Calibração de Válvula de Segurança: Como Garantir a Segurança e Eficiência do Seu Sistema
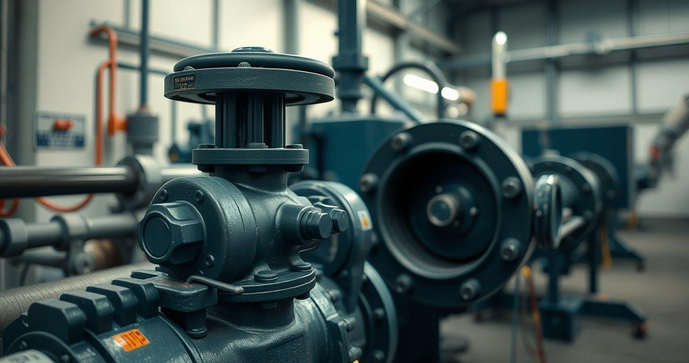
Por: Anderson - 23 de Junho de 2025
A calibração de válvula de segurança é um processo crucial para garantir a eficiência e a segurança em sistemas industriais. Essas válvulas desempenham um papel vital na proteção de equipamentos e na prevenção de acidentes, controlando a pressão e evitando sobrecargas. Neste artigo, abordaremos a importância da calibração, o passo a passo para realizá-la corretamente, os erros comuns a serem evitados e a necessidade de manutenção regular para assegurar o funcionamento adequado das válvulas de segurança.
Importância da Calibração de Válvula de Segurança para a Segurança Operacional
A calibração de válvula de segurança é um aspecto fundamental na operação de sistemas industriais, especialmente em setores que lidam com fluidos pressurizados, como petróleo, gás, química e energia. Essas válvulas são projetadas para proteger equipamentos e instalações contra pressões excessivas, evitando falhas catastróficas que podem resultar em danos materiais, lesões e até mesmo fatalidades. Portanto, a calibração adequada dessas válvulas é essencial para garantir a segurança operacional e a integridade dos processos industriais.
Uma válvula de segurança mal calibrada pode levar a uma série de problemas. Se a válvula não abrir na pressão correta, o sistema pode experimentar uma sobrepressão, resultando em rupturas de tubulações, explosões ou vazamentos perigosos. Por outro lado, se a válvula abrir muito cedo, pode causar perda de produto e eficiência, além de aumentar os custos operacionais. Assim, a calibração precisa é vital para assegurar que a válvula funcione dentro dos parâmetros estabelecidos, garantindo a segurança e a eficiência do sistema.
Além de prevenir acidentes, a calibração regular das válvulas de segurança também é uma exigência normativa em muitos setores. Organizações como a American Society of Mechanical Engineers (ASME) e a Occupational Safety and Health Administration (OSHA) estabelecem diretrizes rigorosas para a manutenção e calibração de válvulas de segurança. O não cumprimento dessas normas pode resultar em penalidades legais, além de comprometer a segurança dos trabalhadores e a operação da planta.
Outro ponto importante a ser considerado é que a calibração de válvulas de segurança não deve ser vista apenas como uma tarefa de manutenção, mas como parte integrante da cultura de segurança de uma organização. Promover uma mentalidade de segurança entre os funcionários, onde a calibração e a manutenção são priorizadas, pode reduzir significativamente o risco de acidentes. Treinamentos regulares e conscientização sobre a importância da calibração ajudam a criar um ambiente de trabalho mais seguro e eficiente.
Além disso, a calibração de válvulas de segurança contribui para a longevidade do equipamento. Válvulas bem calibradas tendem a ter uma vida útil mais longa, pois operam dentro de suas especificações ideais, reduzindo o desgaste e a necessidade de reparos frequentes. Isso não apenas economiza custos com manutenção, mas também minimiza o tempo de inatividade da planta, permitindo que as operações continuem sem interrupções.
É importante ressaltar que a calibração deve ser realizada por profissionais qualificados, que compreendam as especificações técnicas da válvula e as condições de operação do sistema. Esses especialistas devem utilizar equipamentos de calibração adequados e seguir procedimentos estabelecidos para garantir resultados precisos. A falta de conhecimento técnico pode levar a erros que comprometem a segurança e a eficiência do sistema.
Além da calibração, a manutenção regular de outros componentes do sistema, como redutores de velocidade, também é crucial para a segurança operacional. A manutenção de redutor deve ser realizada em conjunto com a calibração das válvulas de segurança, pois esses componentes trabalham em sinergia para garantir o funcionamento adequado do sistema. A falha em um desses elementos pode afetar o desempenho do outro, aumentando o risco de falhas operacionais.
Por fim, a calibração de válvulas de segurança é um investimento que traz retornos significativos em termos de segurança, eficiência e conformidade regulatória. As empresas que priorizam a calibração e a manutenção de suas válvulas de segurança não apenas protegem seus ativos e funcionários, mas também melhoram sua reputação no mercado, demonstrando compromisso com as melhores práticas de segurança. Em um ambiente industrial, onde os riscos são elevados, a calibração adequada das válvulas de segurança é uma responsabilidade que não pode ser negligenciada.
Em resumo, a calibração de válvula de segurança é um elemento essencial para a segurança operacional em ambientes industriais. Ela previne acidentes, garante a conformidade com normas regulatórias, promove uma cultura de segurança e contribui para a longevidade do equipamento. Portanto, é fundamental que as empresas implementem práticas rigorosas de calibração e manutenção, assegurando que suas válvulas de segurança operem de maneira eficaz e segura.
Passo a Passo para Realizar a Calibração de Válvula de Segurança
A calibração de válvulas de segurança é um procedimento crítico que garante a operação segura e eficiente de sistemas industriais. A seguir, apresentamos um guia passo a passo para realizar a calibração de válvulas de segurança, assegurando que elas funcionem dentro dos parâmetros especificados e contribuam para a segurança operacional.
1. Preparação e Planejamento
Antes de iniciar o processo de calibração, é fundamental realizar um planejamento adequado. Isso inclui a revisão da documentação técnica da válvula, como manuais do fabricante e especificações de operação. Além disso, é importante reunir todas as ferramentas e equipamentos necessários, como manômetros, chaves de fenda, chaves inglesas e dispositivos de calibração. Certifique-se de que a área de trabalho esteja limpa e livre de obstruções para garantir um ambiente seguro.
2. Desligamento do Sistema
Antes de realizar qualquer trabalho na válvula de segurança, é essencial desligar o sistema. Isso envolve a interrupção do fornecimento de energia e a despressurização do sistema. Siga os procedimentos de segurança estabelecidos pela sua empresa para garantir que todos os riscos sejam minimizados. A despressurização é uma etapa crítica, pois trabalhar em uma válvula sob pressão pode resultar em acidentes graves.
3. Remoção da Válvula de Segurança
Após despressurizar o sistema, a próxima etapa é remover a válvula de segurança. Utilize as ferramentas apropriadas para soltar os parafusos ou conexões que prendem a válvula ao sistema. Tenha cuidado para não danificar a válvula ou as conexões durante a remoção. Coloque a válvula em uma superfície limpa e estável para facilitar o processo de calibração.
4. Inspeção Visual
Antes de iniciar a calibração, realize uma inspeção visual detalhada da válvula. Verifique se há sinais de desgaste, corrosão ou danos. Componentes danificados devem ser substituídos antes da calibração, pois podem afetar o desempenho da válvula. Além disso, verifique se as partes móveis estão livres de obstruções e se a válvula está em boas condições de funcionamento.
5. Conexão do Equipamento de Calibração
Conecte o equipamento de calibração à válvula de segurança. Isso geralmente envolve a conexão de um manômetro ao orifício de teste da válvula. Certifique-se de que todas as conexões estejam firmes e seguras para evitar vazamentos. O manômetro deve ser calibrado e verificado para garantir a precisão das medições.
6. Ajuste da Pressão de Atuação
Com o equipamento de calibração conectado, inicie o processo de ajuste da pressão de atuação da válvula. Aumente lentamente a pressão do sistema até que a válvula comece a abrir. Observe a pressão no manômetro e registre o ponto em que a válvula se abre. Esse valor deve corresponder à pressão especificada pelo fabricante. Se a pressão de abertura estiver fora dos limites, ajuste a válvula conforme necessário, seguindo as instruções do fabricante.
7. Teste de Funcionamento
Após ajustar a pressão de atuação, é importante realizar um teste de funcionamento. Aumente a pressão novamente até que a válvula se abra e, em seguida, reduza a pressão para verificar se a válvula fecha corretamente. O fechamento deve ocorrer sem vazamentos e de forma suave. Registre os resultados dos testes para referência futura.
8. Reinstalação da Válvula
Depois de concluir a calibração e os testes, a válvula de segurança pode ser reinstalada no sistema. Certifique-se de que todas as conexões estejam firmes e que a válvula esteja posicionada corretamente. Siga os procedimentos de instalação recomendados pelo fabricante para garantir que a válvula funcione adequadamente.
9. Verificação Final e Documentação
Após a reinstalação, é essencial realizar uma verificação final. Ligue o sistema e monitore a válvula de segurança para garantir que ela opere conforme esperado. Documente todos os resultados da calibração, incluindo a pressão de abertura e fechamento, bem como quaisquer ajustes realizados. Essa documentação é importante para auditorias e para garantir a conformidade com as normas de segurança.
10. Manutenção Contínua
A calibração de válvulas de segurança não deve ser um evento isolado. É fundamental implementar um programa de manutenção contínua que inclua verificações regulares e recalibrações conforme necessário. Além disso, a manutenção em redutores e outros componentes do sistema deve ser realizada em conjunto com a calibração das válvulas de segurança, garantindo que todos os elementos do sistema operem de forma sinérgica e segura.
Em resumo, a calibração de válvulas de segurança é um processo crítico que requer atenção aos detalhes e um compromisso com a segurança. Seguir este passo a passo garantirá que as válvulas operem de maneira eficaz, protegendo tanto os equipamentos quanto os trabalhadores. A implementação de práticas rigorosas de calibração e manutenção é essencial para a segurança operacional em ambientes industriais.
Erros Comuns na Calibração de Válvula de Segurança e Como Evitá-los
A calibração de válvulas de segurança é um processo crítico para garantir a segurança e a eficiência em sistemas industriais. No entanto, existem diversos erros que podem ocorrer durante esse procedimento, comprometendo a eficácia da válvula e, consequentemente, a segurança operacional. Neste artigo, abordaremos os erros mais comuns na calibração de válvulas de segurança e como evitá-los, assegurando que o processo seja realizado de maneira correta e eficaz.
1. Falta de Preparação Adequada
Um dos erros mais frequentes na calibração de válvulas de segurança é a falta de preparação adequada. Isso inclui não revisar a documentação técnica da válvula, não reunir as ferramentas necessárias ou não realizar uma inspeção visual prévia. Para evitar esse erro, é fundamental dedicar tempo ao planejamento. Revise os manuais do fabricante, verifique se todas as ferramentas estão disponíveis e faça uma inspeção visual da válvula antes de iniciar o processo de calibração. Essa preparação pode evitar problemas durante a calibração e garantir que o procedimento seja realizado de forma eficiente.
2. Ignorar a Despressurização do Sistema
Outro erro comum é não despressurizar o sistema antes de trabalhar na válvula de segurança. Trabalhar em uma válvula sob pressão pode resultar em acidentes graves, como vazamentos ou explosões. Para evitar esse erro, sempre siga os procedimentos de segurança estabelecidos pela sua empresa. Certifique-se de que o sistema esteja completamente despressurizado e que todas as fontes de energia estejam desligadas antes de iniciar a calibração.
3. Uso de Equipamentos de Calibração Inadequados
Utilizar equipamentos de calibração inadequados ou não calibrados é um erro que pode comprometer a precisão da calibração da válvula de segurança. Manômetros e outros dispositivos de medição devem ser verificados regularmente para garantir que estão funcionando corretamente. Para evitar esse problema, utilize sempre equipamentos de calibração de alta qualidade e verifique se estão calibrados antes de cada uso. Um termômetro industrial digital é um exemplo de equipamento que deve ser mantido em boas condições para garantir medições precisas.
4. Não Realizar Testes de Funcionamento
Após a calibração, é essencial realizar testes de funcionamento para garantir que a válvula opere corretamente. Ignorar essa etapa pode resultar em falhas operacionais e riscos à segurança. Para evitar esse erro, sempre teste a válvula após a calibração, verificando se ela abre e fecha nas pressões corretas e se não há vazamentos. Documente os resultados dos testes para referência futura e para garantir a conformidade com as normas de segurança.
5. Falta de Documentação
A documentação adequada é crucial para a calibração de válvulas de segurança. A falta de registros pode dificultar a identificação de problemas futuros e comprometer a conformidade com as normas regulatórias. Para evitar esse erro, mantenha registros detalhados de todas as calibrações realizadas, incluindo as pressões de abertura e fechamento, os ajustes feitos e os resultados dos testes. Essa documentação é importante para auditorias e para garantir a segurança operacional.
6. Não Treinar a Equipe Adequadamente
A calibração de válvulas de segurança deve ser realizada por profissionais qualificados e treinados. A falta de conhecimento técnico pode levar a erros graves durante o processo. Para evitar esse problema, invista em treinamentos regulares para a equipe responsável pela calibração. Isso garantirá que todos os envolvidos compreendam os procedimentos corretos e as melhores práticas, minimizando o risco de erros.
7. Ignorar as Condições Ambientais
As condições ambientais podem afetar o desempenho das válvulas de segurança e, consequentemente, a calibração. Ignorar fatores como temperatura, umidade e vibrações pode resultar em medições imprecisas. Para evitar esse erro, considere as condições ambientais ao realizar a calibração. Se necessário, ajuste os parâmetros de calibração para compensar as condições específicas do ambiente em que a válvula está instalada.
8. Não Realizar Manutenção Regular
A calibração de válvulas de segurança não deve ser vista como uma tarefa única, mas sim como parte de um programa de manutenção contínua. Ignorar a manutenção regular pode levar a falhas e comprometer a segurança. Para evitar esse erro, implemente um cronograma de manutenção que inclua verificações regulares e recalibrações conforme necessário. Isso garantirá que as válvulas operem de maneira eficaz e segura ao longo do tempo.
Em resumo, a calibração de válvulas de segurança é um processo crítico que requer atenção aos detalhes e um compromisso com a segurança. Evitar erros comuns, como falta de preparação, uso de equipamentos inadequados e falta de documentação, é essencial para garantir que as válvulas operem de maneira eficaz. Investir em treinamento e manutenção regular também é fundamental para minimizar riscos e garantir a segurança operacional em ambientes industriais.
Manutenção e Verificação Regular da Válvula de Segurança após a Calibração
A manutenção e verificação regular das válvulas de segurança são essenciais para garantir a segurança e a eficiência operacional em sistemas industriais. Após a calibração, é fundamental implementar um programa de manutenção que assegure que as válvulas continuem a operar dentro dos parâmetros especificados. Neste artigo, discutiremos a importância da manutenção regular, as práticas recomendadas e os benefícios de manter as válvulas de segurança em boas condições.
1. Importância da Manutenção Regular
A manutenção regular das válvulas de segurança é crucial para prevenir falhas operacionais e garantir a segurança dos trabalhadores e das instalações. As válvulas de segurança são projetadas para abrir e fechar em pressões específicas, e qualquer desvio desses parâmetros pode resultar em acidentes graves, como explosões ou vazamentos. Portanto, a manutenção regular ajuda a identificar problemas antes que eles se tornem críticos, garantindo que as válvulas funcionem corretamente quando necessário.
Além disso, a manutenção regular contribui para a longevidade do equipamento. Válvulas bem mantidas tendem a ter uma vida útil mais longa, reduzindo a necessidade de substituições frequentes e os custos associados. Isso não apenas economiza dinheiro, mas também minimiza o tempo de inatividade da planta, permitindo que as operações continuem sem interrupções.
2. Práticas Recomendadas para Manutenção
Para garantir a eficácia da manutenção das válvulas de segurança, é importante seguir algumas práticas recomendadas:
- Inspeções Visuais Regulares: Realize inspeções visuais periódicas para verificar se há sinais de desgaste, corrosão ou danos. Componentes danificados devem ser substituídos imediatamente para evitar falhas.
- Limpeza: Mantenha as válvulas limpas e livres de detritos. A sujeira e a corrosão podem afetar o desempenho da válvula, portanto, a limpeza regular é essencial.
- Testes de Funcionamento: Realize testes de funcionamento regulares para garantir que a válvula abra e feche nas pressões corretas. Documente os resultados dos testes para referência futura.
- Verificação de Conexões: Verifique todas as conexões e fixações para garantir que estejam firmes e seguras. Conexões soltas podem causar vazamentos e comprometer a segurança.
- Documentação: Mantenha registros detalhados de todas as manutenções realizadas, incluindo inspeções, testes e substituições de peças. Essa documentação é importante para auditorias e para garantir a conformidade com as normas de segurança.
3. Frequência da Manutenção
A frequência da manutenção das válvulas de segurança pode variar dependendo do tipo de válvula, das condições de operação e das recomendações do fabricante. Em geral, recomenda-se realizar inspeções visuais mensais e testes de funcionamento a cada seis meses. No entanto, em ambientes de alta demanda ou em condições adversas, pode ser necessário aumentar a frequência das manutenções.
Além disso, é importante realizar uma verificação completa da válvula após qualquer evento significativo, como uma alteração nas condições de operação, uma parada prolongada ou uma manutenção em outros componentes do sistema. Essas verificações garantem que a válvula esteja pronta para operar de forma segura e eficiente.
4. Treinamento da Equipe
Um aspecto fundamental da manutenção regular é o treinamento da equipe responsável pela operação e manutenção das válvulas de segurança. A equipe deve ser treinada para identificar sinais de problemas, realizar inspeções e testes adequados e seguir os procedimentos de manutenção estabelecidos. Investir em treinamentos regulares ajuda a garantir que todos os envolvidos compreendam a importância da manutenção e as melhores práticas a serem seguidas.
5. Calibração de Equipamentos Relacionados
Além da manutenção das válvulas de segurança, é importante garantir que todos os equipamentos relacionados, como manômetros e termômetros, também estejam calibrados e em boas condições. A calibração de equipamentos laboratoriais é essencial para garantir medições precisas e confiáveis, que são fundamentais para o funcionamento adequado das válvulas de segurança. Equipamentos de medição não calibrados podem levar a medições imprecisas, comprometendo a eficácia da válvula e a segurança do sistema.
6. Benefícios da Manutenção Regular
Implementar um programa de manutenção regular para válvulas de segurança traz uma série de benefícios, incluindo:
- Segurança Aumentada: A manutenção regular ajuda a identificar e corrigir problemas antes que se tornem críticos, aumentando a segurança operacional.
- Redução de Custos: Válvulas bem mantidas têm uma vida útil mais longa, reduzindo a necessidade de substituições frequentes e os custos associados.
- Eficiência Operacional: A manutenção regular garante que as válvulas operem de maneira eficaz, minimizando o tempo de inatividade e melhorando a eficiência do sistema.
- Conformidade Regulatória: Manter registros detalhados de manutenção ajuda a garantir a conformidade com as normas de segurança e regulatórias.
Em resumo, a manutenção e verificação regular das válvulas de segurança após a calibração são essenciais para garantir a segurança e a eficiência operacional em sistemas industriais. Implementar práticas recomendadas, realizar inspeções e testes regulares, e investir no treinamento da equipe são passos fundamentais para manter as válvulas em boas condições. Além disso, a calibração de equipamentos relacionados é crucial para garantir medições precisas e confiáveis. Ao priorizar a manutenção regular, as empresas podem minimizar riscos, reduzir custos e garantir um ambiente de trabalho seguro e eficiente.
Em conclusão, a calibração de válvulas de segurança é um elemento essencial para a operação segura e eficiente de sistemas industriais. Através de um processo metódico que inclui a preparação adequada, a realização de testes e a manutenção regular, é possível garantir que essas válvulas funcionem dentro dos parâmetros especificados, protegendo tanto os equipamentos quanto os trabalhadores. Evitar erros comuns e implementar práticas de manutenção eficazes não apenas aumenta a segurança operacional, mas também contribui para a longevidade do equipamento e a conformidade com as normas regulatórias. Portanto, investir tempo e recursos na calibração e manutenção das válvulas de segurança é uma decisão estratégica que traz benefícios significativos para qualquer operação industrial.