Calibração de Manômetro: Como Garantir Medidas Precisas e Confiáveis
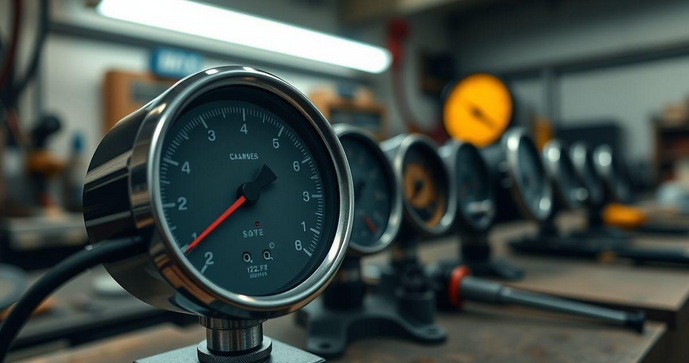
Por: Anderson - 16 de Março de 2025
A calibração de manômetro é um processo fundamental para garantir a precisão e a confiabilidade das medições em diversos setores, como industrial e laboratorial. Com o uso adequado, é possível evitar erros que podem comprometer a segurança e a eficiência dos sistemas. Neste artigo, abordaremos a importância da calibração, o passo a passo para realizá-la corretamente e os cuidados necessários para manter a precisão dos manômetros ao longo do tempo.
Importância da Calibração de Manômetro para Medições Precisar
A calibração de manômetros é um procedimento essencial que garante a precisão das medições de pressão em diversos setores, como indústria, laboratórios e até mesmo em aplicações domésticas. A precisão nas medições é crucial, pois qualquer erro pode resultar em consequências significativas, como falhas em equipamentos, perda de eficiência e até riscos à segurança. Neste contexto, entender a importância da calibração de manômetros é fundamental para assegurar a qualidade e a confiabilidade dos processos.
Um manômetro é um instrumento utilizado para medir a pressão de gases ou líquidos em um sistema. A precisão desse instrumento é vital, pois a pressão inadequada pode levar a falhas em sistemas hidráulicos e pneumáticos, comprometendo a operação de máquinas e equipamentos. Por isso, a calibração regular é necessária para garantir que o manômetro forneça leituras exatas e confiáveis.
Um dos principais motivos para a calibração de manômetros é a prevenção de erros de medição. Com o tempo, os manômetros podem sofrer desgastes ou danos que afetam sua precisão. Fatores como vibrações, temperaturas extremas e corrosão podem impactar o funcionamento do instrumento. A calibração permite identificar e corrigir essas falhas, assegurando que as medições estejam dentro das especificações exigidas.
Além disso, a calibração é uma exigência em muitos setores regulados, como o farmacêutico e o alimentício. Nesses setores, a precisão das medições é crítica para garantir a qualidade dos produtos e a conformidade com normas e regulamentos. A falta de calibração pode resultar em produtos fora dos padrões, levando a multas, recalls e danos à reputação da empresa. Portanto, a calibração regular não é apenas uma prática recomendada, mas uma necessidade legal em muitos casos.
Outro aspecto importante da calibração de manômetros é a otimização de processos. Quando os manômetros estão calibrados corretamente, as medições são mais precisas, permitindo que os operadores ajustem os sistemas de forma mais eficaz. Isso pode resultar em economia de energia, redução de desperdícios e aumento da eficiência operacional. Por exemplo, em sistemas de aquecimento, a pressão correta é essencial para garantir que o calor seja distribuído de maneira uniforme. A calibração adequada do manômetro garante que o sistema funcione de maneira ideal, evitando sobrecargas e danos.
Além disso, a calibração de manômetros contribui para a segurança no ambiente de trabalho. Em indústrias onde a pressão é um fator crítico, como na petroquímica, a precisão das medições pode prevenir acidentes graves. Um manômetro descalibrado pode indicar uma pressão segura quando, na verdade, a pressão está em níveis perigosos. Isso pode levar a explosões, vazamentos e outros incidentes que colocam em risco a vida dos trabalhadores e a integridade das instalações. Portanto, a calibração regular é uma medida de segurança indispensável.
Outro ponto a ser considerado é a durabilidade dos manômetros. Instrumentos que são calibrados regularmente tendem a ter uma vida útil mais longa. A manutenção preventiva, que inclui a calibração, ajuda a identificar problemas antes que se tornem sérios, evitando a necessidade de substituições frequentes. Isso não apenas reduz os custos operacionais, mas também minimiza o impacto ambiental associado ao descarte de equipamentos.
Para garantir a eficácia da calibração, é importante que ela seja realizada por profissionais qualificados e utilizando equipamentos adequados. A calibração deve ser feita em condições controladas, onde a temperatura e a pressão sejam monitoradas. Além disso, é essencial seguir as recomendações do fabricante do manômetro e as normas técnicas aplicáveis. A documentação adequada do processo de calibração também é fundamental, pois fornece um histórico que pode ser útil em auditorias e inspeções.
Por fim, a calibração de manômetros não deve ser vista apenas como uma tarefa a ser realizada, mas como uma parte integrante da gestão de qualidade de qualquer operação que dependa de medições precisas. Investir em calibração é investir na segurança, eficiência e qualidade dos processos. Para complementar a manutenção de manômetros, é importante também considerar a manutenção de redutor, que pode impactar diretamente na performance dos sistemas que utilizam manômetros.
Em resumo, a calibração de manômetros é um procedimento essencial que garante a precisão das medições, previne erros, otimiza processos e assegura a segurança no ambiente de trabalho. A prática regular de calibração deve ser parte da rotina de manutenção de qualquer operação que dependa de medições de pressão, contribuindo para a eficiência e a qualidade dos produtos e serviços oferecidos.
Passo a Passo para Realizar a Calibração de Manômetro
A calibração de manômetros é um processo fundamental para garantir a precisão das medições de pressão em diversos sistemas. Realizar a calibração de forma adequada não apenas assegura a confiabilidade dos dados, mas também contribui para a segurança e eficiência operacional. A seguir, apresentamos um passo a passo detalhado para realizar a calibração de manômetros, garantindo que você possa executar essa tarefa com eficácia.
1. Preparação e Planejamento
Antes de iniciar o processo de calibração, é essencial realizar um planejamento adequado. Isso inclui a escolha do local onde a calibração será realizada, que deve ser um ambiente controlado, livre de vibrações e interferências externas. Além disso, reúna todos os equipamentos necessários, como o manômetro a ser calibrado, um manômetro de referência (calibrado e certificado), ferramentas de ajuste e, se necessário, um computador para registrar os dados.
2. Verificação do Equipamento
Antes de iniciar a calibração, verifique se o manômetro a ser calibrado está em boas condições. Inspecione visualmente o instrumento em busca de danos, corrosão ou vazamentos. Certifique-se de que todas as conexões estão firmes e que não há obstruções nas entradas e saídas. Um manômetro danificado pode fornecer leituras imprecisas, comprometendo todo o processo de calibração.
3. Conexão do Manômetro de Referência
Conecte o manômetro de referência ao sistema onde o manômetro a ser calibrado será instalado. É importante que o manômetro de referência tenha uma precisão superior ao manômetro que está sendo calibrado. Isso garantirá que as medições sejam confiáveis. Certifique-se de que as conexões estão bem apertadas para evitar vazamentos que possam afetar as leituras.
4. Estabelecimento de Pressões de Teste
Defina os pontos de pressão que serão utilizados durante a calibração. É comum calibrar o manômetro em pelo menos três pontos: baixa, média e alta pressão. Esses pontos devem abranger a faixa de operação do manômetro. Por exemplo, se o manômetro opera entre 0 e 100 psi, você pode escolher 0 psi, 50 psi e 100 psi como pontos de teste.
5. Aplicação da Pressão
Utilize uma bomba de pressão ou um sistema de controle de pressão para aplicar as pressões definidas nos pontos de teste. Aumente a pressão lentamente até o primeiro ponto de teste e aguarde alguns instantes para que o manômetro estabilize. Registre a leitura do manômetro a ser calibrado e a leitura do manômetro de referência. É importante que a pressão seja aplicada de forma controlada para evitar picos que possam danificar o equipamento.
6. Comparação das Leituras
Compare as leituras do manômetro a ser calibrado com as do manômetro de referência. Anote as diferenças entre as leituras. Se a diferença estiver dentro da tolerância especificada pelo fabricante, o manômetro está calibrado corretamente. Caso contrário, será necessário realizar ajustes. A diferença entre as leituras é chamada de erro de medição e deve ser documentada para futuras referências.
7. Ajuste do Manômetro
Se o manômetro a ser calibrado apresentar um erro fora da tolerância, será necessário ajustá-lo. A maioria dos manômetros possui um parafuso de ajuste que permite corrigir a leitura. Siga as instruções do fabricante para realizar o ajuste corretamente. Após o ajuste, repita o processo de aplicação de pressão e comparação das leituras para garantir que o manômetro esteja agora dentro da faixa aceitável.
8. Repetição do Processo
Repita o processo de calibração para todos os pontos de teste definidos. Isso garantirá que o manômetro esteja calibrado em toda a sua faixa de operação. É importante que cada ponto de teste seja verificado e ajustado, se necessário, para assegurar a precisão em todas as condições de operação.
9. Documentação
Após concluir a calibração, é fundamental documentar todo o processo. Registre as leituras obtidas, os ajustes realizados e as condições em que a calibração foi feita. Essa documentação é importante para auditorias e para garantir a rastreabilidade do processo. Além disso, mantenha um histórico de calibrações anteriores, pois isso pode ajudar a identificar padrões de desgaste ou problemas recorrentes.
10. Manutenção Contínua
Por fim, lembre-se de que a calibração não é um evento único, mas parte de um programa de manutenção contínua. Estabeleça um cronograma de calibração regular com base nas recomendações do fabricante e nas necessidades específicas do seu sistema. Além disso, considere a manutenção em redutores e outros equipamentos que possam impactar a precisão das medições. A manutenção preventiva é essencial para garantir que os manômetros continuem a operar de forma eficaz e precisa ao longo do tempo.
Seguindo esses passos, você poderá realizar a calibração de manômetros de forma eficaz, garantindo medições precisas e confiáveis. A calibração regular é um investimento na qualidade e segurança dos processos, contribuindo para a eficiência operacional e a conformidade com normas e regulamentos.
Erros Comuns na Calibração de Manômetros e Como Evitá-los
A calibração de manômetros é um processo crítico para garantir a precisão das medições de pressão em diversos sistemas. No entanto, existem erros comuns que podem comprometer a eficácia desse procedimento. Identificar e evitar esses erros é fundamental para assegurar que os manômetros funcionem corretamente e forneçam dados confiáveis. Neste artigo, abordaremos os erros mais frequentes na calibração de manômetros e como preveni-los.
1. Falta de Planejamento Adequado
Um dos erros mais comuns na calibração de manômetros é a falta de planejamento. Muitas vezes, a calibração é realizada de forma apressada, sem considerar as condições ideais para o processo. É essencial escolher um ambiente controlado, livre de vibrações e interferências externas. Além disso, é importante ter todos os equipamentos necessários à mão antes de iniciar a calibração. Um planejamento inadequado pode levar a medições imprecisas e a necessidade de recalibrações frequentes.
2. Não Verificar o Estado do Manômetro
Antes de iniciar a calibração, é crucial verificar o estado do manômetro. Ignorar essa etapa pode resultar em medições erradas. Danos visíveis, corrosão ou vazamentos podem afetar a precisão do instrumento. Sempre faça uma inspeção visual antes de conectar o manômetro ao sistema. Se o manômetro estiver danificado, ele deve ser reparado ou substituído antes da calibração.
3. Uso de Manômetros de Referência Inadequados
Outro erro comum é utilizar manômetros de referência que não possuem a precisão necessária. O manômetro de referência deve ser calibrado e certificado, com uma precisão superior ao manômetro que está sendo calibrado. Usar um manômetro de referência impreciso compromete todo o processo de calibração, resultando em leituras erradas. Sempre verifique a calibração do manômetro de referência antes de utilizá-lo.
4. Aplicação de Pressão de Forma Apressada
Aplicar pressão de forma apressada é um erro que pode causar danos ao manômetro e resultar em medições imprecisas. A pressão deve ser aumentada lentamente, permitindo que o manômetro estabilize em cada ponto de teste. Se a pressão for aplicada rapidamente, pode haver picos que danificam o instrumento ou causam leituras erradas. Sempre aplique a pressão de maneira controlada e gradual.
5. Não Registrar as Leituras Corretamente
Registrar as leituras de forma inadequada é um erro que pode levar a confusões e a um histórico de calibração impreciso. É fundamental anotar todas as leituras do manômetro a ser calibrado e do manômetro de referência em cada ponto de teste. Além disso, é importante documentar quaisquer ajustes realizados. A falta de documentação pode dificultar a identificação de problemas futuros e a análise de tendências de desempenho.
6. Ignorar as Condições Ambientais
As condições ambientais podem ter um impacto significativo nas medições de pressão. Ignorar fatores como temperatura e umidade pode levar a erros de calibração. Por exemplo, a temperatura pode afetar a densidade do fluido em um sistema, alterando as leituras. Sempre realize a calibração em condições ambientais controladas e registre as condições durante o processo.
7. Não Realizar Calibrações Regulares
A calibração de manômetros não deve ser vista como uma tarefa única, mas como parte de um programa de manutenção contínua. Ignorar a necessidade de calibrações regulares pode resultar em medições imprecisas ao longo do tempo. Estabeleça um cronograma de calibração com base nas recomendações do fabricante e nas necessidades específicas do seu sistema. A falta de calibrações regulares pode comprometer a segurança e a eficiência operacional.
8. Falta de Treinamento Adequado
Realizar a calibração de manômetros requer conhecimento técnico e experiência. A falta de treinamento adequado pode levar a erros durante o processo. É importante que os profissionais responsáveis pela calibração sejam devidamente treinados e compreendam os princípios de funcionamento dos manômetros e os procedimentos de calibração. Investir em treinamento é essencial para garantir a precisão e a confiabilidade das medições.
9. Não Seguir as Instruções do Fabricante
Cada manômetro possui especificações e recomendações do fabricante para calibração. Ignorar essas instruções pode resultar em erros e danos ao equipamento. Sempre consulte o manual do fabricante antes de realizar a calibração e siga as diretrizes fornecidas. Isso garantirá que o processo seja realizado corretamente e que o manômetro funcione de acordo com as especificações.
10. Negligenciar a Calibração de Equipamentos Relacionados
Por fim, é importante lembrar que a calibração de manômetros deve ser parte de um programa de manutenção mais amplo. Negligenciar a calibração de outros equipamentos relacionados, como válvulas e redutores, pode afetar a precisão das medições. A calibração de equipamentos laboratoriais e a manutenção de outros instrumentos devem ser realizadas em conjunto para garantir a eficiência e a segurança do sistema como um todo.
Em resumo, evitar erros comuns na calibração de manômetros é essencial para garantir medições precisas e confiáveis. Um planejamento adequado, a verificação do estado do manômetro, o uso de manômetros de referência adequados e a aplicação controlada de pressão são apenas algumas das práticas que podem ajudar a prevenir problemas. Além disso, a documentação adequada, o treinamento e a manutenção regular são fundamentais para assegurar a eficácia do processo de calibração. Ao seguir essas diretrizes, você poderá realizar calibrações de manômetros de forma eficaz, contribuindo para a segurança e eficiência dos seus sistemas.
Frequência Recomendada para Calibração de Manômetros
A calibração de manômetros é uma prática essencial para garantir a precisão e a confiabilidade das medições de pressão em diversos setores. No entanto, a frequência com que essa calibração deve ser realizada pode variar dependendo de vários fatores, como o tipo de manômetro, a aplicação, as condições de operação e as recomendações do fabricante. Neste artigo, discutiremos a frequência recomendada para a calibração de manômetros e os fatores que influenciam essa decisão.
1. Importância da Frequência de Calibração
Realizar a calibração de manômetros em intervalos regulares é fundamental para assegurar que as medições permaneçam precisas ao longo do tempo. A falta de calibração pode resultar em leituras imprecisas, o que pode comprometer a segurança e a eficiência dos processos. Por exemplo, em indústrias onde a pressão é um fator crítico, como na petroquímica ou na farmacêutica, um manômetro descalibrado pode levar a falhas catastróficas, vazamentos ou produtos fora das especificações. Portanto, estabelecer uma frequência de calibração adequada é uma medida preventiva essencial.
2. Recomendações Gerais de Frequência
Embora a frequência exata de calibração possa variar, existem algumas diretrizes gerais que podem ser seguidas. Em muitos casos, recomenda-se que a calibração de manômetros seja realizada anualmente. No entanto, essa frequência pode ser ajustada com base nas condições específicas de operação e no uso do manômetro. Por exemplo, manômetros utilizados em ambientes agressivos ou que estão sujeitos a vibrações constantes podem exigir calibrações mais frequentes, como a cada seis meses.
Além disso, manômetros que são utilizados em aplicações críticas, onde a precisão é vital, podem necessitar de calibrações trimestrais. Por outro lado, manômetros que operam em condições mais estáveis e que não são utilizados com frequência podem ser calibrados a cada dois anos. É importante que cada empresa avalie suas necessidades específicas e estabeleça um cronograma de calibração que atenda a essas exigências.
3. Fatores que Influenciam a Frequência de Calibração
Vários fatores podem influenciar a frequência recomendada para a calibração de manômetros. Um dos principais fatores é o ambiente em que o manômetro está operando. Ambientes com altas temperaturas, umidade, corrosão ou vibrações podem afetar a precisão do manômetro e, portanto, podem exigir calibrações mais frequentes. Por exemplo, manômetros utilizados em indústrias químicas ou petroquímicas, onde os produtos químicos podem causar corrosão, devem ser calibrados com mais regularidade.
Outro fator a ser considerado é a frequência de uso do manômetro. Manômetros que são utilizados constantemente em processos críticos podem sofrer desgastes mais rapidamente e, portanto, podem exigir calibrações mais frequentes. Em contrapartida, manômetros que são utilizados esporadicamente podem ter uma frequência de calibração mais espaçada. É importante monitorar o desempenho do manômetro e ajustar a frequência de calibração conforme necessário.
Além disso, a idade do manômetro também pode influenciar a frequência de calibração. Manômetros mais antigos podem apresentar maior probabilidade de desvio em suas medições, exigindo calibrações mais frequentes. Portanto, é recomendável que manômetros mais antigos sejam avaliados com mais atenção e calibrados regularmente para garantir a precisão das medições.
4. Normas e Regulamentações
Em muitos setores, existem normas e regulamentações que estabelecem requisitos específicos para a calibração de instrumentos de medição, incluindo manômetros. Por exemplo, indústrias reguladas, como a farmacêutica e a alimentícia, podem ter requisitos rigorosos sobre a frequência de calibração e a documentação do processo. É importante que as empresas estejam cientes dessas normas e as sigam para garantir a conformidade e a qualidade dos produtos.
5. Monitoramento e Avaliação Contínua
Além de estabelecer uma frequência de calibração, é fundamental que as empresas realizem um monitoramento contínuo do desempenho dos manômetros. Isso pode incluir a análise de tendências de medições, a verificação de leituras em comparação com manômetros de referência e a realização de testes periódicos. Se houver indícios de que um manômetro está apresentando leituras imprecisas, mesmo que a calibração não esteja programada, é importante realizar a calibração imediatamente.
Além disso, a documentação adequada de todas as calibrações realizadas é essencial. Isso não apenas ajuda a manter um histórico de desempenho do manômetro, mas também é importante para auditorias e inspeções. A documentação deve incluir informações sobre a data da calibração, as condições em que foi realizada, as leituras obtidas e quaisquer ajustes feitos.
6. Considerações Finais
Em resumo, a frequência recomendada para a calibração de manômetros pode variar dependendo de vários fatores, incluindo o ambiente de operação, a frequência de uso e as normas do setor. Embora uma calibração anual seja uma diretriz comum, é importante que cada empresa avalie suas necessidades específicas e ajuste a frequência conforme necessário. Além disso, o monitoramento contínuo do desempenho dos manômetros e a documentação adequada são fundamentais para garantir a precisão e a confiabilidade das medições.
Por fim, ao considerar a calibração de manômetros, é importante também ter em mente a calibração de outros instrumentos, como o Termômetro industrial digital, que também desempenha um papel crucial na manutenção da qualidade e segurança dos processos. A calibração regular de todos os instrumentos de medição é uma prática essencial para garantir a eficiência e a conformidade em qualquer operação.
Em conclusão, a calibração de manômetros é uma prática essencial que não deve ser negligenciada em qualquer operação que dependa de medições precisas. A frequência adequada de calibração, aliada a um planejamento cuidadoso e à consideração de fatores como o ambiente de operação e a frequência de uso, garante que os manômetros funcionem de maneira eficaz e segura. Ao seguir as diretrizes apresentadas, as empresas podem minimizar erros, otimizar processos e assegurar a conformidade com normas e regulamentos. Investir na calibração regular de manômetros e outros instrumentos de medição é um passo crucial para garantir a qualidade e a segurança em ambientes industriais e laboratoriais.