Calibração de instrumentos de pressão é essencial para a precisão de medições
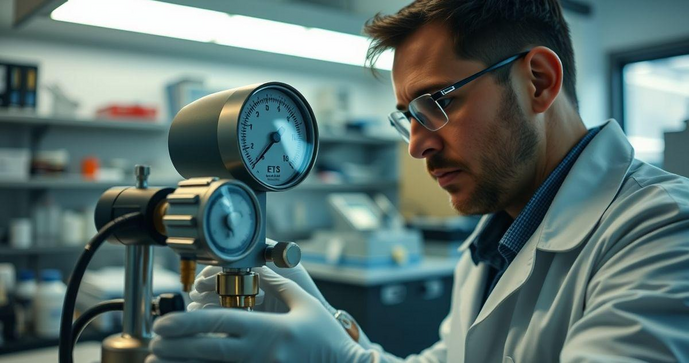
Por: Anderson - 21 de Maio de 2025
Importância da calibração na indústria
A calibração de instrumentos de pressão é uma prática crucial em diversos setores industriais, pois assegura que as medições realizadas estejam dentro dos padrões especificados. Esta precisão é essencial em processos que dependem de medições exatas para a segurança e a qualidade do produto final.
Em indústrias como petroquímica, farmacêutica e alimentícia, por exemplo, a calibração regular de instrumentos é necessária para cumprir normas e regulamentações, garantindo que os produtos sejam seguros para consumo e utilização. Um instrumento desconectado das suas especificações pode resultar em medições impróprias, levando a produtos com qualidade inferior.
Além disso, a calibração play um papel importante na eficiência operacional. Instrumentos imprecisos podem acarretar em desperdícios de materiais, energias e esforços. Por exemplo, um manômetro desalinhado pode gerar pressões excessivas ou insuficientes, afetando máquinas e sistemas produtivos.
Outro fator relevante é a manutenção da confiabilidade das operações. A calibração regular minimiza as chances de falhas em equipamentos e sistemas, resultando em um ambiente de trabalho mais seguro. Medições e controles adequados são vitais para evitar situações perigosas, protegendo não apenas as instalações, mas também os colaboradores presentes.
Por último, a calibração de instrumentos de pressão também pode influenciar na reputação da empresa. Compromissos com a qualidade e segurança se traduzem positivamente para clientes e parceiros, impactando, assim, a competitividade do negócio no mercado.
Equipamentos usados na calibração de pressão
A calibração de instrumentos de pressão requer o uso de equipamentos específicos que garantem a precisão das medições. Entre os mais comuns estão os calibradores manuais e digitais, que oferecem uma alternativa prática e confiável para verificar e ajustar as medições dos instrumentos.
Os calibradores de pressão manuais operam por meio de um sistema de manômetro, onde a pressão é aplicada diretamente ao instrumento a ser verificado. Este tipo de equipamento é ideal para calibrações simples em ambientes de operações menores.
Por outro lado, os calibradores digitais de pressão oferecem maior precisão e facilidade de uso. Eles possuem telas que exibem as medições em tempo real, permitindo ajustes rápidos e eficientes. Muitos modelos digitais também incluem funções de armazenamento de dados, permitindo que as informações de calibração sejam registradas e analisadas posteriormente.
Outro equipamento importante é o comparador de pressão, que permite a verificação de múltiplos instrumentos ao mesmo tempo, garantindo que todos estejam calibrados de acordo com os padrões necessários. Este dispositivo é especialmente útil em ambientes de fábrica onde muitos instrumentos precisam ser monitorados simultaneamente.
Além disso, válvulas e adaptadores são essenciais para conectar os instrumentos de pressão ao sistema de calibração. Esses acessórios garantem que o processo de calibração seja realizado sem vazamentos, mantendo a integridade das medições. É fundamental utilizar adaptadores compatíveis para evitar erros nas leituras.
Procedimentos técnicos para calibração
A calibração de instrumentos de pressão envolve uma série de procedimentos técnicos que garantem a precisão das medições. O primeiro passo é a preparação do instrumento a ser calibrado. É fundamental limpar o dispositivo e verificar se não há danos visíveis que possam comprometer sua operação.
Em seguida, deve-se escolher o equipamento de calibração apropriado, como um calibrador manual ou digital. É essencial que o calibrador tenha uma faixa de medição compatível com o instrumento que está sendo calibrado e que esteja previamente calibrado para garantir sua precisão.
Após conectar o calibrador ao instrumento, o próximo passo é aplicar pressão gradativa. Isso pode ser feito manualmente ou por meio do uso de uma bomba de pressão, dependendo do tipo de equipamento. O procedimento deve ser realizado de forma lenta e controlada, para evitar picos de pressão que possam danificar os instrumentos ou causar medições imprecisas.
Enquanto a pressão é aplicada, devem-se registrar as leituras do instrumento sob calibração e compará-las com as leituras do calibrador. Essa comparação é crucial para identificar desvios e determinar a necessidade de ajustes. Normalmente, se a diferença exceder uma tolerância predefinida, o instrumento precisa ser ajustado ou reparado.
Após registrar os dados de calibração e fazer os ajustes necessários, é importante realizar um teste final. Isso envolve recalibrar o instrumento e verificar novamente as leituras em diferentes níveis de pressão para assegurar que a calibração foi bem-sucedida e que o instrumento agora atende às especificações exigidas.
Normas e regulamentações sobre calibração
As normas e regulamentações sobre calibração de instrumentos de pressão são fundamentais para garantir a consistentência e a confiabilidade das medições em diversos setores.
As principais normas internacionais que orientam a calibração incluem as publicações da International Organization for Standardization (ISO), especialmente a norma ISO/IEC 17025, que especifica os requisitos gerais para a competência de laboratórios de ensaio e calibração.
A ISO 9001 também é uma norma relevante, pois estabelece requisitos para sistemas de gestão da qualidade, incluindo a necessidade de controlos de medição e monitoração. Isso implica que as empresas devem implementar processos sistemáticos para garantir que seus instrumentos estejam sempre calibrados e funcionando de acordo com as especificações.
Além das normas ISO, muitas indústrias possuem regulamentações específicas que ditam os requisitos de calibração. Por exemplo, o setor farmacêutico deve seguir normas rigorosas estabelecidas pela Agência Nacional de Vigilância Sanitária (ANVISA) no Brasil, o que assegura que todos os instrumentos utilizados na produção e controle de qualidade sejam calibrados regularmente para manter a segurança dos produtos.
Em indústrias como a de petróleo e gás, a calibração é regulada por normas da American Petroleum Institute (API), que fornecem diretrizes detalhadas sobre como realizar a calibração e as frequências necessárias de verificação de instrumentos. Essas normas garantem que as medições são precisas, o que é crítico para a segurança operacional.
Por fim, é essencial que as organizações estejam atualizadas sobre as regulamentações pertinentes ao seu setor. Estabelecer um programa de calibração que siga normas reconhecidas e manter registros adequados não apenas ajuda a garantir a conformidade, mas também melhora a qualidade dos produtos e reduz riscos operacionais.
Benefícios da calibração regular
Realizar a calibração regular de instrumentos de pressão traz uma série de benefícios significativos para as operações industriais. Um dos principais benefícios é a melhoria da precisão nas medições, o que resulta em operações mais seguras e eficientes.
Instrumentos calibrados garantem que os dados coletados estejam dentro dos padrões exigidos, evitando erros que poderiam comprometer processos e produtos.
Outra vantagem importante é a redução de custos operacionais. Instrumentos imprecisos podem levar a desperdícios de materiais, retrabalhos e até mesmo danos a equipamentos. Ao garantir que os instrumentos estejam sempre calibrados, as empresas podem minimizar esses custos e promover uma operação mais econômica.
A calibração regular também desempenha um papel crucial na conformidade com normas e regulamentações industriais. Muitos setores exigem que os equipamentos sejam calibrados em intervalos específicos para atender a padrões de qualidade e segurança. Manter a calibração em dia ajuda as empresas a evitarem penalidades e a assegurarem a continuidade de suas operações.
Além disso, a calibração regular contribui para a longevidade dos equipamentos. Instrumentos que são frequentemente calibrados e mantidos em boas condições geralmente têm uma vida útil mais longa, o que reduz a necessidade de substituições frequentes e economiza em investimentos a longo prazo.
Por último, a calibração regular ajuda a fomentar uma cultura de qualidade dentro da organização. Ao fortalecer o compromisso com práticas de manutenção e calibração, as empresas promovem confiança entre seus colaboradores e parceiros, resultando em um ambiente de trabalho mais eficiente e focado na excelência.
Erros comuns na calibração de instrumentos
Durante o processo de calibração de instrumentos de pressão, podem ocorrer diversos erros que comprometem a precisão das medições. Um dos erros mais comuns é a escolha inadequada do equipamento de calibração. Usar um calibrador que não possui a mesma faixa de medição ou especificações compatíveis pode resultar em leituras incorretas e comprometer todo o processo.
Outro erro frequente é a instalação incorreta dos instrumentos. Uma conexão inadequada entre o calibrador e o instrumento a ser verificado pode causar vazamentos que não apenas afetam as medições, mas também podem danificar os dispositivos. É essencial seguir as diretrizes do fabricante para garantir que todas as conexões sejam feitas de forma apropriada e segura.
A falta de preparação adequada antes da calibração também é um erro comum. Não realizar uma limpeza prévia ou não verificar o estado do instrumento pode interferir na precisão das leituras. As partículas de sujeira ou resíduos podem bloquear componentes sensíveis e afetar a performance do instrumento durante o teste.
Erros na aplicação da pressão são outro ponto crítico. A aplicação rápida ou excessiva de pressão pode levar a medições imprecisas e, em casos extremos, danificar os instrumentos. Os técnicos devem sempre aplicar pressão de forma gradual e monitorar as leituras de maneira controlada.
Por fim, uma falha relacionada à documentação pode ser prejudicial. Não registrar as informações de calibração ou não armazenar os dados corretamente impede que a empresa obtenha um histórico confiável do desempenho dos instrumentos. Isso pode dificultar a identificação de padrões de erro e comprometer a qualidade geral do processo de calibração.
A calibração de instrumentos de pressão é uma etapa fundamental para garantir a precisão e a confiabilidade das medições em diversos setores industriais. Através das práticas corretas, incluindo o uso de equipamentos adequados e a adesão a normas e regulamentações, é possível assegurar que os instrumentos estejam sempre funcionando de acordo com os padrões estabelecidos.
Os benefícios associados à calibração regular, como a melhoria na eficiência operacional e a redução de custos, reforçam a necessidade de um rigoroso controle de qualidade. Ao evitar erros comuns e priorizar a manutenção adequada, as empresas não apenas garantem a segurança e a qualidade do seu produto, mas também fortalecem sua reputação no mercado.
Em suma, investir na calibração de instrumentos não é apenas uma questão de cumprimento de normas, mas uma decisão estratégica que pode impactar diretamente o sucesso e a competitividade de uma organização.