Calibração de válvulas de segurança: Garantindo a Eficiência e Segurança
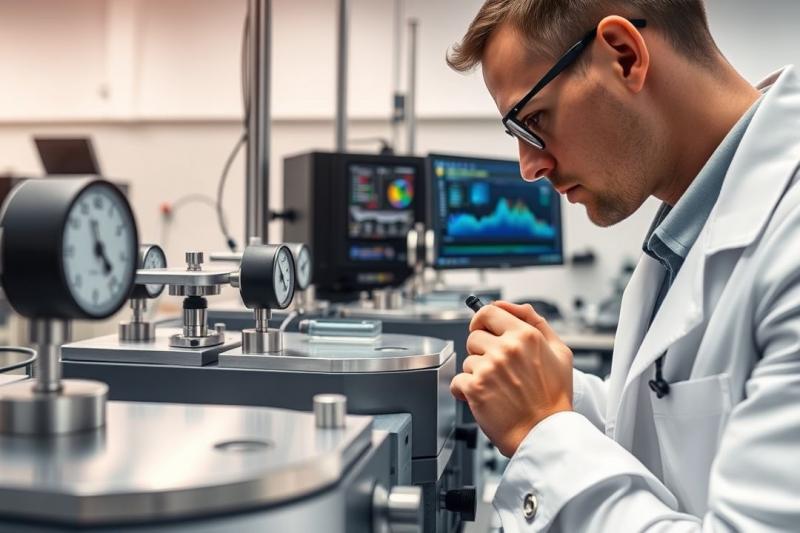
Por: Anderson - 20 de Março de 2025
A calibração de válvulas de segurança é um processo essencial para garantir a operação eficiente e segura de diversos sistemas industriais. Com o aumento da complexidade das operações industriais, a precisão na calibração dessas válvulas se tornou um fator crítico para a segurança e o desempenho das instalações.
Importância da calibração de válvulas de segurança na indústria
A calibração de válvulas de segurança desempenha um papel fundamental na operação de sistemas industriais, garantindo que esses dispositivos funcionem corretamente sob condições críticas. Essas válvulas são projetadas para proteger equipamentos e instalações, evitando sobrepressões que podem causar danos significativos e representar riscos à segurança dos trabalhadores.
Primeiramente, a calibração assegura que as válvulas abram e fechem nas pressões configuradas, evitando falhas que poderiam resultar em explosões ou vazamentos. A precisão na calibração é vital, pois uma válvula que não abre na pressão certa pode comprometer a integridade do sistema, levando a interrupções na produção e custos elevados em reparos e manutenção.
Além disso, a calibração regular das válvulas de segurança ajuda a atender aos requisitos de conformidade regulamentar. Muitas indústrias estão sujeitas a normativas rigorosas e padrões de segurança que exigem documentação de calibração. Garantir que as válvulas estejam calibradas não só contribui para a segurança, mas também evita possíveis penalizações e multas.
Outro aspecto importante é a eficiência operacional. Válvulas de segurança bem calibradas contribuem para um desempenho consistente e eficiente do sistema, minimizando desperdícios de energia e recursos. Isso pode resultar em uma queda de custos operacionais e um aumento na sustentabilidade da operação.
Por fim, a calibração das válvulas de segurança é um componente essencial da estratégia de manutenção preventiva. Realizar a calibração regular não apenas aumenta a vida útil do equipamento, mas também reduz a probabilidade de falhas catastróficas, garantindo um ambiente de trabalho mais seguro e produtivo. Portanto, investir na calibração efetiva das válvulas é um passo crucial na gestão da segurança industrial.
Como identificar a necessidade de calibração de válvulas
Identificar a necessidade de calibração de válvulas de segurança é um aspecto crucial para manter a eficácia e a segurança dos sistemas industriais. Existem vários sinais e fatores que podem indicar que uma válvula requer calibração, os quais abordaremos a seguir.
Um dos principais indicadores é a ocorrência de vazamentos ou falhas durante a operação da válvula. Se uma válvula de segurança estiver apresentando vazamentos quando deveria estar fechada ou se não abrir quando a pressão atinge o limite especificado, isso é um sinal claro de que a calibração é necessária.
Além disso, a análise de desempenho da válvula durante as inspeções regulares pode revelar a necessidade de calibração. Se a válvula não estiver respondendo de maneira consistente às mudanças de pressão, ou se houver variações significativas nos dados, isso requer atenção imediata para evitar problemas maiores.
Outros fatores como variações de temperatura, desgaste mecânico ou corrosão também podem afetar a calibração das válvulas. Se notar que as condições em que a válvula opera mudaram, vale a pena revisar sua calibração. A expectativa é que as válvulas sejam testadas regularmente para verificar se ainda estão dentro das especificações do fabricante.
Documentar qualquer alteração na operação da válvula ou em seu ambiente de trabalho é fundamental. Mudanças nas características do fluido, pressões operacionais ou ciclos de operação podem demandar ajustes na calibração. Além disso, as normas e regulamentações de segurança frequentemente exigem verificações automáticas ou auditorias periódicas visando garantir que todos os componentes, incluindo válvulas, estejam calibrados adequadamente.
Por fim, recomenda-se a implementação de um programa de manutenção preventiva que inclua testes de calibração em intervalos regulares, independentemente da observação de falhas. Isso não apenas assegura a segurança do sistema, mas também facilita a detecção precoce de problemas, minimizando riscos e custos com reparos a longo prazo.
Passos para realizar a calibração de válvulas de segurança
Realizar a calibração de válvulas de segurança é um processo que requer atenção aos detalhes e procedimentos precisos.
A seguir, apresentamos um passo a passo que pode ser seguido para garantir que as válvulas sejam calibradas corretamente.
1. Preparação e Planejamento: Antes de iniciar o processo de calibração, é essencial reunir todos os materiais e ferramentas necessários, como manômetros, chaves de fenda, suportes de teste e, se necessário, um registro adequado.
Além disso, consulte o manual do fabricante para entender as especificações e requisitos da válvula.
2. Desconexão do Sistema: O primeiro passo prático é desconectar a válvula de segurança do sistema.
Isso pode envolver a despressurização do sistema e a remoção da válvula.
É importante garantir que a linha esteja sem pressão antes de manusear qualquer componente.
3. Verificação Visual: Após a remoção, realize uma inspeção visual da válvula para verificar se há sinais de desgaste, corrosão ou deformações.
Isso pode afetar a eficácia da calibração.
Se você encontrar danos, considere substituir a válvula antes de calibrá-la.
4. Instalação do Equipamento de Teste: Instale um manômetro ou outro equipamento de teste na linha que permitirá medir a pressão quando a válvula for submetida à calibração.
Garanta que o equipamento esteja certificado e calibrado para garantir medições precisas.
5. Calibração da Válvula: Siga as especificações do fabricante para iniciar a calibração.
Aumente lentamente a pressão até o ponto de configuração da válvula, observando se ela abre e fecha conforme esperado.
Registre os valores de pressão em que a válvula abre e se ela mantém uma vedação adequada ao ser testada.
6. Ajustes Necessários: Se a válvula não abrir ou fechar na pressão correta, ajuste os pontos de calibração conforme as instruções do fabricante.
Isso geralmente envolve o uso de ferramentas específicas para ajustar a tensão do ressorte da válvula ou substituição de componentes internos, se necessário.
7. Testes Finais: Após realizar os ajustes, teste a válvula novamente para garantir que agora está operando nas especificações corretas.
Realize múltiplos testes ao longo do processo para assegurar a precisão.
8. Documentação: Após a calibração, é fundamental documentar o processo, incluindo todas as medições, ajustes feitos e qualquer observação relevante.
Isso é importante para a conformidade com normas de segurança e para futuras manutenções.
9. Reinstalação: Por fim, reinstale a válvula calibrada no sistema, garantindo que todas as conexões estejam seguras e que não existam vazamentos.
Faça uma última verificação para assegurar a integridade do sistema antes de reestabelecer a operação normal.
Esses passos são essenciais para garantir que a calibração das válvulas de segurança seja realizada de forma eficaz.
Manter um cronograma regular para a calibração não apenas garante a segurança, mas também melhora a confiabilidade do sistema operacional.
Fatores que influenciam a calibração de válvulas
A calibração de válvulas de segurança é influenciada por diversos fatores que podem impactar a eficiência e a precisão do funcionamento dessas válvulas. Compreender esses fatores é fundamental para garantir que a calibração seja realizada de forma adequada e eficaz. A seguir, discutimos os principais elementos que podem afetar a calibração de válvulas.
1. Temperatura: As variações de temperatura podem afetar o desempenho e a funcionalidade das válvulas de segurança. Propriedades materiais como expansão térmica podem alterar a pressão de funcionamento da válvula. Portanto, é vital considerar a temperatura operacional média ao calibrar o equipamento.
2. Pressão do Sistema: O nível de pressão presente no sistema onde a válvula opera também é um fator determinante. Válvulas calibradas em uma pressão específica podem não funcionar corretamente se a pressão do sistema mudar significativamente, exigindo reavaliação e possíveis ajustes na calibração.
3. Qualidade do Fluído: A natureza do fluído que passa pela válvula, seja líquido ou gás, pode impactar a calibração. Fluídos corrosivos, viscosos ou com aditivos podem causar desgaste nos componentes internos da válvula, afetando sua capacidade de abrir e fechar em pressões específicas. Análise regular da qualidade do fluído é recomendada para evitar problemas.
4. Desgaste e Corrosão: Com o tempo, as válvulas sofrem desgaste e corrosão devido à operação contínua e ao contato com diferentes fluídos. O desgaste pode resultar em folgas indesejadas ou falhas no fechamento, que impactam negativamente a calibração. Inspeções periódicas são essenciais para identificar e mitigar esses efeitos.
5. Ciclos de Operação: A quantidade de ciclos de abertura e fechamento que a válvula experimenta também pode influenciar sua calibração. Válvulas que são operadas com alta frequência podem sofrer desgastes mais rápidos e, portanto, exigem calibrações mais frequentes para manter sua integridade.
6. Condições Ambientais: Fatores ambientais, como umidade, presença de partículas no ar ou contaminação, podem comprometer o funcionamento da válvula. Sistemas instalados em ambientes adversos devem ser monitorados de perto, e a calibração deve ser ajustada com mais frequência se as condições de operação forem desfavoráveis.
7. Normas e Regulamentações: As exigências regulamentares e de segurança em diversas indústrias podem determinar a frequência e a forma da calibração. Normas específicas podem exigir que as válvulas sejam testadas e calibradas em intervalos determinados, o que deve ser levado em conta na programação da manutenção.
8. Instalação Correta: Uma instalação inadequada pode levar a problemas de calibração. É essencial que as válvulas sejam instaladas de acordo com as especificações do fabricante e atendendo às orientações de engenharia para garantir um funcionamento apropriado.
Entender todos esses fatores que influenciam a calibração das válvulas de segurança permite que os profissionais do setor desempenhem um papel ativo na manutenção e na eficiência dos sistemas. Implementar um plano de manutenção e calibração que considere esses elementos é crucial para a segurança e a operação eficaz de toda a instalação industrial.
Erros comuns na calibração e como evitá-los
A calibração de válvulas de segurança é um processo crítico que requer atenção meticulosa. No entanto, é comum que diversos erros ocorram durante esse procedimento, o que pode comprometer a segurança e a eficiência do sistema. Conhecer esses erros e adotar medidas para evitá-los é essencial. A seguir, apresentamos alguns dos erros mais frequentes na calibração de válvulas e dicas de como evitá-los.
1. Falta de Preparação: Um erro comum é não realizar uma preparação adequada antes da calibração. Isso pode incluir não reunir as ferramentas necessárias, não consultar o manual do fabricante ou não verificar a integridade da válvula. Para evitar isso, sempre planeje o processo com antecedência, garantindo que todas as ferramentas estejam disponíveis e que você tenha conhecimento suficiente sobre o equipamento.
2. Negligenciar a Inspeção Visual: Ignorar a inspeção visual da válvula antes da calibração pode resultar na perda de tempo e na realização de ajustes desnecessários. Inspecione a presença de corrosão, desgaste ou qualquer dano físico à válvula antes de iniciar a calibração. Isso ajuda a garantir que a válvula esteja em boas condições de funcionamento.
3. Não Realizar Testes em Diferentes Pressões: Um erro frequente é testar a válvula em apenas uma configuração de pressão, sem considerar as variações que possam ocorrer no sistema. É importante calibrar a válvula em várias pressões para garantir que ela funcione corretamente em diferentes condições. Realizar testes em faixas apropriadas aumenta a confiabilidade do sistema.
4. Não Documentar o Processo: Falhar em registrar os resultados da calibração, incluindo pressões de abertura e fechamento, pode levar à falta de histórico e problemas de conformidade no futuro. Sempre documente todos os resultados e ajustes feitos durante o processo de calibração, mantendo registros detalhados para referência futura.
5. Ignorar Sinais de Desgaste: É comum negligenciar os sinais de desgaste que podem afetar a calibração. Se a válvula mostra sinais de fadiga ou interferência, isso deve ser abordado antes da calibração. Fique atento a ruídos incomuns ou falhas intermitentes que podem indicar problemas que exigem manutenção ou substituição de peças.
6. Calibração Irregular: A falta de um cronograma de calibração regular pode fazer com que válvulas não sejam calibradas quando necessário, levando a falhas em momentos críticos. Estabeleça um cronograma de manutenção que inclua a calibração regular das válvulas, seguindo as recomendações do fabricante e as exigências da norma de segurança aplicável.
7. Confiar Apenas na Tecnologia: Embora o uso de tecnologia, como equipamentos de medição avançados, seja valioso, confiar somente nisso sem a supervisão de um profissional pode ser um erro. Assegure-se de que técnicos qualificados estejam monitorando o processo e verifiquem as medições, uma vez que a experiência prática é crucial para identificar problemas que podem não ser capturados por instrumentos.
Ao evitar esses erros comuns, você poderá garantir que a calibração das válvulas de segurança seja realizada de forma eficaz, mantendo a segurança e a eficiência do sistema industrial. A educação contínua da equipe e o comprometimento com a manutenção preventiva são fundamentais para o sucesso nesse processo.
Manutenção regular e periodicidade da calibração
A manutenção regular e a calibração periódica das válvulas de segurança são essenciais para garantir o funcionamento adequado e seguro das instalações industriais. Estabelecer uma rotina de manutenção não apenas previne falhas catastróficas, como também aumenta a vida útil dos equipamentos.
A seguir, discutimos a importância da manutenção regular e a periodicidade recomendada para a calibração das válvulas de segurança.
1. Importância da Manutenção Regular: A manutenção regular permite identificar e corrigir problemas nos equipamentos antes que se tornem sérios. Inspeções programadas ajudam a detectar sinais de desgaste e corrosão, garantindo que as válvulas estejam sempre em condições de operação seguras. Além disso, essas práticas ajudam a reduzir custos com reparos emergenciais e a minimizar interrupções na produção.
2. Estabelecimento de Cronogramas de Calibração: A periodicidade da calibração das válvulas de segurança deve estar alinhada às recomendações do fabricante e às normas de segurança aplicáveis. Embora não exista um prazo único para todas as condições, muitas indústrias seguem a regra de calibrar as válvulas anualmente. Em ambientes de operação mais agressiva ou em situações que envolvem altas pressões, a calibração pode ser necessária a cada seis meses ou até mesmo trimestralmente.
3. Fatores que Determinam a Frequência: Alguns fatores específicos influenciam a frequência da calibração, como a quantidade de ciclos de operação da válvula, as condições ambientais e a natureza do fluido que está sendo controlado. Em sistemas onde as válvulas operam em condições extremas de temperatura ou pressão, recomenda-se uma calibração mais frequente. Analise a aplicação e o desempenho histórico da válvula para determinar o melhor intervalo.
4. Registro das Atividades de Manutenção: Manter um registro detalhado das atividades de calibração e manutenção é crucial. Isso permite rastrear o desempenho ao longo do tempo e fornece dados valiosos para análises futuras. Além disso, os registros ajudam a garantir a conformidade com regulamentos de segurança e facilitam as auditorias.
5. Treinamento da Equipe: Ao implementar um cronograma de manutenção regular, é importante garantir que a equipe envolvida esteja bem treinada. Conhecimento sobre os procedimentos de calibração e identificação de sinais de problemas contribui para uma operação segura e eficiente. Programas de formação contínua devem ser oferecidos aos profissionais que realizam a calibração e manutenção.
Resumindo, a manutenção regular e a calibração periódica das válvulas de segurança são fundamentais para garantir a segurança e a eficácia operacional em ambientes industriais. Um cronograma claro, baseado em práticas recomendadas e na experiência operacional, assegura que os sistemas sejam confiáveis e que a segurança de todos os envolvidos seja mantida.
A calibração de válvulas de segurança é um aspecto fundamental para a segurança e eficiência em ambientes industriais. A compreensão da importância da calibração, a identificação dos fatores que influenciam esse processo e a conscientização sobre os erros comuns são essenciais para garantir que as válvulas funcionem corretamente.
Além disso, a implementação de uma rotina de manutenção regular e a definição de períodos adequados para a calibração contribuem para a longevidade do equipamento e a prevenção de falhas catastróficas. Investir em calibração e manutenção não é apenas uma questão de conformidade normativa, mas uma iniciativa que assegura a segurança dos trabalhadores e a integridade das operações industriais.