Calibração de Equipamentos de Medição para Garantir a Segurança do Trabalho
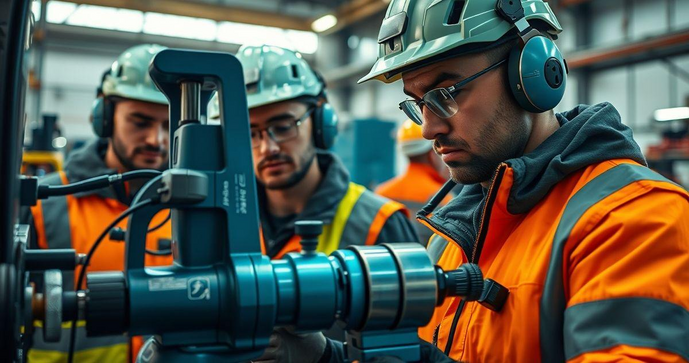
Por: Anderson - 20 de Fevereiro de 2025
A calibração de equipamentos de medição segurança do trabalho é um aspecto fundamental para garantir a precisão e a confiabilidade dos instrumentos utilizados em ambientes laborais. Equipamentos devidamente calibrados não apenas asseguram a qualidade dos processos, mas também protegem a saúde e a segurança dos trabalhadores. Neste artigo, abordaremos a importância da calibração, os procedimentos recomendados e as consequências da falta desse cuidado essencial.
Importância da Calibração de Equipamentos de Medição na Segurança do Trabalho
A calibração de equipamentos de medição segurança do trabalho é um processo crítico que garante a precisão e a confiabilidade dos instrumentos utilizados em diversas atividades laborais. A correta calibração não apenas assegura a qualidade dos resultados obtidos, mas também desempenha um papel vital na proteção da saúde e segurança dos trabalhadores. Neste contexto, é essencial entender por que a calibração é tão importante e como ela impacta diretamente a segurança no ambiente de trabalho.
Em primeiro lugar, a calibração é fundamental para garantir que os equipamentos de medição estejam funcionando dentro das especificações estabelecidas pelos fabricantes. Quando um equipamento não é calibrado corretamente, há um risco significativo de que os dados coletados sejam imprecisos. Isso pode levar a decisões erradas, que podem comprometer a segurança dos trabalhadores. Por exemplo, em indústrias onde a medição de gases tóxicos é necessária, um sensor mal calibrado pode não detectar níveis perigosos, colocando em risco a vida dos funcionários.
Além disso, a calibração regular dos equipamentos de medição é uma exigência legal em muitos setores. Normas e regulamentos de segurança do trabalho, como os estabelecidos pela Norma Regulamentadora NR-13, exigem que os equipamentos de medição sejam mantidos em conformidade com padrões específicos. O não cumprimento dessas normas pode resultar em penalidades severas, além de aumentar o risco de acidentes. Portanto, a calibração não é apenas uma prática recomendada, mas uma obrigação legal que deve ser respeitada por todas as empresas.
Outro aspecto importante a ser considerado é que a calibração contribui para a eficiência operacional. Equipamentos de medição que funcionam corretamente ajudam a otimizar processos, reduzindo desperdícios e melhorando a produtividade. Por exemplo, em uma linha de produção, a medição precisa de temperatura e pressão é crucial para garantir que os produtos sejam fabricados dentro das especificações. Se os equipamentos não estiverem calibrados, isso pode resultar em produtos defeituosos, que não atendem aos padrões de qualidade, levando a retrabalhos e perdas financeiras.
Além disso, a calibração de equipamentos de medição é essencial para a manutenção da confiança dos trabalhadores e da gestão em relação aos processos de segurança. Quando os colaboradores sabem que os equipamentos estão sendo calibrados regularmente, eles se sentem mais seguros em suas funções. Isso não apenas melhora a moral da equipe, mas também promove uma cultura de segurança dentro da organização. A confiança nos equipamentos de medição é um fator motivador que pode impactar positivamente a produtividade e a satisfação no trabalho.
É importante ressaltar que a calibração deve ser realizada por profissionais qualificados e com equipamentos adequados. A falta de conhecimento técnico pode resultar em calibrações inadequadas, que podem, por sua vez, comprometer a segurança. Portanto, as empresas devem investir em treinamentos e na contratação de serviços especializados para garantir que a calibração seja feita de maneira correta e eficiente.
Além disso, a calibração deve ser parte de um programa de manutenção preventiva mais amplo. Isso inclui a manutenção de redutor e outros componentes que podem afetar o desempenho dos equipamentos de medição. A integração de diferentes práticas de manutenção ajuda a garantir que todos os aspectos do sistema estejam funcionando em harmonia, minimizando o risco de falhas e acidentes.
Por fim, a calibração de equipamentos de medição segurança do trabalho é um investimento que traz retornos significativos em termos de segurança, eficiência e conformidade legal. As empresas que priorizam a calibração não apenas protegem seus trabalhadores, mas também melhoram sua reputação e competitividade no mercado. Em um mundo onde a segurança no trabalho é cada vez mais valorizada, a calibração se torna uma prática indispensável para qualquer organização que deseja operar de maneira responsável e eficaz.
Em resumo, a calibração de equipamentos de medição é um elemento essencial para garantir a segurança no trabalho. Ela assegura a precisão dos dados, cumpre com as exigências legais, melhora a eficiência operacional e fortalece a confiança dos trabalhadores. Portanto, as empresas devem adotar uma abordagem proativa em relação à calibração, investindo em processos e treinamentos que garantam a segurança e a qualidade em suas operações.
Procedimentos para Calibração Eficiente de Equipamentos
A calibração de equipamentos de medição é um processo essencial para garantir a precisão e a confiabilidade dos instrumentos utilizados em diversas aplicações. Para que a calibração seja eficiente, é necessário seguir uma série de procedimentos que assegurem resultados consistentes e confiáveis. Neste artigo, abordaremos os principais passos e considerações para realizar uma calibração eficaz, contribuindo para a segurança e a qualidade no ambiente de trabalho.
O primeiro passo para uma calibração eficiente é a preparação adequada do ambiente onde o processo será realizado. É fundamental que o local esteja limpo, organizado e livre de interferências externas que possam afetar os resultados. Fatores como temperatura, umidade e vibrações podem influenciar a precisão dos equipamentos de medição. Portanto, é recomendável realizar a calibração em um ambiente controlado, onde as condições possam ser monitoradas e mantidas dentro dos parâmetros ideais.
Após garantir um ambiente adequado, o próximo passo é reunir todos os equipamentos e ferramentas necessárias para a calibração. Isso inclui não apenas o equipamento a ser calibrado, mas também instrumentos de referência que serão utilizados como padrão durante o processo. A escolha de instrumentos de referência de alta precisão é crucial, pois eles servirão como base para comparar e ajustar os resultados do equipamento em calibração.
Antes de iniciar a calibração, é importante revisar o manual do fabricante do equipamento. O manual geralmente contém informações valiosas sobre os procedimentos específicos de calibração, incluindo os pontos de ajuste e as tolerâncias permitidas. Seguir as recomendações do fabricante é essencial para garantir que a calibração seja realizada de acordo com as especificações corretas, evitando danos ao equipamento e assegurando resultados precisos.
Uma vez que todas as preparações estejam concluídas, o processo de calibração pode ser iniciado. O primeiro passo é realizar uma verificação inicial do equipamento, que envolve a medição de valores conhecidos e a comparação com os resultados obtidos. Essa etapa é fundamental para identificar se o equipamento está fora de especificação e, se necessário, determinar a magnitude do ajuste que precisa ser feito.
Durante a calibração, é importante realizar medições em diferentes pontos de operação do equipamento. Isso significa que, em vez de calibrar apenas em um único ponto, o operador deve testar o equipamento em toda a sua faixa de operação. Essa abordagem ajuda a identificar não apenas desvios em pontos específicos, mas também a garantir que o equipamento funcione corretamente em toda a sua capacidade. A coleta de dados em múltiplos pontos também permite uma análise mais abrangente do desempenho do equipamento.
Após realizar as medições, o próximo passo é ajustar o equipamento conforme necessário. Isso pode envolver a modificação de configurações, a troca de componentes ou a aplicação de correções. É importante documentar todos os ajustes realizados, bem como os resultados obtidos antes e depois da calibração. Essa documentação é essencial para garantir a rastreabilidade e a conformidade com as normas de qualidade e segurança.
Além disso, a calibração deve ser realizada por profissionais qualificados e treinados. A falta de conhecimento técnico pode resultar em calibrações inadequadas, que podem comprometer a segurança e a precisão dos equipamentos. Portanto, as empresas devem investir em treinamentos e na contratação de serviços especializados para garantir que a calibração seja feita de maneira correta e eficiente.
Outro aspecto importante a ser considerado é a manutenção contínua dos equipamentos. A calibração não deve ser vista como um evento isolado, mas sim como parte de um programa de manutenção preventiva mais amplo. Isso inclui a manutenção em redutores e outros componentes que podem afetar o desempenho dos equipamentos de medição. A integração de diferentes práticas de manutenção ajuda a garantir que todos os aspectos do sistema estejam funcionando em harmonia, minimizando o risco de falhas e acidentes.
Após a calibração, é fundamental realizar testes de verificação para garantir que o equipamento esteja operando dentro das especificações desejadas. Esses testes devem ser realizados em condições semelhantes às que o equipamento enfrentará em sua aplicação real. Isso ajuda a validar a eficácia da calibração e a garantir que o equipamento esteja pronto para uso.
Por fim, a calibração deve ser realizada em intervalos regulares, conforme recomendado pelo fabricante ou pelas normas aplicáveis. A frequência da calibração pode variar dependendo do tipo de equipamento, da intensidade de uso e das condições ambientais. Manter um cronograma de calibração ajuda a garantir que os equipamentos permaneçam precisos e confiáveis ao longo do tempo.
Em resumo, os procedimentos para calibração eficiente de equipamentos envolvem uma série de etapas que garantem a precisão e a confiabilidade dos instrumentos. Desde a preparação do ambiente até a documentação dos resultados, cada passo é crucial para assegurar que a calibração seja realizada de maneira eficaz. Investir em calibração e manutenção contínua é essencial para garantir a segurança e a qualidade no ambiente de trabalho, contribuindo para a proteção dos trabalhadores e a eficiência operacional das empresas.
Frequência Recomendada para Calibração de Equipamentos de Medição
A calibração de equipamentos de medição é um processo essencial para garantir a precisão e a confiabilidade dos instrumentos utilizados em diversas aplicações. No entanto, a eficácia da calibração não depende apenas da qualidade do processo em si, mas também da frequência com que é realizada. Neste artigo, discutiremos a frequência recomendada para a calibração de equipamentos de medição, considerando fatores que influenciam essa periodicidade e a importância de manter um cronograma adequado.
Em primeiro lugar, é importante entender que a frequência de calibração pode variar significativamente dependendo do tipo de equipamento, da aplicação e das condições em que ele é utilizado. Equipamentos que operam em ambientes rigorosos ou que estão sujeitos a condições adversas, como temperaturas extremas, umidade elevada ou vibrações, podem exigir calibrações mais frequentes. Por outro lado, equipamentos que são utilizados em condições controladas e que não sofrem desgaste significativo podem ter intervalos de calibração mais longos.
Uma prática comum é seguir as recomendações do fabricante do equipamento. Os manuais de operação geralmente incluem diretrizes sobre a frequência de calibração, com base em testes e análises realizadas pelos fabricantes. Essas recomendações são valiosas, pois levam em consideração as especificidades do equipamento e as condições de uso. Portanto, é fundamental que as empresas consultem os manuais e sigam as orientações fornecidas pelos fabricantes para garantir a precisão e a confiabilidade dos instrumentos.
Além das recomendações do fabricante, as normas e regulamentos aplicáveis também desempenham um papel importante na determinação da frequência de calibração. Em muitos setores, como o farmacêutico, alimentício e de saúde, existem normas rigorosas que exigem calibrações regulares para garantir a conformidade com os padrões de qualidade e segurança. Por exemplo, a calibração de equipamentos laboratoriais é frequentemente regulamentada por normas que estabelecem a frequência mínima para garantir a precisão dos resultados obtidos em análises e testes.
Outro fator a ser considerado é a intensidade de uso do equipamento. Equipamentos que são utilizados com frequência ou que estão sujeitos a ciclos de operação intensos podem exigir calibrações mais frequentes. Por exemplo, em uma linha de produção onde instrumentos de medição são utilizados continuamente, a calibração pode ser necessária a cada mês ou até mesmo semanalmente, dependendo da criticidade das medições. Em contrapartida, equipamentos que são utilizados esporadicamente podem ter intervalos de calibração mais longos, como trimestrais ou semestrais.
Além disso, a experiência e o histórico de desempenho do equipamento também podem influenciar a frequência de calibração. Se um equipamento apresentar desvios frequentes ou inconsistências nas medições, pode ser um sinal de que a calibração deve ser realizada com mais regularidade. Monitorar o desempenho dos equipamentos e registrar os resultados das calibrações anteriores pode ajudar a identificar padrões e determinar a frequência ideal para cada instrumento.
É importante ressaltar que a calibração não deve ser vista como um evento isolado, mas sim como parte de um programa de manutenção preventiva mais amplo. A manutenção regular dos equipamentos, incluindo inspeções e ajustes, pode ajudar a prolongar a vida útil dos instrumentos e a garantir que eles permaneçam precisos ao longo do tempo. Portanto, as empresas devem adotar uma abordagem proativa em relação à calibração e à manutenção, estabelecendo um cronograma que leve em consideração todos os fatores mencionados.
Além disso, a documentação adequada das calibrações realizadas é essencial para garantir a rastreabilidade e a conformidade com as normas aplicáveis. Manter registros detalhados das calibrações, incluindo datas, resultados e ajustes realizados, ajuda a monitorar a frequência e a eficácia do processo. Essa documentação também pode ser útil em auditorias e inspeções, demonstrando que a empresa está comprometida com a qualidade e a segurança.
Por fim, a frequência recomendada para calibração de equipamentos de medição deve ser determinada com base em uma combinação de fatores, incluindo as recomendações do fabricante, as normas aplicáveis, a intensidade de uso e o histórico de desempenho do equipamento. Ao estabelecer um cronograma de calibração adequado, as empresas podem garantir a precisão e a confiabilidade dos instrumentos, contribuindo para a segurança e a qualidade em suas operações.
Em resumo, a calibração de equipamentos de medição é um processo crítico que deve ser realizado com a frequência adequada para garantir resultados precisos e confiáveis. Seguir as recomendações do fabricante, considerar as condições de uso e monitorar o desempenho dos equipamentos são práticas essenciais para manter a eficácia da calibração e assegurar a conformidade com as normas de qualidade e segurança.
Consequências da Falta de Calibração na Segurança do Trabalho
A calibração de equipamentos de medição é um aspecto crucial para garantir a segurança no ambiente de trabalho. A falta de calibração pode levar a uma série de consequências negativas que não apenas comprometem a precisão dos dados, mas também colocam em risco a saúde e a segurança dos trabalhadores. Neste artigo, discutiremos as principais consequências da falta de calibração e como isso pode impactar a segurança do trabalho.
Uma das consequências mais imediatas da falta de calibração é a imprecisão nas medições. Equipamentos que não são calibrados regularmente podem apresentar desvios significativos em suas leituras, resultando em dados incorretos. Por exemplo, um termômetro industrial digital que não foi calibrado pode indicar temperaturas erradas, levando a decisões inadequadas em processos críticos, como a produção de alimentos ou a manipulação de substâncias químicas. Essa imprecisão pode resultar em produtos defeituosos, desperdício de materiais e até mesmo em situações perigosas que podem afetar a saúde dos trabalhadores.
Além disso, a falta de calibração pode resultar em não conformidade com normas e regulamentos de segurança. Muitas indústrias são obrigadas a seguir normas rigorosas que exigem a calibração regular de equipamentos de medição. O não cumprimento dessas normas pode levar a penalidades legais, multas e até mesmo à suspensão das operações. Isso não apenas afeta a reputação da empresa, mas também pode resultar em custos financeiros significativos e perda de confiança por parte dos clientes e parceiros comerciais.
Outro aspecto importante a ser considerado é que a falta de calibração pode aumentar o risco de acidentes de trabalho. Equipamentos de medição imprecisos podem levar a decisões erradas que comprometem a segurança dos trabalhadores. Por exemplo, em ambientes onde a medição de gases tóxicos é necessária, um sensor mal calibrado pode não detectar níveis perigosos, colocando em risco a vida dos funcionários. A falta de calibração pode, portanto, resultar em acidentes graves, lesões e até fatalidades.
Além dos riscos diretos à segurança, a falta de calibração também pode impactar a eficiência operacional. Equipamentos que não estão funcionando corretamente podem levar a interrupções na produção, retrabalhos e aumento dos custos operacionais. Isso pode afetar a produtividade da equipe e a capacidade da empresa de atender às demandas do mercado. A ineficiência resultante da falta de calibração pode, portanto, ter um efeito cascata que prejudica não apenas a segurança, mas também a viabilidade econômica da empresa.
Outro ponto a ser destacado é que a falta de calibração pode afetar a moral dos trabalhadores. Quando os funcionários percebem que os equipamentos que utilizam não estão sendo mantidos adequadamente, isso pode gerar desconfiança e insegurança em relação ao ambiente de trabalho. A falta de confiança nos instrumentos de medição pode levar a um aumento do estresse e da insatisfação no trabalho, impactando negativamente a produtividade e a saúde mental dos colaboradores.
Além disso, a falta de calibração pode resultar em custos adicionais a longo prazo. Embora a calibração regular possa parecer um custo a mais no curto prazo, a falta dela pode levar a problemas muito mais caros no futuro. Equipamentos que não são calibrados podem sofrer desgastes mais rápidos, resultando em necessidade de reparos ou substituições frequentes. Isso pode aumentar os custos operacionais e afetar o orçamento da empresa.
Por fim, a falta de calibração pode comprometer a qualidade dos produtos e serviços oferecidos pela empresa. Em setores onde a precisão é fundamental, como na indústria farmacêutica ou alimentícia, a falta de calibração pode resultar em produtos que não atendem aos padrões de qualidade. Isso pode levar a recalls, reclamações de clientes e danos à reputação da marca. A qualidade dos produtos é um fator crítico para a satisfação do cliente e a sustentabilidade do negócio.
Em resumo, as consequências da falta de calibração na segurança do trabalho são significativas e abrangem desde a imprecisão nas medições até o aumento do risco de acidentes e a não conformidade com normas de segurança. A calibração regular é essencial para garantir a precisão dos dados, a segurança dos trabalhadores e a eficiência operacional. Portanto, as empresas devem adotar uma abordagem proativa em relação à calibração, investindo em processos e treinamentos que garantam a segurança e a qualidade em suas operações.
Em conclusão, a calibração de equipamentos de medição é um elemento crucial para a segurança do trabalho e a eficiência operacional. Através de práticas adequadas de calibração, as empresas podem garantir a precisão dos dados, cumprir com as normas de segurança e proteger a saúde dos trabalhadores. Ignorar a calibração pode resultar em consequências graves, incluindo acidentes, não conformidade legal e impactos negativos na qualidade dos produtos. Portanto, é essencial que as organizações adotem uma abordagem proativa em relação à calibração, implementando procedimentos regulares e investindo na formação de seus colaboradores. Dessa forma, será possível criar um ambiente de trabalho mais seguro e produtivo, beneficiando tanto os trabalhadores quanto a empresa como um todo.