender esses fatores é essencial para garantir que os instrumentos operem de maneira eficiente e eficaz ao longo de sua vida útil. Neste artigo, exploraremos os principais fatores que podem influenciar a calibragem de instrumentos industriais.
Um dos fatores mais significativos que impacta a calibração é a temperatura. A variação de temperatura pode afetar não apenas o próprio instrumento, mas também os padrões de referência utilizados na calibração. Instrumentos que não são projetados para operar em suas faixas de temperatura específicas podem apresentar desvios nos dados medidos, o que compromete a precisão. Por exemplo, termômetros e sensores de temperatura geralmente têm especificações que delimitam a faixa de temperatura em que operam com precisão. As propriedades físicas dos materiais e componentes também podem mudar com as variações de temperatura, afetando diretamente as medições realizadas. Portanto, é essencial monitorar as condições de temperatura e garantir que a calibração seja feita em condições controladas.
A umidade é outro fator que pode impactar de forma significativa as medições. Muitos instrumentos, especialmente os que envolvem componentes eletrônicos ou mecânicos sensíveis, podem apresentar falhas ou desvios em ambientes com alta umidade. A umidade pode causar corrosão e deterioração em partes do instrumento, levando a leituras imprecisas. Além disso, em processos onde a umidade é uma variável a ser medida, como na indústria alimentícia ou farmacêutica, um sensor mal calibrado em condições de alta umidade pode afetar seriamente a qualidade do produto final. Para minimizar influências adversas, é fundamental considerar a calibração em ambientes controlados, onde a umidade é mantida dentro de limites adequados.
O vibração é outro fator a ser considerado cuidadosamente. Ambientes industriais frequentemente apresentam níveis elevados de vibração, resultado de maquinário em funcionamento ou movimentações. As vibrações podem causar desassociamento em componentes sensíveis e alterar as características de medição de instrumentos. Por exemplo, manômetros e sensores de pressão podem apresentar erros ao serem submetidos a vibrações excessivas, o que pode levar à coleta de dados imprecisos. Portanto, é aconselhável que os instrumentos sejam instalados em locais que minimizem a exposição a vibrações, sempre que possível, e que a calibração seja realizada em condições de operação ideais.
Além disso, a durabilidade dos componentes dos instrumentos também influencia na calibração. Com o tempo e o uso, os componentes dos instrumentos tendem a se desgastar, afetando sua precisão e confiabilidade. Isso é particularmente relevante em instrumentos que operam sob cargas pesadas ou em condições extremas, onde os estresses físicos podem acelerar o desgaste. O desgaste pode resultar em medições incorretas e a calibração pode não ser suficiente para corrigir esses desvios a menos que a manutenção adequada dos equipamentos seja realizada regularmente. Por isso, é importante seguir as recomendações do fabricante sobre os intervalos de calibração, manutenção e substituição de peças.
O tipo de instrumento e sua tecnologia também afetam a calibração. Diferentes instrumentos têm abordagens e metodologias específicas para calibração. Por exemplo, instrumentos digitais podem exigir procedimentos de calibração diferentes dos analógicos. Além disso, a introdução de novas tecnologias e métodos de medição pode alterar as práticas tradicionais de calibração. À medida que novos instrumentos com condições de medição mais rigorosas são desenvolvidos, é essencial que as práticas de calibração sejam adaptadas para acomodar essas inovações. O uso de tecnologias avançadas como conectividade em nuvem e sensores inteligentes pode influenciar a maneira como as medições são feitas e as calibrações são realizadas.
A qualidade dos padrões de referência utilizados na calibração é igualmente crucial. Para garantir a precisão das medições, é fundamental que os instrumentos de referência tenham uma precisão maior que o instrumento que está sendo calibrado. Além disso, os padrões de referência devem ser caracterizados e rastreáveis a padrões reconhecidos em nível nacional ou internacional, como os estabelecidos pelo Sistema Internacional de Unidades (SI). No caso de um padrão de referência com um erro conhecido, a calibração do instrumento pode ser afetada, levando a resultados imprecisos. As empresas devem manter um rigoroso programa de calibração de seus padrões de referência para assegurar que a qualidade das medições seja mantida.
A experiência e habilidade do técnico de calibração que executa o processo também é um fator determinante. A calibração eficaz requer um conhecimento especializado sobre os instrumentos, métodos de calibragem e operação em ambiente industrial. Técnicos mal treinados podem cometer erros no processo de calibração ou interpretar incorretamente os resultados, resultando em medições imprecisas. Assim, investir em treinamento e desenvolvimento contínuo dos profissionais envolvidos na calibração é uma prática que não deve ser negligenciada. Isso assegura que a calibração seja realizada de acordo com as melhores práticas e normas da indústria.
A disposição e organização do ambiente de trabalho onde a calibração ocorre também afetam diretamente a qualidade do processo. Um ambiente desordenado pode levar a distrações e erros durante a calibração. Por exemplo, a falta de ferramentas adequadas ou a presença de interferências podem impactar nas medições e resultados. Um espaço de trabalho limpo e organizado com acesso fácil a todos os equipamentos necessários pode minimizar a probabilidade de erros. Além disso, práticas de gerenciamento de qualidade e segurança são fundamentais para garantir que todas as etapas do processo de calibração sejam seguidas e documentadas de forma adequada.
Outro elemento a considerar é a frequência da calibração. Instrumentos que são usados com mais frequência ou em condições mais exigentes geralmente necessitam de calibrações mais regulares. Assim, a frequência de calibração deve ser adaptada às condições e ao uso de cada instrumento. A negligência em calibrações regulares pode resultar no acúmulo de desvios nas medições, o que compromete os processos. Portanto, as empresas devem estabelecer um cronograma de calibração que esteja alinhado às características de uso e requisitos normativos de seus instrumentos.
Por fim, a integração de sistemas de gerenciamento da qualidade e calibração é fundamental para assegurar que todos os fatores mencionados acima sejam considerados de forma sistemática. Um programa abrangente de gerenciamento da qualidade deve ir além da calibração, já que envolve a documentação, auditoria e revisão contínua dos processos. Isso garante que todos os fatores que possam influenciar a calibração sejam monitorados e gerenciados adequadamente. A integração de informações das medições e calibrações em um sistema de gerenciamento eletrônico ou em nuvem pode facilitar o acompanhamento e o controle da qualidade.
Em resumo, há uma ampla gama de fatores que podem afetar a calibração de instrumentos industriais, desde condições ambientais a treinamento de pessoal. Compreender e controlar esses fatores é essencial para garantir a precisão e confiabilidade dos instrumentos. Ao implementar processos rigorosos de calibração, bem como um programa de manutenção preventiva e um ambiente de trabalho adequado, as empresas podem garantir que seus instrumentos operem de maneira eficiente e eficaz. Isso não apenas leva a medições mais precisas, mas também resulta em maior segurança, qualidade do produto e eficiência operacional.
Manutenção e Verificação Regular dos Instrumentos
A manutenção e verificação regular de instrumentos industriais são etapas cruciais para garantir a precisão, confiabilidade e longevidade dos equipamentos utilizados em diversos setores da indústria. Instrumentos calibrados e bem mantidos não apenas asseguram a qualidade do produto final, mas também contribuem para a segurança operacional e a eficiência dos processos. Neste artigo, vamos explorar a importância da manutenção e verificação regular, as melhores práticas e as estratégias que podem ser adotadas para um gerenciamento eficaz desses instrumentos.
Para iniciar, é fundamental entender que a manutenção implica em um conjunto de ações realizadas para preservar o bom funcionamento dos instrumentos. Isso inclui inspeções regulares, limpeza, ajustes e reparos. Já a verificação refere-se a processos mais formais que garantem que os instrumentos ainda estão operando dentro de especificações estabelecidas, geralmente por meio de calibrações periódicas. Essa combinação é essencial, pois um instrumento que não é mantido adequadamente pode falhar ou apresentar medições imprecisas, independentemente da sua calibragem.
A manutenção preventiva é uma abordagem estratégica que busca evitar falhas e prolongar a vida útil dos instrumentos. Diferente da manutenção corretiva, que ocorre após a identificação de um problema, a manutenção preventiva é planejada e programada. Isso pode incluir a realização de verificações periódicas, substituição de peças desgastadas e testes de desempenho. Ao implementar um programa de manutenção preventiva, as empresas podem reduzir o risco de falhas inesperadas e garantir que os instrumentos estejam sempre prontos para operação. Por exemplo, filtros em sensores de fluxo devem ser limpos ou substituídos periodicamente para evitar obstruções que comprometem a leitura de medições.
Além disso, a manutenção corretiva também tem seu papel. Apesar de não ser ideal, situações podem surgir onde instrumentos falham e a manutenção corretiva se torna necessária. Isso envolve a identificação do problema, diagnóstico, reparo e, eventualmente, recertificação do instrumento. É vital que esse processo seja documentado, para que haja um histórico das intervenções realizadas. Isso não apenas ajuda na identificação de padrões de falha, mas também oferece garantias para auditorias e conformidade regulatória.
Outro elemento importante na manutenção de instrumentos industriais é a limpeza. Muitas vezes, a sujeira, poeira e resíduos podem acumular-se nos instrumentos, afetando a precisão das leituras. Manter os instrumentos limpos é uma prática simples, mas de grande impacto, que pode prevenir problemas maiores. A limpeza deve ser feita com cuidado, respeitando os materiais e especificações recomendados pelos fabricantes, evitando assim o risco de danos.
Quando falamos sobre verificação, um dos pontos mais críticos é a calibração regular. A calibração deve ser feita com a frequência recomendada pelo fabricante e de acordo com os padrões da indústria. Um cronograma deve ser estabelecido, levando em consideração a natureza do instrumento, a frequência de utilização e as condições operacionais. Ferramentas como software de gerenciamento de manutenção podem ser úteis na programação e no rastreamento da calibração e verificação. A calibração deve ser vista como parte integrante do ciclo de vida do instrumento e não apenas uma atividade pontual. Além disso, é importante registrar todos os resultados de calibração e verificações realizadas para garantir a rastreabilidade e a conformidade.
O treinamento da equipe que opera e mantém os instrumentos é outro aspecto essencial. Profissionais capacitados são mais propensos a identificar e corrigir problemas de forma eficaz. Isso inclui compreender os manuais dos instrumentos, as práticas recomendadas para manutenção e calibração, e as normas de segurança necessárias ao operar equipamentos sensíveis. Investir em capacitação regular não só melhora a eficiência operacional, mas também ajuda a garantir que os instrumentos sejam utilizados e mantidos da melhor maneira possível.
Outro aspecto importante é a localização dos instrumentos. É essencial que os instrumentos sejam instalados em locais adequados, onde estarão protegidos de vibrações excessivas, temperaturas extremas, alta umidade e outros fatores que possam impactar seu desempenho. Instalações em ambientes controlados, como salas climatizadas ou áreas com filtragem de ar, podem ajudar a prolongar a vida útil dos equipamentos e reduzir a necessidade de manutenção frequente.
A documentação é vital na manutenção e verificação dos instrumentos. Manter um registro detalhado de todas as atividades de manutenção, calibrações e verificações realizadas proporciona uma visão clara das condições e desempenho dos instrumentos ao longo do tempo. Isso também ajuda a identificar tendências ou padrões que podem indicar a necessidade de maior atenção em certos equipamentos. Além disso, a documentação é imprescindível para auditorias internas e externas e para a conformidade com regulamentações da indústria. Registros organizados e acessíveis facilitam a condução de auditorias e melhoram a comunicação entre as equipes de manutenção e operações.
Integração de tecnologias modernas, como o uso de sistemas de monitoramento remoto, em muitos casos, também pode beneficiar a manutenção e verificação dos instrumentos. Esses sistemas podem oferecer dados em tempo real sobre o desempenho e o estado dos instrumentos, permitindo que as equipes identifiquem rapidamente qualquer anomalia e tomem medidas proativas. Isso pode incluir sensores conectados que alertam sobre desvios de desempenho ou condições operacionais fora dos parâmetros normais, resultando em intervenções mais ágeis e eficazes, antes que problemas sérios se desenvolvam.
Além disso, as empresas devem priorizar a análise de falhas para entender as causas raiz de problemas com instrumentos. Sempre que ocorrer uma falha, deve-se realizar uma análise detalhada para identificar as causas e desenvolver estratégias para evitar que essas situações se repitam no futuro. Isso pode envolver a revisão dos procedimentos de operação e manutenção, bem como a atualização das práticas ou tecnologias utilizadas.
A cultura de qualidade dentro da organização também desempenha um papel fundamental na eficácia da manutenção e verificação regularmente. Cultivar um ambiente onde todos os colaboradores compreendam a importância da precisão das medições e da manutenção dos instrumentos ajudará a aumentar o comprometimento da equipe em seguir práticas adequadas. Os líderes devem promover a conscientização sobre a importância dos instrumentos calibrados e mantidos, destacando como isso impacta diretamente a qualidade do produto final e a eficiência operacional.
Como resultado de todas essas boas práticas, a implementação de um adequado programa de manutenção e verificação regular permite não apenas a melhor performance dos instrumentos, mas também a segurança no ambiente de trabalho. Minimizar falhas e desperdícios tem impacto significativo nas operações e pode resultar na redução de custos, melhoria de qualidade e, por fim, aumento da satisfação do cliente.
Em suma, a manutenção e verificação regular de instrumentos industriais são componentes essenciais de um sistema de gestão da qualidade eficaz. Com um enfoque proativo e práticas rigorosas, as empresas podem garantir que seus instrumentos permaneçam precisos e confiáveis, contribuindo para a eficiência e segurança das operações. Mantenha um compromisso contínuo com a manutenção adequada e a formação de equipes capacitadas, e os resultados positivos surgirão a longo prazo.
Em conclusão, a calibração de instrumentos industriais desempenha um papel vital na garantia da precisão e confiabilidade dos processos produtivos. Ao longo deste artigo, discutimos como a calibração não apenas assegura a qualidade do produto final, mas também contribui para a segurança operacional e eficiência das operações. Compreender os métodos de calibração, os fatores que a influenciam e a importância da manutenção e verificação regular é essencial para qualquer organização que busca otimizar suas operações. Um comprometimento contínuo com a calibração e manutenção não só diminui falhas e desperdícios, mas também fortalece a confiança na medição, resultando em um impacto positivo direto no desempenho e na reputação da empresa no mercado. Por fim, investir em processos de calibração adequados e na capacitação da equipe responsável são passos cruciais para garantir um futuro produtivo e sustentável na indústria.