Como Escolher o Manômetro Industrial Ideal para Sua Indústria
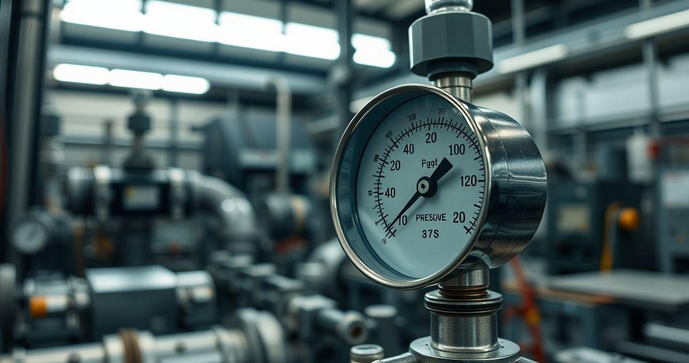
Por: Anderson - 21 de Maio de 2025
Entendendo o Funcionamento do Manômetro Industrial
O manômetro industrial é um instrumento projetado para medir a pressão de gases ou líquidos em sistemas industriais. O funcionamento desse dispositivo é baseado em princípios físicos fundamentais, que permitem uma leitura precisa da pressão em ambientes variados.
Em essência, o manômetro atua convertendo a pressão aplicada em uma força mecânica que é então traduzida em uma leitura de pressão. Existem diferentes tipos de manômetros, sendo os mais comuns os manômetros de tubo em U, manômetros de bourdon e manômetros digitais.
Os manômetros de tubo em U utilizam um tubo curvado em forma de 'U' preenchido com um líquido, normalmente água ou mercúrio. A pressão do fluido provoca uma diferença de altura no líquido, que pode ser medida para determinar a pressão.
Já os manômetros de bourdon utilizam um tubo de forma oval que se expande ou contrai conforme a pressão se altera, fazendo com que um ponteiro marche em uma escala calibrada. Esse tipo é bastante confiável e amplamente utilizado em aplicações industriais.
Por sua vez, os manômetros digitais apresentam sensores eletrônicos que medem a pressão e fornecem os resultados em um display digital. Esses dispositivos são apreciados pela precisão e pela facilidade de leitura, além de geralmente oferecerem funções adicionais, como registro de dados e alarmes.
Compreender como funciona o manômetro industrial é crucial para sua seleção e uso adequados. Ao escolher um manômetro, é essencial avaliar a faixa de pressão que será medida, o tipo de fluido envolvido e as condições ambientais, como temperatura e corrosividade.
Principais Tipos de Manômetros para Indústrias
Existem diversos tipos de manômetros utilizados nas indústrias, cada um projetado para atender a necessidades específicas de medição de pressão. Conhecer as características de cada tipo é fundamental para escolher o modelo mais adequado para sua aplicação.
Os manômetros de tubo em U são um dos modelos mais antigos e simples. Eles consistem em um tubo em forma de 'U', parcialmente preenchido com um líquido. A pressão do fluido a ser medido causa uma diferença no nível do líquido, possibilitando a leitura da pressão pela altura da coluna. Essa opção é muito útil em aplicações de baixa pressão.
Os manômetros de bourdon são bastante populares na indústria. Eles operam através da deformação de um tubo elástico que se curva conforme a pressão aumenta. Essa curvatura movimenta um ponteiro, permitindo a leitura da pressão em uma escala graduada. São ideais para uma ampla gama de pressões e aplicações.
Os manômetros digitais, por sua vez, utilizam sensores eletrônicos para medir a pressão. Esses dispositivos oferecem leituras mais precisas e podem incluir funcionalidades extras, como a gravação de dados e alarmes para situações anormais. São bastante valorizados em ambientes industriais que exigem medições exatas.
Manômetros de diafragma são usados em aplicações que envolvem fluidos corrosivos ou viscosos. Eles possuem um diafragma flexível que se deforma com alterações de pressão, permitindo que medições sejam feitas sem que o fluido entre em contato direto com o mecanismo do manômetro. Esse tipo é crucial para a proteção do instrumento e a segurança do sistema.
Por fim, existem manômetros de pressão absoluta e de pressão manométrica. Os manômetros absolutos medem a pressão em relação ao vácuo, enquanto os manômetros manométricos medem a pressão em relação à pressão atmosférica. A escolha entre esses tipos depende do contexto e das exigências da aplicação específica.
Fatores a Considerar na Escolha do Manômetro
Escolher o manômetro ideal para sua aplicação industrial envolve avaliar uma série de fatores cruciais. A decisão correta pode garantir a precisão, a segurança e a durabilidade do equipamento.
Aqui estão os principais fatores a considerar.
Primeiramente, a faixa de pressão é um aspecto fundamental. É importante selecionar um manômetro que opere adequadamente dentro da faixa de pressão esperada para o seu sistema. Um manômetro com faixa de medição muito ampla pode resultar em leituras imprecisas, enquanto um com faixa insuficiente pode estar sempre operando no limite ou ultrapassando-o, o que pode danificar o instrumento.
Outro fator significativo é o tipo de fluido que será medido. Fluídos corrosivos, abrasivos ou viscosos podem danificar componentes internos do manômetro. Portanto, é essencial escolher um modelo que seja compatível com as propriedades do fluido. Manômetros com diafragmas ou revestimentos específicos podem ser necessários para proteger o instrumento.
As condições ambientais também devem ser consideradas. A temperatura e a presença de vibrações, umidade e poeira podem afetar o desempenho do manômetro. Modelos robustos e resistentes a ambientes adversos podem ser necessários em indústrias pesadas ou em locais de difícil acesso.
A precisão do manômetro é outro ponto crítico. Diferentes tipos de manômetros apresentam graus variados de precisão. Para aplicações que exigem medições exatas, um manômetro digital pode ser a melhor escolha devido à sua capacidade de fornecer leituras mais confiáveis e precisas.
Finalmente, o custo e a manutenção do manômetro devem ser avaliados. Modelos mais sofisticados podem oferecer funções avançadas, mas também exigem investimento inicial maior e podem demandar manutenção especializada. Considerar o custo total de propriedade, incluindo instalação e manutenção, é essencial para fazer uma escolha informada.
Instalação Correta do Manômetro Industrial
A instalação correta do manômetro industrial é crucial para garantir a precisão das medições e o bom funcionamento do sistema. Seguir diretrizes adequadas durante a instalação pode prevenir problemas futuros e aumentar a vida útil do equipamento.
O primeiro passo é escolher o local adequado para a instalação do manômetro. Ele deve ser instalado em uma posição onde seja facilmente acessível para manutenção e leitura. Além disso, deve-se evitar locais com vibrações excessivas ou onde haja nebulização de fluidos corrosivos que possam danificá-lo.
Antes de realizar a instalação, verifique se todas as ferramentas necessárias estão disponíveis, como chaves de fenda, fita de vedação e, se necessário, um adaptador para o tipo de conexão do manômetro. É importante que a conexão seja compatível com o sistema para evitar vazamentos.
Na instalação, certifique-se de seguir as instruções do fabricante. Normalmente, é necessário utilizar uma fita de vedação na rosca do manômetro para garantir que não haja vazamento durante a operação. Um aperto adequado e uniforme das conexões é essencial para criar uma vedação eficaz.
Após a instalação física, é fundamental calibrar o manômetro conforme as especificações do fabricante. Isso geralmente envolve a realização de um teste de pressão para verificar se o manômetro está lendo corretamente. A calibração deve ser feita periodicamente e sempre que a instalação for realizada ou após uma manutenção significativa.
Finalmente, após a instalação e a calibração, realize uma inspeção final no sistema para garantir que não haja vazamentos e que todas as conexões estejam firmes. Monitorar a operação nos primeiros dias pode ajudar a identificar rapidamente quaisquer problemas que possam surgir.
Manutenção e Cuidados Necessários
A manutenção adequada do manômetro industrial é essencial para garantir sua precisão e prolongar sua vida útil. Implementar cuidados regulares ajuda a evitar falhas e a garantir que o equipamento opere com eficiência ao longo do tempo.
Um dos passos mais importantes é realizar limpezas periódicas do manômetro. Poeira, sujeira ou resíduos de líquidos podem afetar as medições e, portanto, é recomendável limpar o dispositivo com um pano macio e seco. Evite o uso de produtos químicos agressivos que possam danificar os componentes do manômetro.
Outra prática recomendada é inspecionar regularmente as conexões e as tubulações associadas ao manômetro. Certifique-se de que estão firmes e que não há sinais de corrosão ou desgaste. Qualquer dano nas conexões pode levar a vazamentos e comprometer a precisão das medições.
A lubrificação das partes móveis, quando aplicável, também é crucial. Consulte o manual do fabricante para identificar quais componentes devem ser lubrificados e com que frequência. Em geral, a lubrificação deve ser feita a cada seis meses, mas pode variar de acordo com o uso e as condições ambientais.
Além disso, é importante verificar a calibração do manômetro em intervalos regulares ou após manutenção significativa. A calibração garante que o instrumento esteja fornecendo medições precisas, o que é fundamental para a segurança e eficiência do sistema.
Por fim, a manutenção deve incluir registros detalhados de todas as inspeções e serviços realizados. Isso ajudará a monitorar a performance do manômetro e a identificar padrões que possam indicar a necessidade de substituição ou reparo antes que problemas maiores ocorram.
Erros Comuns ao Utilizar Manômetros Industriais
Os manômetros industriais são ferramentas essenciais para a medição de pressão, mas seu uso inadequado pode levar a erros graves. Conhecer os erros mais comuns pode ajudar a evitar problemas e garantir medições precisas.
Um dos erros mais frequentes é a instalação incorreta do manômetro. Isso pode incluir o uso de conexões inadequadas, instalação em locais com vibrações excessivas ou não seguir as orientações do fabricante. A instalação inadequada pode resultar em leituras imprecisas e, em casos extremos, danos ao instrumento.
Outro erro comum é ignorar a calibração regular do manômetro. A falta de calibração pode levar a medições erradas, que podem comprometer a segurança do sistema e causar falhas operacionais. É fundamental programar verificações de calibração conforme recomendado pelo fabricante.
A exposição a condições ambientais adversas também pode ser uma fonte de erro. Manômetros que não são projetados para resistir a temperaturas extremas, umidade ou produtos químicos podem apresentar falhas. É importante escolher um manômetro adequado para o ambiente em que será utilizado.
O uso de manômetros com faixas de medição inadequadas é outro erro crítico. Um manômetro que não está na faixa correta de pressão pode dar leituras imprecisas ou falhar completamente ao tentar medir a pressão. Por isso, é essencial verificar a compatibilidade do manômetro com a pressão do sistema.
Por último, a falta de manutenção regular pode causar problemas sérios. A negligência nos cuidados necessários pode levar ao acúmulo de sujeira, desgaste excessivo ou falhas mecânicas. Estabelecer um cronograma de manutenção garante que o manômetro funcione corretamente e que a precisão das medições seja mantida.
A escolha e o uso adequados de manômetros industriais são fundamentais para garantir a precisão e a segurança em diversas aplicações. Compreender o funcionamento, os tipos disponíveis e os fatores a serem considerados na seleção ajuda a otimizar a medição de pressão.
A instalação correta e a manutenção periódica são essenciais para prolongar a vida útil do manômetro e assegurar que ele opere de maneira eficiente. Evitar erros comuns, como a calibração inadequada e a instalação incorreta, é crucial para garantir a confiabilidade do equipamento.
Investir tempo na escolha do manômetro certo e na implementação de práticas de manutenção ajudará a garantir que sua operação industrial continue fluindo sem problemas, aumentando a segurança e a eficácia das operações.