Calibração de instrumentos industriais aumenta precisão e segurança
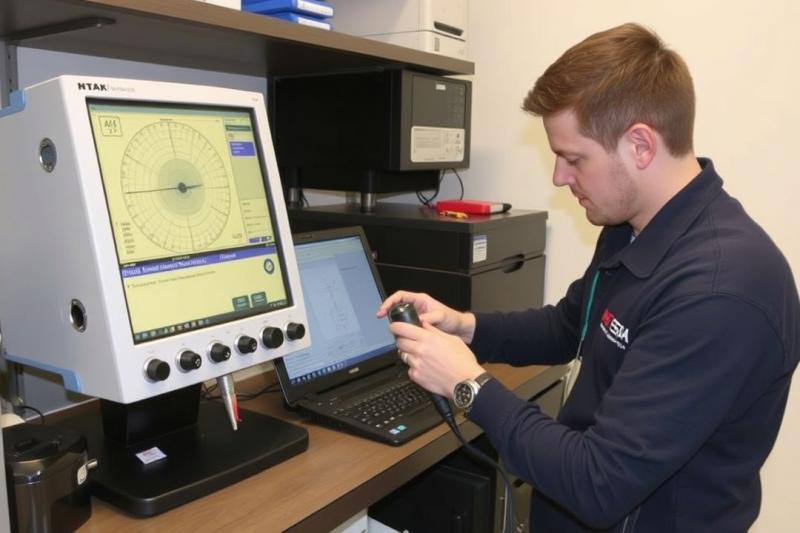
Por: Anderson - 25 de Junho de 2025
A calibração de instrumentos industriais é uma prática fundamental que assegura a precisão e a confiabilidade dos equipamentos utilizados em processos produtivos. Sem uma calibração adequada, as medições podem comprometer a qualidade dos produtos e a segurança das operações. Neste contexto, entender os aspectos relacionados à calibração torna-se crucial para as empresas que buscam otimizar seus processos e garantir conformidade com normas técnicas.
A importância da calibração para o setor industrial
A calibração de instrumentos industriais desempenha um papel crítico na garantia da precisão nas medições, essenciais para a qualidade dos produtos e a segurança das operações. Instruments como manômetros, termômetros e medidores de pressão, se não calibrados, podem resultar em erros que impactam a eficiência produtiva.
Além disso, a precisão nas medições é fundamental para atender às normas regulatórias e padrões de qualidade estabelecidos por órgãos governamentais e entidades normativas. A não conformidade pode acarretar em multas, retrabalhos ou, em casos severos, até na suspensão das atividades da empresa.
Outro aspecto importante é o impacto econômico. Investir em calibração regular pode reduzir custos a longo prazo, minimizando perdas decorrentes de produtos fora de especificação e evitando desperdícios de matéria-prima. Portanto, a calibração não é apenas uma questão de conformidade, mas também de eficiência e sustentabilidade financeira.
Por fim, a manutenção da calibração dos instrumentos também melhora a segurança operacional. Instrumentos imprecisos podem levar a falhas em sistemas de controle, resultando em condições que potencialmente colocam em risco a segurança dos colaboradores e das instalações.
Principais tipos de instrumentos que precisam de calibração
Existem diversos tipos de instrumentos utilizados na indústria que requerem calibração regular para assegurar suas medições precisas e confiáveis. Entre eles, destaca-se os medidores de pressão, que são cruciais para monitorar e controlar pressões em sistemas de fluidos.
Outro tipo importante é o termômetro, utilizado em aplicações que vão desde processos de aquecimento até controle de temperatura em ambientes refrigerados. A precisão na medição de temperatura é essencial para manter a qualidade do produto final.
Medidores de vazão também são críticos, pois ajudam a medir a quantidade de fluido que passa por um ponto específico em um determinado período. Uma calibragem adequada desses instrumentos é fundamental para garantir que processos de produção ocorram de forma eficiente.
Adicionalmente, os instrumentos de medição elétrica, como multímetros e osciloscópios, exigem calibração regular para garantir a precisão nas medições de tensão, corrente e resistência. Falhas na calibração desses dispositivos podem afetar a performance de sistemas elétricos.
Por fim, a calibração de balanças industriais é igualmente essencial, especialmente em setores como alimentos e farmacêutico, onde a precisão no peso dos ingredientes pode impactar diretamente na qualidade e segurança dos produtos.
Processo de calibração: etapas e cuidados
O processo de calibração envolve uma série de etapas metódicas que garantem que os instrumentos funcionem de acordo com as especificações estabelecidas. A primeira etapa é a verificação inicial do instrumento, onde se avalia seu estado físico e funcionalidade antes de qualquer ajuste.
Em seguida, realiza-se a comparação das medições do instrumento com um padrão de referência, que é denominado de instrumento de calibração. Essa comparação deve ser feita em condições controladas e utilizando os mesmos parâmetros, como temperatura e umidade.
Após a comparação, se forem detectadas discrepâncias, ajustes serão feitos no instrumento para que suas medições se alinhem ao valor padrão. Essa etapa pode requerer conhecimento técnico específico, especialmente para instrumentos mais complexos.
Uma vez que o instrumento esteja ajustado, é crucial realizar novos testes para confirmar que a calibração foi efetiva. Esses testes asseguram que o instrumento está agora medindo corretamente dentro dos limites especificados.
Além disso, é importante documentar todo o processo de calibração. Manter registros detalhados ajuda a monitorar o desempenho do instrumento ao longo do tempo e garante a rastreabilidade das calibragens, o que é vital para auditorias e conformidade com normas.
Por fim, recomenda-se a realização da calibração em intervalos regulares, conforme o fabricante do instrumento ou as exigências normativas. Isso assegura que os instrumentos permaneçam confiáveis e prontos para uso em processos críticos.
Frequência recomendada para calibrações
A frequência recomendada para calibrações varia de acordo com vários fatores, incluindo o tipo de instrumento, a aplicação específica, as condições de uso e as diretrizes do fabricante. Por exemplo, instrumentos utilizados em ambientes críticos ou que operam sob condições severas, como variações extremas de temperatura e umidade, geralmente requerem calibrações mais frequentes.
Para instrumentos de uso geral em ambientes controlados, a calibração pode ser realizada anualmente. No entanto, para equipamentos que desempenham um papel crucial na qualidade do produto ou na segurança operacional, recomenda-se que a calibração ocorra semestralmente ou até mesmo trimestralmente.
Além disso, empresas que seguem normas específicas, como ISO 9001 ou ISO 17025, devem adotar um calendário rigoroso de calibrações para garantir a conformidade com as exigências regulatórias. Tais normas frequentemente estabelecem a necessidade de um plano de manutenção preventiva que inclua a calibração regular dos instrumentos.
Outro fator a ser considerado é o histórico de desempenho do instrumento. Se um instrumento tem apresentado leituras inconsistentes ou se foi submetido a choques físicos, sua calibração deve ser feita imediatamente, independentemente do intervalo regular estabelecido.
Em resumo, embora existam diretrizes gerais sobre a frequência de calibração, é importante que cada empresa avalie suas necessidades específicas e estabeleça um cronograma de calibrações adaptado às suas operações e requisitos de qualidade.
Como escolher um laboratório de calibração confiável
Escolher um laboratório de calibração confiável é fundamental para garantir que os instrumentos sejam calibrados com precisão e de acordo com as normas estabelecidas. O primeiro passo é verificar se o laboratório possui certificações reconhecidas, como ISO 17025, que atesta a competência técnica e a qualidade dos serviços prestados.
É importante também avaliar a experiência e a reputação do laboratório no mercado. Pesquise sobre a sua história, o número de anos de operação e referências de outras empresas que utilizam seus serviços. Laboratórios com uma longa trajetória geralmente oferecem maior segurança quanto à qualidade do trabalho realizado.
Outro ponto a considerar é a gama de instrumentos que o laboratório é capaz de calibrar. Um laboratório competente deve oferecer serviços para uma ampla variedade de instrumentos, adequando-se às necessidades específicas da sua operação. Isso inclui desde instrumentos simples até dispositivos altamente complexos.
Além disso, o suporte técnico e o atendimento ao cliente são aspectos essenciais. Escolha um laboratório que ofereça um bom suporte, esclarecendo suas dúvidas e fornecendo informações claras sobre o processo de calibração, prazos e custos envolvidos.
Por fim, compare preços, mas sem comprometer a qualidade. Certifique-se de que o custo dos serviços está alinhado com a qualidade oferecida. Muitas vezes, preços muito baixos podem estar vinculados a compromissos na qualidade da calibração.
Normas e regulamentações relacionadas à calibração de instrumentos
As normas e regulamentações relacionadas à calibração de instrumentos são fundamentais para garantir a precisão e a confiabilidade das medições em ambientes industriais. Entre as principais normas internacionais, destaca-se a ISO/IEC 17025, que estabelece requisitos gerais para a competência de laboratórios de ensaio e calibração.
Além disso, muitas indústrias seguem regulamentações específicas de qualidade, como a ISO 9001, que enfatiza a importância da calibração como parte do controle de qualidade do processo produtivo. Essas normas exigem a implementação de um sistema de gestão que inclua a calibração regular de instrumentos como parte de suas práticas operacionais.
Outras normas, como a ANSI/NCSL Z540 e a ISO 10012, também fornecem diretrizes sobre a gestão do processo de medição, incluindo a calibração. Essas normas abordam aspectos como rastreabilidade das medições, registros de calibração e normas de qualidade que os laboratórios devem seguir.
Na área regulamentar, órgãos governamentais e agências regulamentadoras em diferentes locais podem definir obrigações adicionais para a calibração de instrumentos, especialmente em setores críticos como saúde, alimentos e farmacêuticos, onde a precisão nas medições pode impactar a segurança do consumidor.
Portanto, é essencial que as empresas estejam cientes das normas e regulamentações relevantes para sua área de atuação e garantam que seus processos de calibração sejam realizados de acordo com essas diretrizes, a fim de promover a conformidade e a qualidade dos produtos e serviços oferecidos.
A calibração de instrumentos industriais é um aspecto crucial para garantir a precisão, segurança e eficiência em processos produtivos.
Ao compreender a importância da calibração, reconhecer os tipos de instrumentos que necessitam deste processo, e seguir as etapas adequadas, as empresas podem otimizar suas operações e assegurar a qualidade de seus produtos.
Manter uma frequência adequada de calibrações e escolher laboratórios confiáveis também é fundamental para a conformidade com normas e regulamentações.
Em última análise, investir em calibração não apenas protege a integridade dos processos e produtos, mas também promove a confiança e a satisfação do cliente.