Calibração de Equipamentos de Medição: Garantindo a Segurança do Trabalho com Precisão
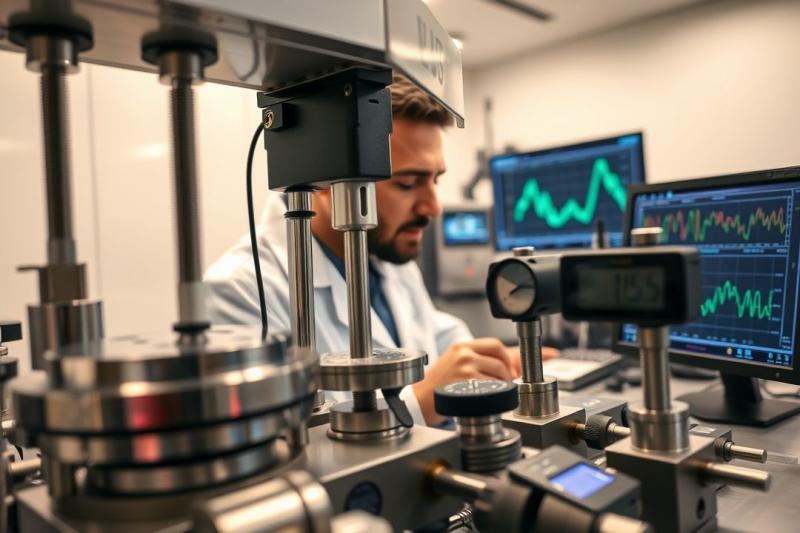
Por: Anderson - 20 de Março de 2025
A calibração de equipamentos de medição segurança do trabalho é um aspecto fundamental para garantir a precisão e a confiabilidade dos instrumentos utilizados em ambientes laborais. Com a crescente preocupação com a segurança dos trabalhadores, a calibração adequada se torna essencial para evitar acidentes e garantir a conformidade com as normas regulamentadoras. Neste artigo, abordaremos a importância da calibração, os métodos utilizados, a frequência recomendada e as consequências da falta desse procedimento crítico.
Importância da Calibração na Segurança do Trabalho
A calibração de equipamentos de medição é um processo essencial que garante a precisão e a confiabilidade dos instrumentos utilizados em diversas atividades laborais. No contexto da segurança do trabalho, essa prática se torna ainda mais crítica, pois a precisão das medições pode impactar diretamente a saúde e a segurança dos trabalhadores. A seguir, discutiremos a importância da calibração na segurança do trabalho, abordando suas implicações e benefícios.
Em primeiro lugar, a calibração assegura que os equipamentos de medição estejam funcionando dentro dos padrões estabelecidos. Isso é vital em ambientes onde a precisão é crucial, como em indústrias químicas, de construção e de manufatura. Por exemplo, instrumentos que medem a pressão, temperatura ou níveis de substâncias perigosas devem fornecer leituras exatas para evitar situações de risco. Se um medidor de pressão estiver descalibrado, pode levar a uma explosão ou a vazamentos de substâncias tóxicas, colocando em risco a vida dos trabalhadores e a integridade do ambiente de trabalho.
Além disso, a calibração regular dos equipamentos de medição é uma exigência legal em muitos setores. Normas regulamentadoras, como as estabelecidas pelo Ministério do Trabalho e Emprego (MTE) no Brasil, exigem que os equipamentos utilizados em ambientes de trabalho sejam calibrados periodicamente. O não cumprimento dessas normas pode resultar em penalidades severas, incluindo multas e até a interdição de atividades. Portanto, a calibração não é apenas uma questão de segurança, mas também de conformidade legal.
Outro aspecto importante é que a calibração contribui para a eficiência operacional. Equipamentos bem calibrados operam de maneira mais eficiente, reduzindo o desperdício de materiais e tempo. Por exemplo, em uma linha de produção, um sensor de temperatura que não está calibrado corretamente pode levar a um superaquecimento de máquinas, resultando em paradas inesperadas e custos adicionais com manutenção. A calibração regular ajuda a evitar esses problemas, garantindo que os processos operacionais sejam realizados de forma contínua e segura.
Além disso, a calibração é fundamental para a manutenção da qualidade dos produtos. Em setores como o alimentício e farmacêutico, a precisão nas medições é crucial para garantir que os produtos atendam aos padrões de qualidade e segurança. Um erro na medição de ingredientes pode resultar em produtos inseguros, que podem causar sérios problemas de saúde aos consumidores. Portanto, a calibração não apenas protege os trabalhadores, mas também os consumidores finais.
Outro ponto a ser considerado é a responsabilidade social das empresas. Ao garantir que seus equipamentos de medição estejam calibrados e funcionando corretamente, as empresas demonstram um compromisso com a segurança e o bem-estar de seus funcionários. Isso não apenas melhora a moral dos trabalhadores, mas também fortalece a reputação da empresa no mercado. Organizações que priorizam a segurança tendem a atrair e reter talentos, além de conquistar a confiança dos clientes.
É importante ressaltar que a calibração deve ser realizada por profissionais qualificados e em ambientes controlados. A falta de conhecimento técnico pode levar a erros na calibração, comprometendo a segurança e a eficácia dos equipamentos. Portanto, investir em treinamento e na contratação de serviços especializados é uma prática recomendada para garantir que a calibração seja realizada de forma adequada.
Além disso, a calibração deve ser parte de um programa de manutenção preventiva mais amplo. Equipamentos de medição, como redutores de velocidade, também requerem atenção e cuidados regulares. A manutenção de redutor é um exemplo de como a calibração e a manutenção devem andar de mãos dadas para garantir a segurança e a eficiência operacional. A falta de manutenção pode levar a falhas mecânicas, que podem resultar em acidentes e interrupções na produção.
Por fim, a calibração de equipamentos de medição é uma prática indispensável para garantir a segurança no trabalho. Ela assegura a precisão das medições, cumpre com as exigências legais, melhora a eficiência operacional e mantém a qualidade dos produtos. Além disso, demonstra a responsabilidade social das empresas e deve ser realizada por profissionais qualificados como parte de um programa de manutenção abrangente. Investir na calibração é, portanto, um passo fundamental para proteger os trabalhadores e garantir um ambiente de trabalho seguro e produtivo.
Métodos de Calibração de Equipamentos de Medição
A calibração de equipamentos de medição é um processo essencial para garantir a precisão e a confiabilidade dos instrumentos utilizados em diversas aplicações industriais e laboratoriais. Existem diferentes métodos de calibração, cada um adequado a tipos específicos de equipamentos e medições. Neste artigo, exploraremos os principais métodos de calibração, suas aplicações e a importância de cada um deles.
Um dos métodos mais comuns de calibração é a calibração por comparação. Este método envolve a comparação das medições de um equipamento com um padrão de referência conhecido e rastreável. O equipamento a ser calibrado é colocado em operação e suas leituras são comparadas com as do padrão. Se houver discrepâncias, ajustes são feitos até que as medições estejam dentro das tolerâncias aceitáveis. Este método é amplamente utilizado em laboratórios de metrologia e é eficaz para uma variedade de instrumentos, como termômetros, manômetros e medidores de pressão.
Outro método importante é a calibração por ajuste. Neste caso, o equipamento é ajustado diretamente para que suas medições correspondam a um padrão de referência. Este método é frequentemente utilizado em instrumentos que possuem um mecanismo de ajuste interno, como multímetros e calibradores de pressão. A calibração por ajuste é crucial para garantir que os instrumentos estejam sempre operando dentro das especificações exigidas, especialmente em ambientes onde a precisão é crítica.
A calibração em campo é um método que se destaca pela sua praticidade. Este tipo de calibração é realizado no local onde o equipamento está instalado, em vez de ser enviado para um laboratório. A calibração em campo é especialmente útil para equipamentos que não podem ser facilmente removidos, como sensores de temperatura e pressão instalados em processos industriais. Embora a calibração em campo possa ser menos precisa do que a calibração em laboratório, ela oferece a vantagem de minimizar o tempo de inatividade do equipamento e garantir que as medições sejam feitas em condições reais de operação.
Além disso, a calibração por simulação é um método que utiliza dispositivos de simulação para reproduzir as condições de medição. Este método é frequentemente utilizado para calibrar instrumentos que medem variáveis complexas, como fluxo e nível. A calibração por simulação permite que os técnicos ajustem os instrumentos de acordo com as condições específicas que eles enfrentarão em operação, garantindo que as medições sejam precisas e confiáveis.
Outro método relevante é a calibração por transferência. Este método envolve o uso de um equipamento de medição que já foi calibrado e é utilizado para calibrar outro instrumento. A calibração por transferência é útil quando não é possível acessar um padrão de referência direto ou quando o equipamento a ser calibrado é muito grande ou pesado para ser transportado. Este método é comum em indústrias onde equipamentos de grande porte são utilizados, como na calibração de redutores de velocidade, onde a manutenção em redutores é essencial para garantir a precisão e a eficiência do sistema.
Além dos métodos mencionados, a calibração também pode ser realizada utilizando padrões de referência que são certificados e rastreáveis. Esses padrões são fundamentais para garantir a confiabilidade das medições, pois são calibrados em laboratórios acreditados e seguem normas internacionais. A utilização de padrões rastreáveis é uma prática recomendada em setores que exigem alta precisão, como a indústria farmacêutica e a produção de alimentos.
É importante ressaltar que a escolha do método de calibração deve levar em consideração diversos fatores, como o tipo de equipamento, a precisão necessária, o ambiente de operação e os recursos disponíveis. Cada método tem suas vantagens e desvantagens, e a seleção adequada pode impactar diretamente a qualidade das medições e a segurança do trabalho.
Além disso, a calibração deve ser realizada por profissionais qualificados e treinados, que compreendam as especificações dos equipamentos e os procedimentos corretos. A falta de conhecimento técnico pode resultar em erros de calibração, comprometendo a segurança e a eficácia dos instrumentos. Portanto, investir em treinamento e na contratação de serviços especializados é fundamental para garantir que a calibração seja realizada de forma adequada.
Por fim, a calibração de equipamentos de medição é um processo crítico que deve ser realizado regularmente para garantir a precisão e a confiabilidade das medições. Os métodos de calibração variam de acordo com o tipo de equipamento e as condições de operação, e a escolha do método adequado é essencial para garantir a segurança e a eficiência dos processos. Com a calibração correta, as empresas podem minimizar riscos, aumentar a eficiência operacional e garantir a conformidade com as normas regulamentadoras.
Frequência Recomendada para Calibração de Equipamentos
A calibração de equipamentos de medição é uma prática essencial para garantir a precisão e a confiabilidade das medições em diversos setores. No entanto, a eficácia da calibração depende não apenas da qualidade do processo, mas também da frequência com que ela é realizada. A seguir, discutiremos a importância de estabelecer uma frequência adequada para a calibração de equipamentos, os fatores que influenciam essa frequência e as recomendações gerais para diferentes tipos de instrumentos.
Em primeiro lugar, é importante entender que a frequência de calibração pode variar significativamente de acordo com o tipo de equipamento, a aplicação e o ambiente em que ele é utilizado. Equipamentos que operam em condições extremas, como altas temperaturas, umidade ou vibrações, podem exigir calibrações mais frequentes. Por exemplo, instrumentos utilizados em ambientes industriais pesados, como fábricas e canteiros de obras, podem sofrer desgastes mais rápidos e, portanto, necessitar de calibrações regulares para garantir a precisão das medições.
Além disso, a frequência de calibração também pode ser influenciada pela criticidade das medições. Em setores onde a precisão é vital, como na indústria farmacêutica ou na produção de alimentos, a calibração deve ser realizada com mais frequência. A Calibração de equipamentos laboratoriais é um exemplo onde a precisão das medições é crucial para garantir a qualidade e a segurança dos produtos finais. Nesses casos, recomenda-se que a calibração seja realizada pelo menos uma vez por ano, ou até mesmo trimestralmente, dependendo das diretrizes específicas do setor e das normas regulamentadoras aplicáveis.
Outro fator a ser considerado é a frequência de uso do equipamento. Equipamentos que são utilizados com alta frequência podem exigir calibrações mais regulares. Por exemplo, um medidor de pressão que é utilizado diariamente em um ambiente industrial pode precisar ser calibrado a cada seis meses, enquanto um instrumento que é utilizado apenas ocasionalmente pode ser calibrado anualmente. A análise do histórico de uso e desempenho do equipamento pode ajudar a determinar a frequência ideal de calibração.
Além disso, a idade do equipamento também pode influenciar a frequência de calibração. Equipamentos mais antigos podem apresentar maior probabilidade de desvio nas medições, o que pode exigir calibrações mais frequentes. É importante monitorar o desempenho do equipamento ao longo do tempo e ajustar a frequência de calibração conforme necessário. Se um equipamento começar a apresentar leituras inconsistentes, pode ser um sinal de que a calibração deve ser realizada com mais frequência.
As recomendações de calibração também podem ser influenciadas por normas e regulamentos específicos do setor. Muitas indústrias têm diretrizes estabelecidas que determinam a frequência mínima de calibração para diferentes tipos de equipamentos. Por exemplo, a norma ISO 9001, que estabelece requisitos para sistemas de gestão da qualidade, recomenda que as organizações realizem calibrações regulares para garantir a conformidade com os padrões de qualidade. Portanto, é fundamental que as empresas estejam cientes das normas aplicáveis ao seu setor e sigam as diretrizes recomendadas.
Além disso, a calibração deve ser parte de um programa de manutenção preventiva mais amplo. A manutenção regular dos equipamentos, incluindo limpeza e inspeção, pode ajudar a prolongar a vida útil dos instrumentos e garantir que eles permaneçam dentro das especificações. A calibração deve ser realizada em conjunto com outras atividades de manutenção para garantir que o equipamento esteja sempre em condições ideais de operação.
Por fim, é importante ressaltar que a documentação adequada é essencial para o processo de calibração. Manter registros detalhados das calibrações realizadas, incluindo datas, resultados e ajustes feitos, pode ajudar a monitorar o desempenho do equipamento ao longo do tempo e a identificar tendências que possam indicar a necessidade de calibrações mais frequentes. A documentação também é fundamental para garantir a conformidade com as normas regulamentadoras e para fornecer evidências de que a calibração foi realizada de acordo com os padrões estabelecidos.
Em resumo, a frequência recomendada para a calibração de equipamentos de medição é um aspecto crítico que deve ser cuidadosamente considerado. Fatores como o tipo de equipamento, as condições de operação, a criticidade das medições e as normas do setor influenciam a frequência de calibração. Estabelecer uma rotina de calibração adequada não apenas garante a precisão das medições, mas também contribui para a segurança e a eficiência operacional. Portanto, as empresas devem investir tempo e recursos na definição de um cronograma de calibração que atenda às suas necessidades específicas e que esteja alinhado com as melhores práticas do setor.
Consequências da Falta de Calibração na Segurança do Trabalho
A calibração de equipamentos de medição é uma prática essencial para garantir a precisão e a confiabilidade das medições em ambientes de trabalho. A falta de calibração pode ter consequências graves, não apenas para a segurança dos trabalhadores, mas também para a eficiência operacional e a qualidade dos produtos. Neste artigo, discutiremos as principais consequências da falta de calibração na segurança do trabalho, destacando a importância de manter os equipamentos devidamente calibrados.
Uma das consequências mais imediatas da falta de calibração é o aumento do risco de acidentes. Equipamentos de medição, como manômetros, termômetros e sensores, são utilizados para monitorar condições críticas em ambientes industriais. Se esses instrumentos não estiverem calibrados corretamente, as medições podem ser imprecisas, levando a decisões erradas que podem resultar em acidentes. Por exemplo, um termômetro industrial digital que não está calibrado pode fornecer leituras incorretas de temperatura, levando a superaquecimento de equipamentos ou processos, o que pode resultar em explosões ou incêndios. Portanto, a falta de calibração pode comprometer a segurança dos trabalhadores e a integridade das instalações.
Além do risco de acidentes, a falta de calibração pode levar a falhas nos processos operacionais. Equipamentos que não estão funcionando corretamente podem causar interrupções na produção, resultando em perdas financeiras significativas. Por exemplo, se um sensor de pressão estiver descalibrado, pode não detectar uma pressão excessiva em um sistema, levando a falhas mecânicas e paradas não programadas. Essas interrupções não apenas afetam a produtividade, mas também podem resultar em custos adicionais com reparos e manutenção.
Outro aspecto a ser considerado é a qualidade dos produtos. Em setores onde a precisão das medições é crucial, como na indústria alimentícia e farmacêutica, a falta de calibração pode comprometer a qualidade dos produtos finais. Um equipamento de medição que não está calibrado pode resultar em produtos que não atendem aos padrões de qualidade, o que pode levar a recalls, multas e danos à reputação da empresa. A calibração regular é, portanto, uma prática essencial para garantir que os produtos sejam seguros e de alta qualidade.
A falta de calibração também pode ter implicações legais. Muitas indústrias são obrigadas a seguir normas e regulamentos que exigem a calibração regular de equipamentos de medição. O não cumprimento dessas normas pode resultar em penalidades severas, incluindo multas e até a suspensão das operações. Além disso, em caso de acidentes, a falta de documentação que comprove a calibração dos equipamentos pode resultar em responsabilidades legais para a empresa. Portanto, manter os equipamentos calibrados não é apenas uma questão de segurança, mas também de conformidade legal.
Outro ponto importante é o impacto na moral dos funcionários. Quando os trabalhadores percebem que os equipamentos não estão sendo mantidos adequadamente, isso pode afetar sua confiança na segurança do ambiente de trabalho. A falta de calibração pode criar um clima de insegurança, onde os funcionários se sentem vulneráveis a acidentes. Isso pode resultar em um aumento do estresse e da insatisfação no trabalho, afetando a produtividade e a retenção de talentos. Portanto, investir na calibração dos equipamentos é uma forma de demonstrar o compromisso da empresa com a segurança e o bem-estar dos funcionários.
Além disso, a falta de calibração pode levar a um aumento nos custos operacionais. Equipamentos que não estão funcionando corretamente podem consumir mais energia e recursos, resultando em custos mais altos. Por exemplo, um motor que não está operando dentro das especificações pode exigir mais energia para funcionar, aumentando os custos de eletricidade. A calibração regular ajuda a garantir que os equipamentos operem de forma eficiente, reduzindo os custos operacionais e melhorando a rentabilidade da empresa.
Por fim, a falta de calibração pode afetar a competitividade da empresa no mercado. Em um ambiente de negócios cada vez mais competitivo, as empresas que não mantêm seus equipamentos calibrados podem perder oportunidades para concorrentes que priorizam a segurança e a qualidade. A reputação de uma empresa é construída com base na confiança dos clientes, e a falta de calibração pode prejudicar essa confiança. Portanto, investir na calibração dos equipamentos é uma estratégia importante para garantir a competitividade e o sucesso a longo prazo.
Em resumo, a falta de calibração de equipamentos de medição pode ter consequências graves para a segurança do trabalho, a eficiência operacional, a qualidade dos produtos e a conformidade legal. As empresas devem priorizar a calibração regular de seus equipamentos para garantir um ambiente de trabalho seguro e produtivo. A calibração não é apenas uma questão de conformidade, mas uma prática essencial para proteger os trabalhadores, melhorar a eficiência e garantir a qualidade dos produtos. Portanto, é fundamental que as organizações implementem programas de calibração eficazes e mantenham seus equipamentos em condições ideais de operação.
Em conclusão, a calibração de equipamentos de medição é uma prática indispensável para assegurar a segurança no ambiente de trabalho. A precisão e a confiabilidade dos instrumentos são cruciais para prevenir acidentes, garantir a qualidade dos produtos e cumprir com as normas regulamentadoras. Ao compreender a importância da calibração, os métodos disponíveis, a frequência necessária e as consequências da falta desse procedimento, as empresas podem adotar medidas proativas para proteger seus trabalhadores e otimizar suas operações. Investir na calibração não é apenas uma questão de conformidade, mas um compromisso com a segurança e a eficiência que traz benefícios a longo prazo para todos os envolvidos.