Calibração e Manutenção de Equipamentos para Garantir Precisão e Desempenho
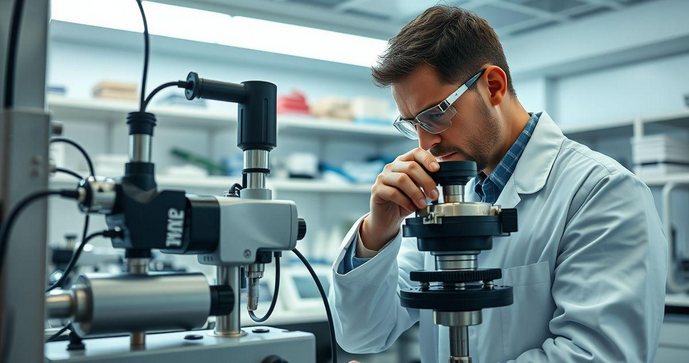
Por: Anderson - 17 de Abril de 2025
Importância da Calibração de Equipamentos para a Indústria
A calibração de equipamentos na indústria é essencial para garantir que os instrumentos de medição e controle operem dentro de especificações aceitáveis. Isso não apenas assegura a precisão nas medições, mas também contribui para a eficiência dos processos produtivos.
Um dos principais benefícios da calibração é a redução de erros. Equipamentos não calibrados podem fornecer dados imprecisos, levando a decisões equivocadas na produção. Por exemplo, em indústrias alimentícias, uma calibração inadequada de balanças pode resultar em produtos fora da conformidade, impactando negativamente a segurança alimentar.
Além disso, a calibração regular ajuda a prolongar a vida útil dos equipamentos. Equipamentos que passam por manutenção e calibração adequadas apresentam menos desgastes e falhas operacionais. Isso se traduz em uma redução de custos com manutenção corretiva e aquisição de novos instrumentos.
Outro ponto relevante é que a calibração é frequentemente exigida por normas e regulamentações. Indústrias que não mantêm seus equipamentos calibrados podem enfrentar penalidades e dificuldades para atender a requisitos de qualidade, como ISO 9001 e outras normas específicas do setor.
Por fim, a calibração e manutenção ajudam a garantir a confiança dos clientes nos produtos. Um controle rigoroso da qualidade e precisão na produção geralmente resulta em maior satisfação do consumidor, melhorando a reputação da marca e levando ao aumento nas vendas.
Processo de Calibração: Passo a Passo
O processo de calibração é fundamental para assegurar que os equipamentos estejam funcionando de maneira adequada e precisa. A seguir, apresentamos um passo a passo para realizar a calibração de equipamentos de forma eficaz.
O primeiro passo é reunir todos os instrumentos e materiais necessários. Isso inclui o equipamento a ser calibrado, padrões de referência, ferramentas específicas e documentação técnica. A escolha de padrões de referência deve ser feita com base nos requisitos do equipamento e na precisão necessária.
Em seguida, deve-se preparar o ambiente de calibração. É importante que o espaço esteja livre de contaminações, vibrações, variações de temperatura e umidade, pois esses fatores podem afetar a precisão da calibração.
O terceiro passo é realizar a verificação inicial do equipamento. Isso envolve testar o equipamento para identificar condições anormais que possam interferir na calibração. Caso o instrumento não esteja funcionando corretamente, deve-se realizar os reparos necessários antes de prosseguir.
Uma vez realizado o check-up, inicia-se a calibração propriamente dita. Isso envolve expor o equipamento a padrões de referência em diferentes pontos de medição e registrar as leituras obtidas. Em seguida, deve-se comparar essas medições com os valores de referência.
Caso as medições estejam fora da tolerância aceitável, ajustes devem ser feitos no equipamento. O ajuste pode variar dependendo do tipo e modelo do instrumento, sendo essencial seguir as orientações do fabricante durante este processo.
Após os ajustes, o equipamento deve ser testado novamente para garantir que agora está operando dentro dos parâmetros desejados. Finalmente, toda a documentação precisa ser atualizada, incluindo registros de calibração e quaisquer ajustes realizados.
Completado o processo de calibração, recomenda-se agendar uma nova calibração com base nas condições de uso e nas recomendações do fabricante, garantindo que o equipamento mantenha a precisão ao longo do tempo.
Manutenção Preventiva: Estratégias e Benefícios
A manutenção preventiva é uma abordagem proativa que visa evitar falhas e garantir a performance otimizada dos equipamentos. Implementar estratégias de manutenção preventiva é crucial para qualquer organização que deseja prolongar a vida útil de seus ativos e manter a produtividade.
Uma das principais estratégias é a criação de um cronograma de manutenção. Esse cronograma deve incluir a frequência das manutenções, baseando-se no tipo de equipamento, na intensidade de uso e nas recomendações do fabricante. O planejamento adequado permite que os técnicos se preparem para realizar as tarefas necessárias sem interromper a produção.
Outra estratégia eficaz envolve o treinamento dos colaboradores. Capacitar a equipe para que compreenda a importância da manutenção preventiva e como identificar sinais de desgaste é fundamental. Isso pode incluir treinamentos periódicos e a disponibilização de manuais e recursos que facilitem o entendimento das máquinas.
Além disso, a adoção de tecnologias de monitoramento pode ser uma vantagem significativa. Sistemas de gestão de manutenção assistida por computador (CMMS) permitem registrar e acompanhar as atividades de manutenção, programar tarefas e gerar relatórios sobre o estado dos equipamentos. Essa visibilidade melhora a tomada de decisões.
Os benefícios da manutenção preventiva são amplos. Principalmente, a redução de custos com reparos emergenciais é um dos mais significativos. Ao evitar falhas inesperadas, empresas economizam em peças de reposição e em mão de obra para reparos, além de reduzir o tempo de inatividade.
Outro benefício importante é o aumento da confiabilidade dos equipamentos. Com a manutenção preventiva, as máquinas têm menos chances de falhar durante a produção, resultando em um ambiente de trabalho mais seguro e eficiente. Essa confiabilidade também se traduz em melhor qualidade dos produtos e serviços.
Finalmente, a manutenção preventiva contribui para a sustentabilidade, uma vez que a eficiência dos equipamentos em funcionamento reduz o desperdício de recursos. Equipamentos bem mantidos utilizam menos energia e geram menos resíduos, o que é benéfico tanto para a empresa quanto para o meio ambiente.
Principais Equipamentos que Necessitam de Calibração Regular
Diversos equipamentos industriais e de laboratório exigem calibração regular para garantir a precisão e a conformidade com normas de qualidade. Conhecer quais são esses equipamentos é essencial para implementar um programa eficiente de calibração.
Um dos principais equipamentos que necessitam de calibração são os instrumentos de medição de pressão, como manômetros e transdutores de pressão. Esses dispositivos são cruciais para controlar processos em indústrias químicas e petroquímicas, onde a precisão nas medições pode impactar a segurança e a eficiência.
Outro grupo importante são os medidores de temperatura, como termômetros e termopares. A calibração regular desses instrumentos é vital na indústria alimentícia e farmacêutica, onde a temperatura deve ser monitorada rigorosamente para garantir a qualidade e a segurança dos produtos.
As balanças eletrônicas também exigem calibração frequente. Em setores como comércio e produção, a precisão nas pesagens é crucial para garantir a conformidade com regulamentações e evitar prejuízos financeiros relacionados a vendas indevidas.
Além desses, os medidores de vazão utilizados em aplicações industriais são outros equipamentos que precisam de calibração regular. A precisão na medição de fluidos é essencial para otimizar processos e manter a integridade de sistemas dentro das indústrias.
Os espectrômetros e cromatógrafos, que são fundamentais em laboratórios químicos e de controle de qualidade, também necessitam de calibração regular para garantir resultados precisos em análises de amostras. A falta de calibração pode levar a falsos resultados e comprometer a pesquisa e produção.
Por fim, instrumentos ópticos, como microscópios e medidores de luz, requerem calibração para garantir que as medições sejam consistentes e precisas. A calibração não só assegura a qualidade dos produtos, mas também a confiabilidade nos resultados de experimentos científicos.
Erros Comuns em Calibração e Como Evitá-los
A calibração é um processo delicado que, quando realizado de forma inadequada, pode resultar em erros significativos. Identificar e evitar esses erros é essencial para garantir a precisão e a confiabilidade dos equipamentos. A seguir, apresentamos alguns erros comuns em calibração e como preveni-los.
Um dos erros mais frequentes é a falta de escolha adequada dos padrões de referência. Usar padrões que não estejam dentro das especificações exigidas ou que não sejam rastreáveis a um padrão nacional pode levar a resultados imprecisos. Para evitar esse erro, sempre utilize padrões de referência que sejam apropriados e calibrados regularmente.
Outro erro comum é a negligência na verificação do estado do equipamento antes da calibração. Esses testes iniciais são cruciais para identificar problemas que possam afetar a calibração. Portanto, é fundamental realizar uma verificação completa do equipamento, incluindo a inspeção de peças desgastadas, antes de iniciar o processo de calibração.
A calibração em condições inadequadas também é uma armadilha comum. Variáveis como temperatura, umidade e vibrações podem impactar a precisão. Para mitigar esse risco, deve-se realizar a calibração em um ambiente controlado, onde essas condições possam ser monitoradas e ajustadas de acordo.
Além disso, a falta de documentação adequada durante o processo de calibração é um erro que pode ter consequências graves. Cada etapa do processo, incluindo os resultados das medições e ajustes feitos, deve ser registrada. Isso não só facilita a identificação de problemas futuros, mas também é essencial para a conformidade com normas de qualidade.
Por último, ignorar a necessidade de calibração recorrente é um grande equívoco. Muitos setores apresentam regulamentos que requerem calibrações em intervalos específicos. Desenvolver um cronograma regular de calibração e seguir as recomendações do fabricante ajuda a garantir a confiança contínua nos resultados obtidos pelos equipamentos.
A educação e o treinamento da equipe responsável pela calibração são essenciais para prevenir todos esses erros. Ao garantir que os funcionários estejam bem informados sobre as melhores práticas e procedimentos, as organizações podem reduzir significativamente as ocorrências de erros durante a calibração.
Impacto da Calibração na Qualidade dos Produtos
A calibração dos equipamentos de medição e controle desempenha um papel crucial na qualidade dos produtos finais. Quando os instrumentos estão calibrados corretamente, eles conseguem fornecer dados precisos, o que se traduz em um processo produtivo mais eficiente e em produtos de alta qualidade.
Um dos principais impactos da calibração é a redução de variações indesejadas nas medições. Isso garante que os produtos atendam às especificações exigidas, reduzindo a quantidade de produtos defeituosos e aumentando a satisfação do cliente. Em indústrias onde a consistência é vital, como a farmacêutica e alimentícia, a calibração é essencial para garantir que cada lote esteja dentro das normas de qualidade.
Além disso, a calibração regular ajuda a prevenir falhas de equipamentos que podem causar interrupções na produção. A manutenção proativa e a calibração garantem que os equipamentos funcionem sem interrupções, resultando em um fluxo de produção contínuo. Esta eficiência operacional não apenas melhora a qualidade do produto, mas também reduz custos e desperdícios.
Os efeitos da calibração também se refletem em conformidade com normas e certificações de qualidade. Muitas indústrias devem cumprir regulamentações rigorosas que exigem a calibração de equipamentos. Mantendo os instrumentos calibrados, as empresas podem garantir que estão em conformidade com esses padrões, evitando multas e possíveis sanções que podem impactar a reputação da marca.
Além disso, produtos que resultam de processos bem calibrados tendem a ter uma vida útil mais longa e desempenho mais confiável. Isso não apenas contribui para a satisfação do cliente, mas também reduz a necessidade de devoluções e trocas, melhorando a percepção da marca no mercado.
Finalmente, a calibração pode levar a inovações. Quando os processos são precisos, as organizações podem explorar novos métodos e abordagens para melhorar ainda mais a qualidade. A calibração regular dos equipamentos libera espaço para melhorias contínuas e a busca pela excelência na produção.
A calibração e manutenção de equipamentos são fundamentais para garantir a precisão, eficiência e qualidade dos produtos em diversas indústrias.
Através de processos de calibração adequados, é possível minimizar erros, prolongar a vida útil dos equipamentos e atender às exigências regulatórias.
Com as estratégias apresentadas, desde a escolha correta dos padrões de referência até a implementação de manutenção preventiva, as organizações podem não apenas otimizar suas operações, mas também aumentar a satisfação do cliente e a confiabilidade da marca.
Em um mercado cada vez mais competitivo, investir na calibração e manutenção de equipamentos é um passo essencial para garantir a excelência e a continuidade do sucesso empresarial.