Como Garantir a Precisão com a Calibração de Equipamentos de Medição
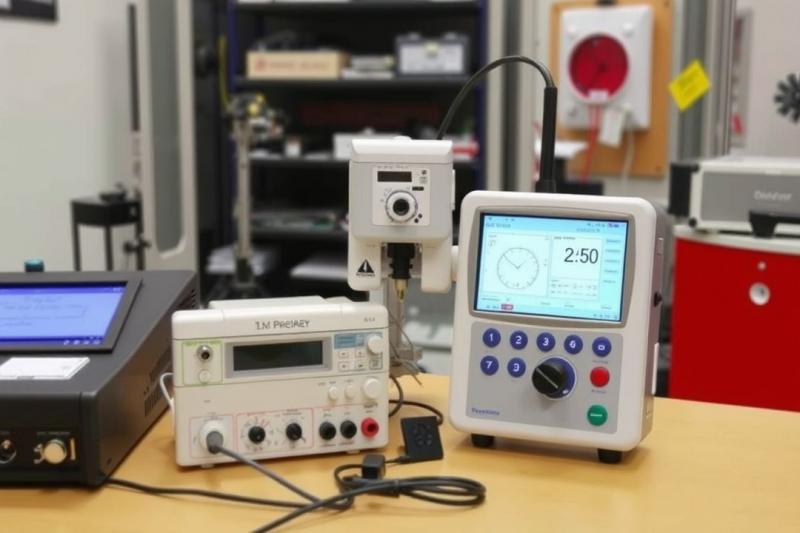
Por: Anderson - 23 de Junho de 2025
A calibração de equipamentos de medição desempenha um papel crucial na precisão dos resultados obtidos em diversas indústrias. Este processo visa garantir que os instrumentos de medição operem dentro de especificações definidas, crucial para assegurar a qualidade e a confiabilidade dos dados. Neste contexto, é fundamental entender a importância da calibração e os métodos adequados para implementá-la.
Importância da Calibração na Medição de Equipamentos
A calibração de equipamentos de medição é uma prática fundamental para garantir a precisão e a confiabilidade dos resultados obtidos. Com o avanço das tecnologias e das indústrias, a demanda por medições exatas aumentou significativamente, tornando a calibração um aspecto essencial na qualidade dos processos produtivos.
Primeiramente, a calibração assegura que os instrumentos estejam medindo com exatidão, minimizando erros que poderiam levar a conclusões erradas ou a falhas em processos. Por exemplo, em setores como farmacêutico e alimentício, uma medição imprecisa pode resultar em produtos não conformes, colocando em risco a segurança do consumidor e a reputação da empresa.
Além disso, a calibração regular é um requisito para muitas certificações de qualidade, como ISO 9001. A conformidade com essas normas não apenas beneficia a imagem da empresa, mas também permite a confiança dos clientes em seus produtos e serviços. Isso é especialmente importante em um mercado competitivo, onde a qualidade é um diferencial significativo.
Outro ponto a ser considerado é a relação custo-benefício que a calibração pode proporcionar. Embora implique em custos, a calibração ajuda a evitar perdas consideráveis ocasionadas por medições incorretas que podem gerar retrabalho, desperdício de materiais ou danos a equipamentos, resultando em custos muito maiores a longo prazo.
Por fim, a calibração contribui para a melhoria contínua dos processos. Com medições confiáveis, as empresas podem realizar análises mais eficazes, identificar oportunidades de melhoria e adotar práticas de manutenção preditiva, aumentando a eficiência operacional e promovendo um ambiente de produção mais seguro e eficiente.
Tipos de Equipamentos que Precisam de Calibração
Diversos tipos de equipamentos requerem calibração para assegurar medições precisas e confiáveis. Abaixo, elencamos alguns dos principais tipos de equipamentos que necessitam desse cuidado, abrangendo diferentes setores da indústria.
1. Instrumentos de Medição de Peso: Balanças industriais e analíticas precisam ser calibradas regularmente para garantir que as medidas de massa estejam corretas. A precisão é crucial, especialmente em indústrias como a farmacêutica e a alimentícia, onde a quantidade de ingredientes pode impactar diretamente a qualidade do produto.
2. Termômetros e Termopares: Utilizados em diversas aplicações para medir temperatura, esses dispositivos devem ter sua precisão checada e ajustada frequentemente. Temperaturas incorretas podem afetar processos químicos e físicos, resultando em falhas de produção ou safra de produtos não conformes.
3. Manômetros: Equipamentos que medem pressão, como manômetros, devem ser calibrados para evitar leituras erradas que podem comprometer a segurança de sistemas industriais, especialmente em áreas de alta pressão e em equipamentos críticos como caldeiras e reatores.
4. Multímetros: Esses dispositivos versáteis medem tensão, corrente e resistência. A calibração é fundamental para garantir que os dados fornecidos sejam exatos, o que é essencial em diagnósticos elétricos e manutenção de equipamentos.
5. Equipamentos de Medição de Fluído: Incluindo fluxômetros e medidores de nível, esses equipamentos são cruciais em sistemas de controle de processos. A calibração garante que a quantidade de fluido medida ou controlada esteja dentro do esperado, prevenindo problemas operacionais.
6. Espectrômetros: Usados para medir a intensidade da luz em diferentes comprimentos de onda, esses dispositivos são comuns em laboratórios de pesquisa e controle de qualidade. Uma calibração incorreta pode levar a erros analíticos significativos.
7. Câmaras de Medição de Dimensões: Utilizadas para verificar tamanhos e dimensões de peças, especialmente na indústria automotiva e aeroespacial, a calibração é essencial para garantir que as peças produzidas estejam dentro das especificações.
Esses são apenas alguns exemplos de equipamentos que necessitam de calibração regular. A prática não só assegura precisão nas medições, mas também garante a conformidade com regulamentos e normas de qualidade que regem diversas indústrias.
Procedimentos para Realizar a Calibração Adequada
Realizar a calibração adequada de equipamentos de medição envolve um conjunto de procedimentos sistemáticos que garantem a precisão das medições e a conformidade com as especificações. A seguir, apresentamos os principais passos a serem seguidos durante o processo de calibração:
1. Planejamento: Antes de iniciar a calibração, é essencial elaborar um plano que inclua os equipamentos a serem calibrados, as condições ambientais (temperatura, umidade, etc.), e as normas aplicáveis. Esse planejamento deve incluir a definição da frequência de calibração, de acordo com o tipo de equipamento e as exigências regulatórias.
2. Preparação do Equipamento: Antes de proceder com a calibração, inspecione cada equipamento para verificar se estão em boas condições de funcionamento. Isso inclui checar por desgaste, sujeira ou danos. Equipamentos que não estejam em condições adequadas devem ser reparados antes da calibração.
3. Uso de Padrões Rastreáveis: Utilize padrões de referência que sejam rastreáveis a entidades metrológicas reconhecidas. Esses padrões devem ter uma precisão conhecida para garantir que as medições do equipamento sejam comparáveis e confiáveis.
4. Realização da Calibração: Execute os procedimentos de calibração conforme os protocolos estabelecidos. Isso envolve a comparação das leituras do equipamento com as do padrão de referência e o ajuste dos instrumentos para garantir que suas medições estejam na faixa especificada. É fundamental seguir as recomendações do fabricante durante este processo.
5. Documentação: Após a calibração, é imprescindível registrar todos os resultados e ajustes realizados. A documentação deve incluir a data da calibração, os padrões utilizados, as condições do ambiente durante o processo e qualquer anomalia ou ajuste feito. Esse registro é essencial para auditorias e para garantir a rastreabilidade do processo.
6. Testes Finais: Após a calibração, é importante realizar testes finais para assegurar que o equipamento esteja operando corretamente. Isso inclui verificar se as medições estão dentro das especificações exigidas e se o equipamento responde conforme o esperado a novas medições.
7. Revisão e Manutenção Periódica: Estabeleça um cronograma para revisões e manutenções periódicas, além de calibrações regulares. Isso ajuda a prolongar a vida útil do equipamento e a garantir a continuidade da precisão nas medições.
Esses passos, se seguidos corretamente, asseguram que a calibração dos equipamentos de medição seja realizada de forma eficaz, contribuindo para a qualidade e confiabilidade dos processos em que esses instrumentos são utilizados.
Fatores que Influenciam a Precisão na Calibração
A precisão na calibração de equipamentos de medição é influenciada por diversos fatores que devem ser considerados para garantir resultados confiáveis. Os principais fatores incluem:
1. Condições Ambientais: As condições em que a calibração é realizada, como temperatura e umidade, podem impactar significativamente os resultados. Por exemplo, flutuações de temperatura podem alterar as propriedades dos materiais, afetando as medições. Portanto, é essencial realizar a calibração em ambientes controlados sempre que possível.
2. Qualidade dos Padrões de Referência: A utilização de padrões de calibração com alta precisão e rastreabilidade garante que as medições sejam exatas. Padrões de baixa qualidade podem levar a resultados imprecisos, prejudicando todo o processo de calibração.
3. Técnica do Operador: A habilidade e a experiência do operador que realiza a calibração são aspectos críticos. Operadores devidamente treinados têm maior probabilidade de seguir os procedimentos corretamente e interpretar os resultados de forma adequada, minimizando erros no processo.
4. Condicionamento do Equipamento: Equipamentos de medição que não foram devidamente mantidos ou que apresentam desgaste podem resultar em medições imprecisas. A integridade do instrumento deve ser verificada regularmente para evitar que fatores mecânicos interfiram nas medições.
5. Intervalos de Calibração: A frequência com que a calibração é realizada também influencia a precisão. Equipamentos que não são calibrados regularmente podem acumular desvios ao longo do tempo, tornando as medições imprecisas. Estabelecer cronogramas de calibração adequados é essencial para manter a precisão dos instrumentos.
6. Método de Calibração: Diferentes métodos de calibração podem levar a variações nos resultados. É importante escolher o método mais apropriado para cada tipo de equipamento e aplicação, de acordo com as diretrizes do fabricante e normas reconhecidas.
7. Interferências Externas: Fontes de interferência, como campos eletromagnéticos ou vibrações, podem afetar a precisão das medições. Garantir que o ambiente de calibração esteja livre dessas influências é fundamental para obter resultados confiáveis.
8. Calibração de Múltiplos Pontos: A calibração em múltiplos pontos permite verificar a linearidade e a precisão do instrumento em diferentes faixas de operação. Isso é particularmente importante para equipamentos que operam em uma ampla gama de condições.
Considerar e controlar esses fatores é fundamental para garantir a precisão e a confiabilidade dos resultados durante o processo de calibração, assegurando que os equipamentos de medição funcionem adequadamente nas suas aplicações específicas.
Normas e Regulamentações para Calibração de Equipamentos
As normas e regulamentações para calibração de equipamentos de medição são essenciais para garantir a qualidade e a precisão dos resultados em diversas indústrias. Essas normas orientam as práticas de calibração e asseguram que os processos estejam em conformidade com os padrões internacionais e locais.
A seguir, destacamos algumas das principais normas e regulamentações relacionadas à calibração:
1. ISO 9001: Essa norma estabelece os requisitos para um sistema de gestão da qualidade e inclui diretrizes sobre a calibração de equipamentos. Empresas que buscam a certificação ISO 9001 devem demonstrar a eficácia de seus processos de calibração para assegurar a qualidade dos produtos e serviços oferecidos.
2. ISO/IEC 17025: Esta norma é especificamente voltada para laboratórios de ensaio e calibração. Ela estabelece requisitos para a competência técnica dos laboratórios e visa garantir que eles realizem calibrações precisas e consistentes. A certificação nesta norma é um indicativo de que o laboratório segue rigorosos padrões de qualidade.
3. NIST (National Institute of Standards and Technology): Nos Estados Unidos, o NIST fornece padrões e diretrizes para calibração e medições em vários setores. Seu papel é assegurar que as medições estejam alinhadas com padrões nacionais e internacionais, promovendo a consistência nas medições em todo o país.
4. EN ISO 10012: Esta norma internacional fornece orientações sobre a gestão de medições e está muito relacionada à calibração de equipamentos. Ela orienta a implementação de um sistema de gestão da medição eficaz, ajudando organizações a garantir que suas medições sejam rastreáveis e precisas.
5. Normas específicas por setor: Além das normas gerais, existem regulamentações específicas para diferentes setores. Por exemplo, na área farmacêutica, a ANVISA (Agência Nacional de Vigilância Sanitária) determina regulamentos que requerem que equipamentos de medição sejam calibrados e validados para assegurar a segurança e eficácia dos produtos.
6. Regulamentações Ambientais e de Segurança: Em indústrias onde a calibração é fundamental para a segurança, como a petroquímica e a nuclear, há regulamentações específicas que exigem calibragens rigorosas. Essas regulamentações visam proteger tanto os trabalhadores quanto o meio ambiente.
Cumprir com essas normas e regulamentações não apenas maximiza a precisão das medições, mas também assegura a integridade das operações da empresa, aumentando a confiança do cliente e a reputação no mercado. Além disso, a conformidade regulatória pode ser um diferencial competitivo, ajudando as empresas a se destacarem em mercados cada vez mais exigentes.
Benefícios da Calibração Regular para Empresas
A calibração regular de equipamentos de medição traz uma série de benefícios significativos para as empresas, contribuindo para a eficiência operacional e a qualidade dos produtos e serviços. Abaixo, listamos alguns dos principais benefícios que as organizações podem obter ao implementar práticas de calibração consistentes:
1. Precisão Aumentada: A calibração frequente assegura que os equipamentos de medição operem dentro das suas especificações, resultando em medições precisas. Isso é crucial para a qualidade dos produtos, pois medições imprecisas podem levar a desperdícios, retrabalhos e produtos não conformes.
2. Conformidade Regulamentar: Muitas indústrias estão sujeitas a regulamentos rigorosos que exigem calibração regular de equipamentos. Manter-se em conformidade com essas normas não apenas evita penalidades, mas também fortalece a reputação da empresa no mercado.
3. Redução de Custos: Embora a calibração envolva um investimento, ela pode resultar em economia a longo prazo, prevenindo falhas e retrabalhos. Ao garantir que os equipamentos trabalham corretamente, as empresas podem evitar paradas não planejadas e prejuízos relacionados à má qualidade dos produtos.
4. Aumento da Vida Útil dos Equipamentos: Calibrações regulares ajudam a identificar problemas mecânicos ou de desempenho antes que eles se tornem sérios. Isso não só melhora a eficiência dos equipamentos, mas também contribui para aumentar sua durabilidade, resultando em menores custos de manutenção e substituição.
5. Melhoria Contínua: A calibração regular é parte essencial de uma estratégia de melhoria contínua. Equipamentos calibrados garantem que os dados coletados sejam confiáveis, permitindo que as empresas identifiquem áreas para otimização e implementem melhorias efetivas nos processos.
6. Satisfação do Cliente: A entrega de produtos de alta qualidade depende da precisão dos equipamentos de medição. Com calibrações regulares, as empresas podem garantir que seus produtos atendam ou excedam as expectativas dos clientes, aumentando a satisfação e a fidelidade dos mesmos.
7. Aumento da Produtividade: Equipamentos que funcionam corretamente permitem que os processos sejam executados de forma mais eficiente. Isso pode levar a uma produção mais rápida e a um melhor uso dos recursos, resultando em maior produtividade geral.
8. Portfólio de Certificações: Empresas que mantêm padrões elevados de calibração podem obter certificações reconhecidas que destacam seu comprometimento com a qualidade. Isso pode ser um diferencial competitivo ao entrar em novos mercados ou quando se busca novos clientes.
Ao implementar um programa de calibração regular, as empresas não apenas garantem a precisão e a conformidade, mas também fortalecem sua posição no mercado tornando-se mais competitivas e eficientes.
A calibração de equipamentos de medição é um aspecto fundamental que não pode ser negligenciado nas operações empresariais.
Ao garantir a precisão e confiabilidade das medições, as empresas têm a oportunidade de melhorar a qualidade dos seus produtos, atender a regulamentações e aumentar a satisfação do cliente.
Além disso, a calibração regular contribui para a redução de custos e a prolongação da vida útil dos equipamentos, promovendo uma cultura de melhoria contínua.
Portanto, investir em práticas de calibração eficazes não é apenas uma questão de conformidade, mas uma estratégia inteligente para garantir a competitividade e o sucesso a longo prazo no mercado.