Calibração de instrumentos de pressão e sua importância para a precisão
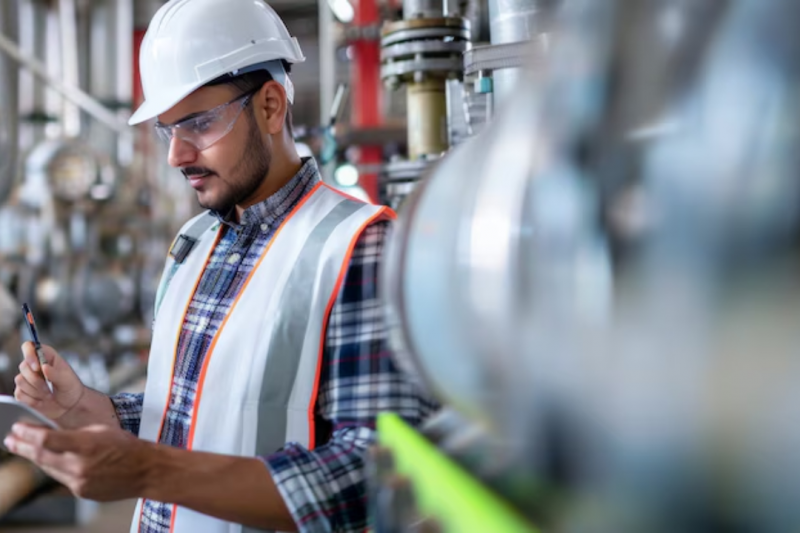
Por: Anderson - 20 de Junho de 2025
A calibração de instrumentos de pressão é um procedimento crucial na indústria. Esse processo assegura que os equipamentos de medição estejam funcionando corretamente e fornecendo dados precisos. Com o aumento da exigência por precisão em diversos campos, a calibração se torna essencial para manter a qualidade e a segurança dos processos industriais.
Entendendo a calibração de instrumentos de pressão
A calibração de instrumentos de pressão é um processo sistemático que visa garantir a precisão das medições realizadas por esses dispositivos. Para entender melhor, é fundamental saber que cada instrumento de pressão possui uma escala de medição, que deve ser verificada contra padrões conhecidos e aceitos.
O procedimento de calibração envolve a comparação do instrumento em questão com um padrão de referência, que possui uma precisão verificada e certificada. Essa comparação é essencial, pois permite identificar desvios que podem ocorrer durante as medições e, assim, ajustar o instrumento para garantir resultados corretos.
Um dos principais objetivos da calibração é minimizar erros de medição que podem impactar na qualidade do produto final, segurança e conformidade regulatória. Instrumentos que não estão devidamente calibrados podem levar a decisões incorretas, resultando em perdas significativas para empresas.
A calibração deve ser realizada de acordo com normas técnicas reconhecidas, como as da ISO (Organização Internacional de Normalização), que oferecem diretrizes essenciais para o processo. As frequências de calibração podem variar conforme o tipo de instrumento, sua utilização e o ambiente em que está inserido, sendo comum realizar calibrações periodicamente, especialmente em setores regulamentados.
Finalmente, é importante que toda calibração seja devidamente documentada. Registros detalhados ajudam a garantir a rastreabilidade e a conformidade com as exigências normativas, além de fornecer uma base para futuras avaliações e calibrações.
Principais tipos de instrumentos de pressão e seus usos
Os instrumentos de pressão são fundamentais em diversas aplicações industriais e de laboratório, pois possibilitam a medição precisa da pressão em diferentes sistemas. Cada tipo de instrumento tem características específicas que o tornam adequado para usos distintos. Abaixo, apresentamos os principais tipos de instrumentos de pressão e suas respectivas aplicações.
1. Manômetros: Estes são os instrumentos mais comuns de medição de pressão. Eles podem ser analógicos, com mostradores de ponteiro, ou digitais, com leituras eletrônicas. São amplamente utilizados em aplicações industriais, como no controle de sistemas de água e ar comprimido.
2. Transdutores de pressão: Usados para converter pressão em um sinal elétrico, os transdutores são essenciais em ambientes automatizados e paleoliticos que requerem monitoramento contínuo. Eles apresentam alta precisão e resposta rápida, sendo comuns em aplicações de processos químicos e de petróleo.
3. Pressostatos: Esses dispositivos não apenas medem a pressão, mas também controlam sistemas baseados em valores de pressão predefinidos. Os pressostatos são amplamente usados em sistemas de segurança e automação industrial, acionando alarmes ou desligando máquinas quando a pressão atinge limites críticos.
4. Manômetros de diferenciais: Estes instrumentos medem a diferença de pressão entre dois pontos e são comuns em aplicações de filtragem e ventilação. Eles ajudam a monitorar a obstrução de filtros industriais e ar condicionado.
5. Manômetros digitais: Equipados com tecnologia avançada, os manômetros digitais oferecem funcionalidades adicionais, como registro de dados, conectividade e medição em diferentes unidades. São utilizados em pesquisa científica, na indústria alimentícia e farmacêutica, onde a precisão é crítica.
6. Transmissores de pressão: Semelhantes aos transdutores, mas com uma precisão ainda maior, os transmissores são utilizados para medições em larga escala e podem monitorar pressão em grandes tanques ou sistemas hidráulicos industriais.
Em resumo, a escolha do instrumento de pressão adequado depende das especificidades do processo, do ambiente de operação e da necessidade de precisão. A compreensão das características de cada tipo de instrumento permite que profissionais realizem medições confiáveis e seguras em suas operações diárias.
Processo de calibração: etapas e cuidados
O processo de calibração de instrumentos de pressão envolve várias etapas cruciais que garantem a precisão e confiabilidade das medições.
Aqui estão as principais etapas e cuidados a serem considerados durante a calibração:
1. Preparação do Instrumento: Antes de iniciar a calibração, é necessário preparar o instrumento.
Isso inclui a limpeza de todas as partes, verificação visual para possíveis danos e análise do estado geral do equipamento.
É essencial garantir que o instrumento esteja em boas condições para uma calibração precisa.
2. Escolha do Padrão de Referência: Um padrão de referência, que é um instrumento de medição cuja precisão foi verificada e certificada, deve ser escolhido com base na faixa de medição do instrumento a ser calibrado.
O padrão deve ser adequado e estar na mesma unidade de medida que o instrumento em calibração.
3. Estabelecimento das Condições de Calibração: As condições de temperatura e pressão durante a calibração devem ser as mesmas que as condições em que o instrumento será utilizado.
Isso ajuda a garantir que os resultados sejam relevantes e aplicáveis ao ambiente real de operação.
4. Execução da Calibração: A calibração propriamente dita consiste em comparar as leituras do instrumento sob teste com as do padrão de referência.
Isso geralmente é feito em vários pontos ao longo da faixa de medição, permitindo a construção de uma curva de calibração.
Qualquer desvio deve ser registrado e corrigido, ajustando o instrumento conforme necessário.
5. Registro dos Dados: Todos os dados obtidos durante a calibração devem ser documentados de forma clara e precisa.
Essas informações incluem os valores de medição, a data da calibração, o nome do operador e quaisquer observações relevantes.
Um registro completo é essencial para futura referência e rastreabilidade.
6. Verificação e Validação: Após a calibração, é importante realizar uma verificação final para garantir que o instrumento funcione corretamente.
Isso pode incluir uma reavaliação de suas leituras em condições de operação simuladas.
A validação final confirma que o instrumento está pronto para o uso.
7. Programação de Manutenção Regular: A calibração não deve ser considerada um evento único.
É fundamental estabelecer um cronograma de calibração regular com base nas recomendações do fabricante e no uso do instrumento.
A manutenção preventiva garantirá a continuidade da precisão ao longo do tempo.
Seguir essas etapas e prestar atenção em cada detalhe do processo de calibração ajuda a garantir que os instrumentos de pressão ofereçam medições precisas e confiáveis, além de atender às normas e regulamentações aplicáveis.
Importância da calibração regular para a segurança industrial
A calibração regular de instrumentos de pressão é uma prática essencial para garantir a segurança industrial. Essa importância se reflete em vários aspectos críticos que afetam tanto a operação das indústrias quanto a segurança dos funcionários. A seguir, discutimos algumas das razões pelas quais a calibração regular é imprescindível.
1. Precisão nas Medidas: Instrumentos de pressão que não são calibrados periodicamente podem apresentar desvios que comprometem a precisão das medições. Esses desvios podem levar a erros na operação de equipamentos, resultando em falhas mecânicas ou operação inadequada, o que poderia causar acidentes graves.
2. Conformidade Regulatória: Muitas indústrias estão sujeitas a regulamentações rigorosas que exigem calibração regular dos instrumentos de medição. O não cumprimento dessas normas pode resultar em penalidades, multas e até mesmo a suspensão das operações. Manter a calibração em dia assegura que a empresa esteja de acordo com as legislações pertinentes.
3. Segurança dos Funcionários: Equipamentos de pressão não calibrados podem representar riscos significativos para quem trabalha nas instalações industriais. Desvios nas medições podem resultar em situações perigosas, como explosões ou vazamentos de substâncias químicas. A calibração regular minimiza esses riscos, contribuindo para um ambiente de trabalho mais seguro.
4. Controle de Processo: A eficácia na produção e controle de qualidade depende fortemente das medições precisas de pressão. A calibração regular assegura que os processos operacionais estejam funcionando dentro dos parâmetros especificados, aumentando a eficiência e reduzindo a quantidade de produtos defeituosos.
5. Confiança em Dados e Relatórios: Medições precisas são fundamentais para auditorias internas e externas. A calibração regular fornece dados confiáveis que podem ser utilizados para análises de desempenho e relatórios de conformidade, o que aumenta a confiança nas informações divulgadas pela empresa.
6. Redução de Custos: Embora a calibração regular envolva um investimento, a longo prazo, ela pode resultar em economias significativas. A prevenção de falhas de equipamentos, retrabalho e desperdício de produtos resulta em uma operação mais econômica. Além disso, a redução de acidentes pode evitar custos associados a licenças médicas e seguro.
Em resumo, a calibração regular dos instrumentos de pressão é uma prática vital que influencia diretamente a segurança, eficiência e reputação das operações industriais. Investir em calibração não é apenas uma questão de conformidade; é um passo fundamental para garantir a segurança do ambiente de trabalho e a qualidade dos processos industriais.
Erros comuns na calibração de instrumentos de pressão
Identificar e evitar erros comuns durante a calibração de instrumentos de pressão é crucial para garantir a precisão e a confiabilidade das medições.
Abaixo estão alguns dos erros mais frequentes que podem ocorrer durante esse processo, juntamente com sugestões para evitá-los.
1. Falta de Preparação do Instrumento: Um erro comum é não realizar uma inspeção pré-calibração adequada.
Instrumentos sujos ou danificados podem fornecer leituras incorretas.
Antes da calibração, é fundamental garantir que o instrumento esteja limpo, em boas condições e devidamente ajustado conforme as especificações do fabricante.
2. Escolha Inadequada de Padrões de Referência: Usar um padrão de referência que não esteja adequado para a faixa de medição do instrumento a ser calibrado pode levar a desvios significativos.
É importante garantir que o padrão de calibração tenha uma precisão certificada e esteja dentro do mesmo intervalo de medição do instrumento em questão.
3. Ignorar as Condições Ambientais: As condições de temperatura e pressão podem afetar as medições.
Não controlar e registrar as condições ambientais durante a calibração pode resultar em resultados imprecisos.
Sempre ajuste e documente as condições de calibração para refletir o ambiente de operação do instrumento.
4. Falhas na Documentação: A falta de documentação completa dos dados de calibração é um erro crítico.
Sem registros adequados, não é possível rastrear as alterações ou identificar problemas de desempenho ao longo do tempo.
É imprescindível manter uma documentação clara e organizada de todo o processo de calibração.
5. Não Seguir Procedimentos Padrão: Ignorar procedimentos operacionais padrão durante o processo de calibração pode resultar em erros.
É fundamental seguir rigorosamente as diretrizes e protocolos estabelecidos, conforme indicado pelos fabricantes e normas técnicas, para garantir que cada etapa da calibração seja realizada corretamente.
6. Falta de Treinamento Adequado: A calibração deve ser conduzida por profissional qualificado e treinado.
A falta de conhecimento adequado sobre os instrumentos e os processos de calibração pode levar a erros significativos.
A capacitação regular da equipe envolvida na calibração é essencial para assegurar a precisão e a confiabilidade das medições.
7. Agendamento Irregular de Calibração: A calibração esporádica pode resultar em desvios mais acentuados.
É importante estabelecer e cumprir um cronograma regular de calibração para todos os instrumentos, de acordo com as diretrizes do fabricante e as normas regulatórias, para garantir medições consistentes e precisas.
Ao estar ciente desses erros comuns, as empresas podem implementar práticas adequadas para evitá-los, garantindo que a calibração de instrumentos de pressão seja uma tarefa eficiente e eficaz.
Isso resultará em medições mais precisas, maior segurança e melhor desempenho operacional.
Como escolher um laboratório de calibração confiável
A escolha de um laboratório de calibração confiável é um passo crucial para garantir a precisão das medições dos instrumentos de pressão. Aqui estão algumas diretrizes que podem ajudar na seleção de um laboratório adequado:
1. Certificações e Acreditações: Verifique se o laboratório possui certificações reconhecidas, como a ISO/IEC 17025. Essa norma garante que o laboratório opera dentro de padrões de qualidade e competência técnica. Laboratórios acreditados são frequentemente submetidos a auditorias para assegurar a conformidade com os requisitos estabelecidos.
2. Experiência e Reputação: Considere a experiência do laboratório na calibração de instrumentos similares aos seus. Opte por laboratórios com um histórico comprovado na indústria, bem como referências e avaliações positivas de clientes. Um laboratório bem avaliado tende a fornecer serviços de maior qualidade.
3. Equipamentos e Tecnologia: A qualidade dos serviços de calibração depende dos equipamentos e tecnologias utilizados pelo laboratório. Certifique-se de que o laboratório possui instrumentos de calibração atualizados e que utiliza tecnologias avançadas. Isso garantirá medições mais precisas e confiáveis.
4. Serviços Oferecidos: Verifique a gama de serviços que o laboratório oferece. Além da calibração, é interessante que o laboratório forneça serviços adicionais, como manutenção, reparo e consultoria técnica. Isso pode facilitar a relação comercial e atender melhor às suas necessidades.
5. Documentação e Relatórios: Um bom laboratório deve fornecer documentação clara e detalhada de cada calibração realizada. Isso inclui certificados, registros de medições e relatórios sobre as condições operacionais durante a calibração. A transparência na documentação é fundamental para a rastreabilidade e análise futura.
6. Localização e Logística: A proximidade do laboratório pode facilitar o transporte de instrumentos para calibração. No entanto, se a distância for um fator, avalie a logística de envio e entrega. Certifique-se de que o laboratório possui um sistema confiável para a manipulação e transporte seguro dos equipamentos.
7. Suporte ao Cliente: Um suporte ao cliente eficaz é essencial para resolver problemas e responder a dúvidas. Considere se o laboratório oferece um canal de comunicação acessível e como é o atendimento ao cliente. Um bom atendimento pode fazer a diferença na relação a longo prazo.
8. Custo: Embora o preço não deva ser o único critério na escolha do laboratório, é importante entender a estrutura de preços e garantir que os serviços oferecidos sejam competitivos. Compare orçamentos de diferentes laboratórios, mas sempre priorizando a qualidade e a confiabilidade dos serviços.
Ao seguir essas diretrizes, você poderá escolher um laboratório de calibração confiável que atenda às suas necessidades e assegure a precisão necessária em suas operações. Um bom parceiro de calibração é essencial para a manutenção da qualidade e segurança dos seus processos industriais.
A calibração de instrumentos de pressão é um aspecto estratégico que não pode ser negligenciado em ambientes industriais e laboratoriais. A precisão nas medições não apenas assegura a conformidade com normas e regulamentos, mas também promove a segurança dos colaboradores e a qualidade dos produtos.
Ao compreender a importância da calibração regular, os processos associados e as melhores práticas para evitar erros, é possível maximizar a eficiência operacional e minimizar riscos. Além disso, a escolha de um laboratório de calibração confiável é fundamental para garantir resultados consistentes e confiáveis.
Investir na calibração adequada dos instrumentos não é apenas uma escolha inteligente; é um passo essencial para garantir o sucesso e a sustentabilidade das operações.